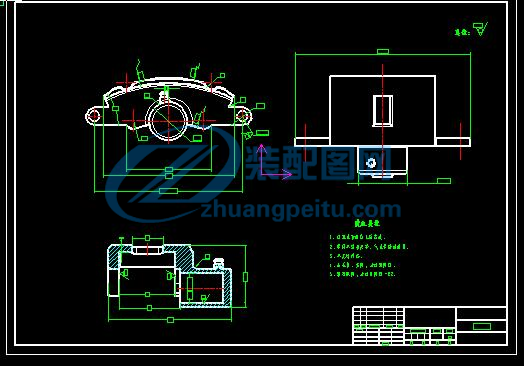

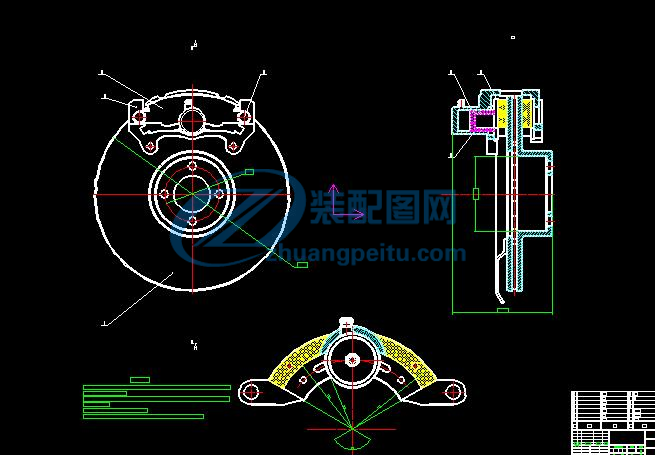
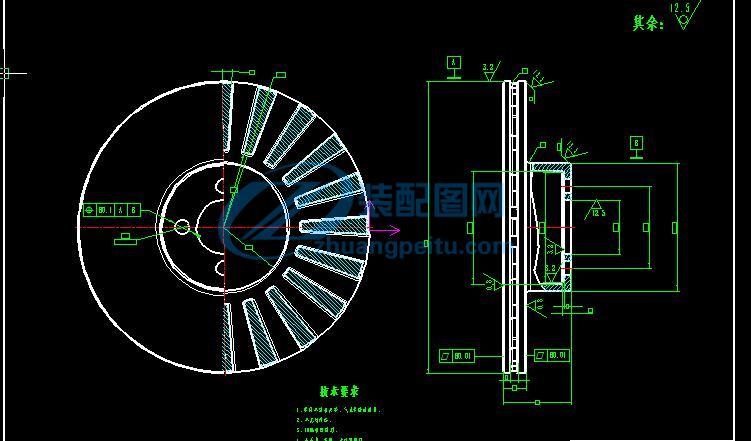
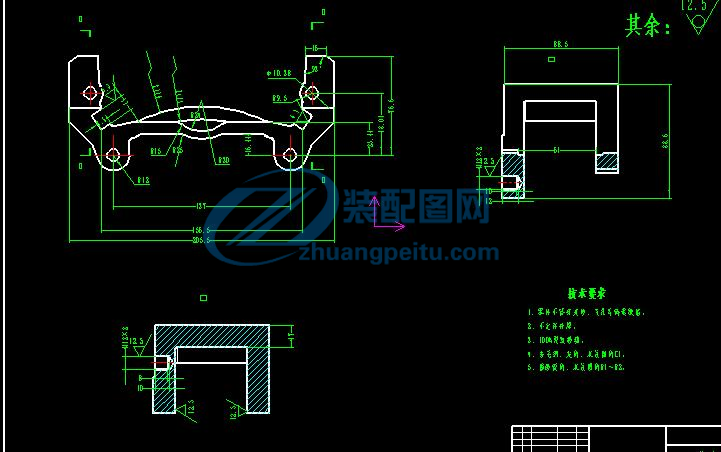
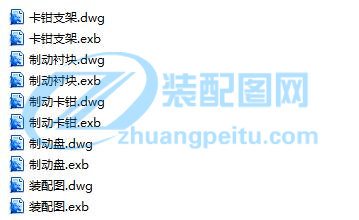
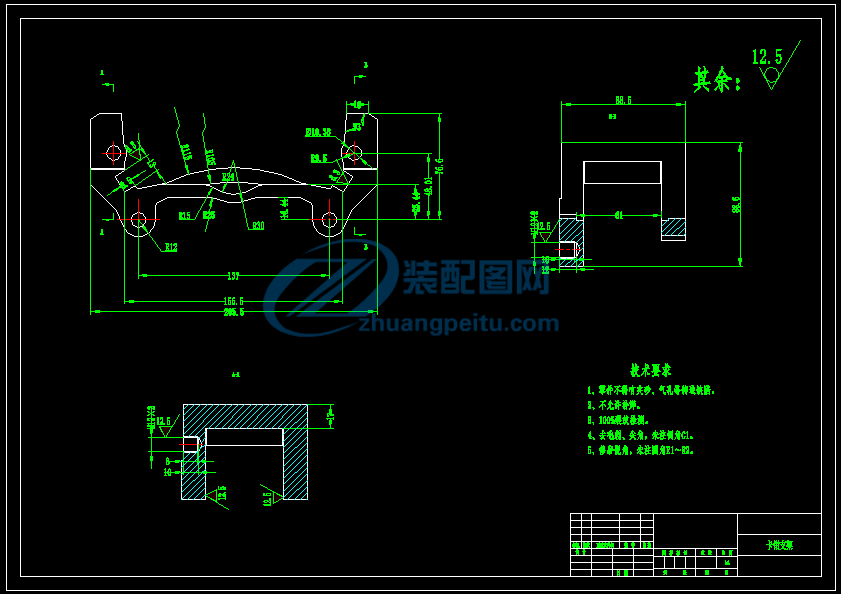
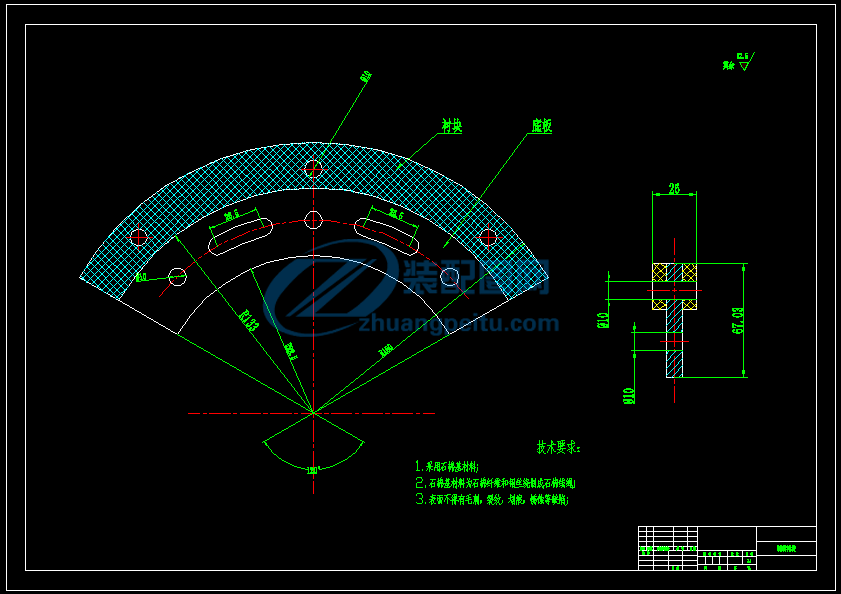
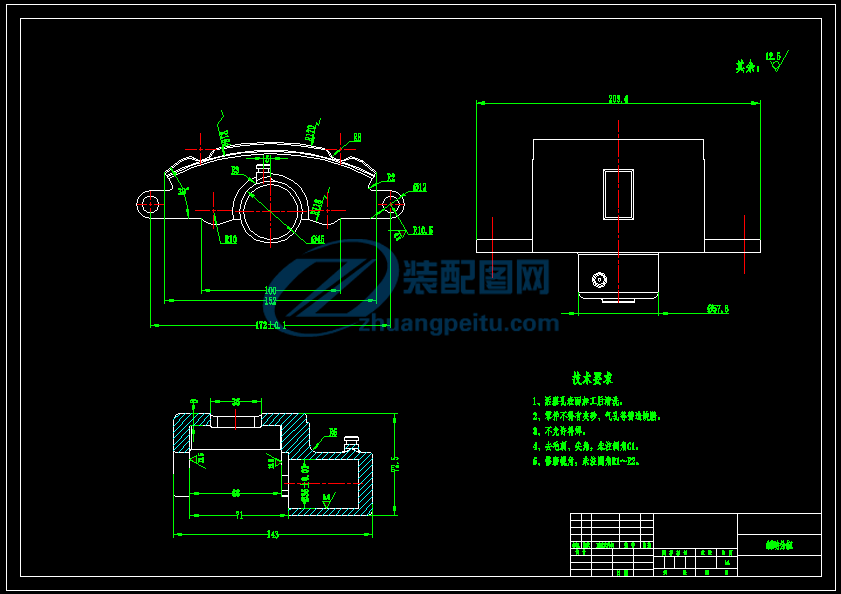
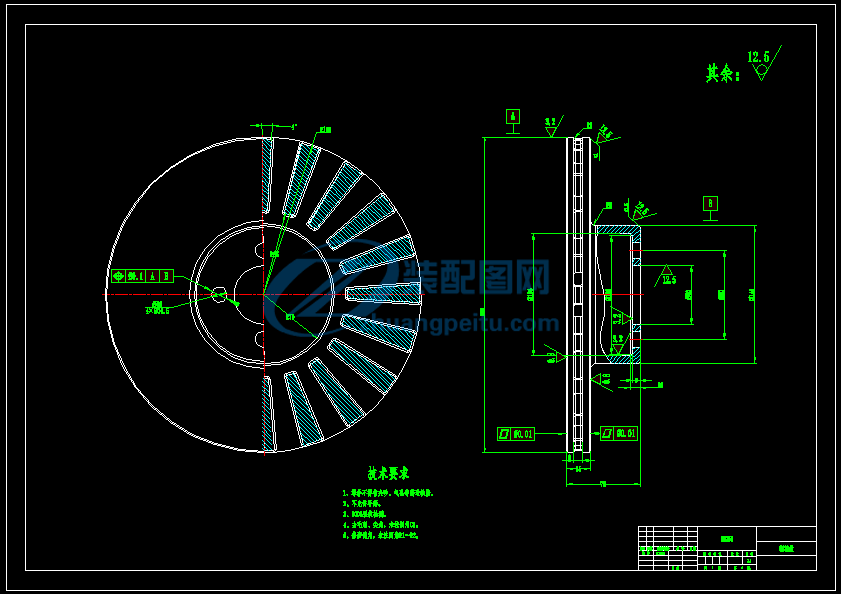

3 汽車整車參數(shù)計算華晨寶馬三系 整備質量 1510Kg滿載質量 滿載質心高 軸距 滿載質心距前軸距離最大車速 輪胎規(guī)格1990Kg 550mm 2810mm 1405mm 210km/h 225/50 R17即車輪名義斷面寬度為 225mm,扁平率為 50%,輪轂名義直徑為 17 英寸,轉化過來為 17*25.4=431.8mm故車輪有效半徑為 r=431.8/2+225*50%=328.4mm4 制動系的主要參數(shù)及其選擇4.1 制動力與制動力分配系數(shù)設前后輪制動器的制動力為 、 ,理想的前后輪制動器動力分配曲線公式:1fF2f滿載時:)]h(-4h[211fg21fg2gf FGLLGF???式中: —前軸車輪的制動器制動力,Nf1—后軸車輪的制動器制動力,Nf2FG—汽車重力,N — 汽車質心離后軸距離,mm2L— 汽車質心高度 ,mm ghL—汽車軸距,mm代入數(shù)據(jù): ]25.08.941-8.910254.5.0891[2 1f12f )( FFF ??????對于轎車而言,滿載時的同步附著系數(shù) ,滿足要求6.φ0?選定 0.7φ?g20hL??L2g0φ?代入數(shù)據(jù): 63.81.457????所以制動分配系數(shù) β=0.634.2 制動強度和附著系數(shù)利用率①當 7.0φ?最大制動力 1365.4N0.7981??GFB制動強度 φq?附著系數(shù)利用率 1??②當 時,前輪先抱死0φ<最大制動力 5.0φ-7.405.14189h)φ(Lg02 ??????)(GFB制動強度 5.0φ-7.1.405h)φ(Lqg02 ??????)(附著系數(shù)利用率 .-41)(g02 )(?③當 時,后輪先抱死0φ>最大制動力 5.07-φ405.1418.9h)φ(Lg01 ??????)(GFB附著系數(shù)利用率 .-)-(g01 )(?4.3 制動器最大制動力矩按所遇路面良好 0.8φ?一個前后輪的最大制動力矩分別為: MNLGT ????? 601.789324.085.70-4.18.29r)qh(maxfeg12 )( MN???? 9.3673.0-axf-21?4.4 制動因數(shù)對于鉗盤式制動器,設兩側制動塊對制動盤的壓緊力均為 P,則制動盤在其兩側工作面的作用半徑上所受的摩擦力為 2 ,此處 f 為盤與制動襯塊間的摩fp擦系數(shù),于是鉗盤式制動器的制動器因數(shù)為 BF=2f=2X0.3=0.6。4.5 駐車計算圖 4 汽車在上坡路上停駐時的受力情況根據(jù)受力圖不難得出停駐時的后橋附著力為: )( ?sinLhgφmg1a2??COSF汽車在下坡路上停駐時的后橋附著力為: )( ?sinLh-gφg1a2SF??汽車可能停駐的極限上坡路傾角 ,可根據(jù)后橋上的附著力與制動力相等的條1?件求得,即由 1a1g1a sinmsiLhgφm???)( COS得到 g11φh-Larctn??式中, 是保證汽車上坡行駛的縱向穩(wěn)定性的極限坡路傾角。1?代入數(shù)據(jù) 5.08-1.24arctn1??得 ?37.?同理可得下坡極限坡路傾角 g11φhLarctn????代入數(shù)據(jù) 0.582.14arctn1????得 ??7.91?5 盤式制動器制動器的設計5.1 制動盤直徑制動盤直徑 D 應盡可能取大些,這時制動盤的有效半徑得到增加,可以減小制動鉗的夾緊力,降低襯塊的單位壓力和工作溫度。受輪輞直徑的限制,制動盤的直徑通常選擇為輪輞直徑的 70%~79%,取 75%。由于輪胎規(guī)格為 225/50 R17 17 英寸即 431.8mm,所以制動盤直徑D=431.8×75%=323.85,為方便加工及保證尺寸的一致性,在此將尺寸取整,故取 320mm;驗算:320/431.8*100%=74.1%,滿足 70%~79%要求。制動盤直徑為 70%~79%輪輞直徑,根據(jù)輪輞提供給制動器的可利用空間,并本著制動盤直徑盡可能大的原則及運動時不發(fā)生干涉。初選制動盤的直徑d=140mm。5.2 制動盤厚度制動盤厚度 h 對制動盤質量和工作時的溫升有影響,為使質量小些,制動盤不宜取得很大,為了減少溫升,制動盤厚度又不宜取得過小,制動盤可以作成實心的,或者為了散熱通風需要在制動盤中間鑄出通風孔道,而我所選的車型制動器采用的便是通風盤式,而通風式制動盤厚度取為 20~ 50mm,采用較多的是 20~ 30mm,取 25mm。5.3 摩擦襯塊外半徑 內半徑2R1推薦摩擦襯塊外半徑 R2,與內半徑 R 的比值不大于 1.5。若此比值偏大,工作時襯塊的外緣與內側圓周速度相差較多,磨損不均勻,接觸面積減少,最終將導致制動力矩變化大。取 ,由于摩擦襯塊外徑 略小于制動盤半徑 = =1602.1?R22D30故取 160mm所以 m132.601?R5.4 制動襯塊工作面積 A由于制動襯塊為扇形,選定其到圓心的夾角為 60°所以 2221 cm409.163.1-360??????)π ()π ( ?RA5.5 摩擦襯塊摩擦系數(shù) f選擇摩擦襯塊時,不僅希望其摩擦系數(shù)要高些,更要求其熱穩(wěn)定性要好,受溫度和壓力的影響要小。不能單純地追求摩擦材料的高摩擦系數(shù),各種制動器用摩擦材料的摩擦系數(shù)的穩(wěn)定值約為 0.3~0.5, 一般來說,摩擦系數(shù)愈高的材料,其耐磨性愈差,所以在制動器設計時并非一定要追求高摩擦系數(shù)的材料。在假設的理想條件下計算制動器的制動力矩,為使計算結果接近實際,取f=0.3。另外,在選擇摩擦材料時,應盡量采用減少污染和對人體無害的材料,故選用粉末冶金材料。5.6 制動襯塊的設計計算假定襯塊的摩擦面全部與制動盤接觸,且各處單位壓力分布均勻,則制動器的制動力矩為 RFM0f2??式中 f 為摩擦系數(shù); 為單側制動塊對制動盤的壓緊力;R 為作用半徑。對0于常見的具有扇形摩擦表面的襯塊,其徑向寬度不是很大,取 R 等于平均半徑或有效半徑 ,在實際中已經足夠精確。mRe平均半徑 為m m5.14620321m???R式中, , 為摩擦襯塊扇形表面的外半徑和內半徑。2R1有效半徑 是扇形的面積中心至制動盤中心的距離,eRm92.1465.])83.01([4]m1[34)(32 2221e ????????R)()(式中, 8.06m21R因為 m<1, ,故 ,且 m 越小,兩者差值越大。41<)( ?eR>應當指出,若,m 過小,即扇形的徑向的寬度過大,襯塊摩擦面上各不同半徑處的滑磨速度相差太遠,磨損將不均勻,因而單位壓力分布均勻這一假設條件不能成立, 則上述計算方法也就不適用。m 值一般不小于 0.65。制動盤工作面的加工精度應達到下述要求:平面度公差為 0.012mm,表面粗糙度 R,值為 0.7 ~1.3μm,兩摩擦表面的平行度公差不應大于 0.05mm,制動盤的端面圓跳動公差不應大于 O.03mm。通常制動盤采用摩擦性能良好的珠光體灰鑄鐵制造。為保證足夠的強度和耐磨性能,其牌號不應低于 HT250。5.7 襯片磨損特性的計算摩擦襯片(襯塊)的磨損受溫度、摩擦力、滑磨速度、制動鼓(制動盤)的材質及加工情況,以及襯片(襯塊)本身材質等許多因素的影響,因此在理論上計算磨損性能極為困難。但試驗表明,影響磨損的最重要的因素還是摩擦表面的溫度和摩擦力。從能量的觀點來說,汽車制動過程即是將汽車的機械能(動能和勢能)的一部分轉變?yōu)闊崃慷纳⒌倪^程。在制動強度很大的緊急制動過程中,制動器幾乎承擔了汽車全部動能耗散的任務。此時,由于制動時間很短,實際上熱量還來不及逸散到大氣中就被制動器所吸收,致使制動器溫度升高。這就是所謂制動器的能量負荷。能量負荷越大,則襯片(襯塊)的磨損越嚴重。對于盤式制動器的襯塊,其單位面積上的能量負荷比鼓式制動器襯片大許多倍,所以制動盤的表面溫度比制動鼓的高。各種汽車的總質量及其制動襯片(襯塊)的摩擦面積各不相同,因而有必要用一種相對的量作為評價能量負荷的指標。目前,各國常用的指標是比能量耗散率,即單位時間內襯片(襯塊)單位摩擦面積耗散的能量,通常所用的計量單位為 。比能量耗散率有時也稱為單位功負荷,或簡稱能量負荷。2m/W雙軸汽車的單個前輪及后輪制動器的比能量耗散率分別為 ??12a1t4meAV)( ??)(te21a2)(jt21V??式中, --汽車總質量(t)am----汽車回轉質量換算系數(shù);?--制動器初速度和終速度(m/s) ;21V、j--制動減速度( ) ;2s/m--前、后制動器襯片(襯塊)的摩擦面積( ) ;21A、 2mβ--制動力分配系數(shù)。在緊急制動到停車的情況下, ,并認為 ,故02?V1???1at4meA)(t2a??據(jù)有關文獻推薦,鼓式制動器的比能量耗散率以不大于 1.8 為宜,2m/W計算時取堿速度 j=0.6g。制動初速度 :乘用車用 100km/h(27. 8m/s);總質量1V3.5t 以下的商用車用 80km/h(22.2m/s);總質量 3.5t 以上的商用車用65km/h(18m/s)。乘用車的盤式制動器在同上的 和 j 的條件下,比能量耗散率1V應不大于 6.0 。對于最高車速低于以上規(guī)定的制動初速度的汽車,按上2m/W述條件算出的 e 值允許略大于 1.8 。比能量耗散率過高不僅引起襯片2m/W(襯塊)的加速磨損,且有可能使制動鼓或制動盤更早發(fā)生龜裂。即乘用車的盤式制動器在 (27.8m/s)和 j=0.6g 條件下,h/k10?V由于設計驅動輪制動器僅計算后摩擦襯塊的摩擦特性代入數(shù)據(jù)得s73.4896.02t??221 m/37.16.0eW?222 /-41073.8.9e??)(另一個磨損特性指標是襯片(襯塊)單位摩擦面積的制動器摩擦力,化摩擦力越大,則磨損越嚴重。單個車輪制動器的比摩擦力為RAM??f式中, 為單個制動器的制動力矩;R 為襯塊平均半徑 或有效半徑 ;?MmReA 為單個制動器的襯片(襯塊)摩擦面積。當前輪處于最大制動力矩時,代入數(shù)據(jù)為:23/0.541.69307f NRA????當后輪處于最大制動力矩時,代入數(shù)據(jù)為:23m/95.4105.6789f NRAM????6 制動器主要零部件的結構設計6.1 制動盤制動盤結構形狀有平板形和禮帽形,由于所設計的是鉗盤式制動器,故采用后者即禮帽形制動盤,其圓柱部分長度取決于布置尺寸。為了改善冷卻,所設計的鉗盤式制動器的制動盤鑄成中間有徑向通風槽的雙層盤,可大大增加散熱面積,但盤的整體厚度較大。制動盤工作面的加工精度應達到下述要求:平面度小于等于 0. 01mm,表面粗糙度值小于等于 0.06mm,兩摩擦表面的不平行度小于等于 0.01mm,制動盤的端面圓跳動小于等于 0.03mm。6.4 摩擦材料制動摩擦材料應具有高而穩(wěn)定的摩擦系數(shù),抗熱衰退性能好,不能在溫度升到某一數(shù)值后摩擦系數(shù)突然急劇下降,材料的耐磨性好,吸水率低,有較高的耐擠壓和耐沖擊性能;制動時不產生噪聲和不良氣味,應盡量采用少污染和對人體無害的摩擦材料。經過綜合考慮,制動盤采用摩擦性能良好的珠光體灰鑄鐵鑄造,為保證足夠的強度和耐磨性能,其牌號為 HT250。摩擦襯塊選用減少污染和對人體無害的粉末冶金材料。7 制動驅動機構的設計與計算6.2 制動鉗制動鉗由球墨鑄鐵 QT400-18 制造,做成整體的,其外緣留有開口,以便不必拆下制動器便可檢查或更換制動塊。制動鉗體應有高的強度和剛度。在鉗體中加工出制動油缸。為了減少傳給制動液的熱量,將杯形活塞的開口端頂靠制動塊的背板?;钊射撝圃?,為了提高耐磨損性能,活塞的工作表面要進行鍍鉻處理。6.3 制動塊制動塊由背板和摩擦襯塊構成,兩者直接牢固地壓嵌或鉚接或連接在一起。襯塊多為扇形,也有矩形、正方形或長圓形的?;钊麘軌鹤”M量多的制動塊面積,以免襯塊發(fā)生卷角而引起尖叫聲。制動塊背板由鋼板制成。為了避免制動時產生的熱量傳給制動鉗而引起制動液氣化和減小制動噪聲,可在摩擦襯塊與背板之間或在背板后粘(或噴涂)一層隔熱減震墊(膠)。由于單位壓力大和工作溫度高等特點,摩擦襯塊的磨損較快,因此其厚度較大。一般情況下,輕型汽車的摩擦塊厚度在 7.5 mm~16 mm 之間,中、重型汽車的摩擦襯塊的厚度在 14 mm~22 mm 之間。許多盤式制動器裝有摩擦襯塊達到磨損極限時的報警裝置,以便能及時更換摩擦襯塊。7.1 制動驅動機構的形式制動驅動機構將來自駕駛員或其它力源的力傳給制動器,使之產生制動力矩。根據(jù)制動力源的不同,制動驅動機構一般可分為簡單制動、動力制動和伺服制動三大類。根據(jù)制動器各方面綜合考慮采用液壓市制動驅動機構液壓式驅動機構:優(yōu)點:a.制動時可以得到必要安全性,因為液壓系統(tǒng)內系統(tǒng)內壓力相等,左右輪制動同時進行;b.易保證制動力正確分配到前、后輪,因為前、后輪分泵可以做出不同直徑;c.車振或懸架變形不發(fā)生自行制動;,d.不須潤滑和時常調整;缺點:a 當管路一處泄漏,則系統(tǒng)失效;b 低溫油液變濃,高溫則汽化;c 不可長時間制動。但綜合來看,油壓制動還是可取的,且得到了廣泛的應用。7.2 分路系統(tǒng)為了提高制動工作可靠性,應采用分路系統(tǒng),即全車的所有行車制動器的液壓或氣壓管路分為兩個或更多的互相獨立的回路,其中一個回路失效后,仍可利用其它完好的回路起制動作用。雙軸汽車的雙回路制動系統(tǒng)有以下常見的五種分路形式:圖 4 分路系統(tǒng)1)一軸對一軸(Ⅱ)型,如圖 a 所示,前軸制動器與后橋制動器各用一個回路(“Ⅱ型”是其形象的簡稱,下同)。2)交叉(X)型,如圖 b 所示,前軸的一側車輪制動器與后橋的對側車輪制動器同屬一個回路。3)一軸半對半軸(HI)型,如圖 c 所示,兩側前制動器的半數(shù)輪缸和全部后制動器輪缸屬于一個回路,其余的前輪缸則屬于另一回路。4)半軸一輪對半軸一輪(LL)型,如圖 d 所示,兩個回路分別對兩側前輪制動器的半數(shù)輪缸和一個后輪制動器起作用。5)雙半軸對雙半軸(HH)型,如圖 e 所示。每個回路均只對每個前、后制動器的半數(shù)輪缸起作用。Ⅱ型的管路布置較為簡單,可與傳統(tǒng)的單輪缸(或單制動氣室)鼓式制動.器配合使用,成本較低,目前在各類汽車特別是貨車上用得最廣泛。這種形式若后制動回路失效,則一旦前輪抱死即極易喪失轉彎制動能力。對于采用前輪驅動因而前制動器強于后制動器的轎車,當前制動回路失效而單用后橋制動時,制動力將嚴重不足(小于正常情況下的一半),并且若后橋負荷小于前軸,則踏板力過大時易使后橋車輪抱死而汽車側滑。X 型的結構也很簡單。直行制動時任一- 回路失效,剩余總制動力都能保持正常值的 50%。但是,一旦某一管路損壞造成制動力不對稱,此時前輪將朝制動力大的一邊繞主銷轉動,使汽車喪失穩(wěn)定性。因此,這種方案適用于主銷偏移距為負值(達 20mm)的汽車上。這時,不平衡的制動力使車輪反向轉動,改善了汽車穩(wěn)定性。HI、HH、LL 型結構都比較復雜。LL 型和 HH 型在任一回路失效時,前、后制動力比值均與正常情況下相同。LL 型和 HH 型的剩余總制動力可達正常值的50%左右。HI 型單用一軸半回路時剩余制動力較大,但此時與 LL 型一樣,緊急制動情況下后輪很容易先抱死。所以本次設計選擇 X 型的布置方案。8 液壓制動驅動機構的設計計算8.1 制動輪缸直徑 d 的確定制動輪缸對制動蹄(塊)施加的張開力 與輪缸直徑 d 和制動管路壓力 p 的0F關系為 )/(4d0pπ?制動管路壓力一般不超過 10—12MPa,對盤式制動器可更高。壓力越高,對管路(首先是制動軟管及管接頭)的密封性要求越嚴格,但驅動機構越緊湊。輪缸直徑 d 應在標準規(guī)定的尺寸系列中選(HG2865-1997),具體為19mm、22mm、24mm、25mm、28mm、30mm、32mm、35mm、38mm、40mm、45mm、50mm、55mm。我們這里油壓選取 12MPa,代入數(shù)據(jù)得到后輪輪缸直徑 45mm,前輪輪缸直徑為 35mm。8.2 制動主缸直徑 的確定0d第 i 個輪缸的工作容積為??n1i2id4?πV式中, 為第 i 個輪缸活塞的直徑;n 為輪缸中活塞的數(shù)目; 為第 i 個輪缸id i?活塞在完全制動時的行程,初步設計時,制動器可取 =2.0—2.5mm,這里取i?=2mmi?前輪制動器單個輪缸工作容積 321wm194354??πV后輪制動器單個輪缸工作容積 32278π輪缸的總容積:=2(3178+1924)10204 ??MV1w2m在初步設計時,制動主缸的工作容積可取為:對于乘用車 V1.0?主缸活塞行程 和活塞直接 為0S0d004SVπ?一般 =(0.8—1.2) 。0S0d我們這里取 0?主缸的直徑 應符合 QC/T311—1999 中規(guī)定的尺寸系列,具體為0d19mm、22mm、26mm、28mm、32mm、35mm、38mm、40mm、45mm。代入數(shù)據(jù)得到主缸直徑得300 m4.12.d4???SVπ m27.4d0?S查表后取 26mm,即 =26mm0d8.3 制動踏板力制動踏板力 為PFk1ipd420)(π ??P式中, 為踏板機構的傳動比( =4-7) ; 為踏板機構及液壓主缸的機械pi pi效率,可取 =0.82—0.86,這里我們取 0.85;K 為真空助力器增力背數(shù),這里?我們取 5。代入數(shù)據(jù):NFP 82.951.01264k1ipd420 ?????π)(π ?制動踏板力應滿足以下要求:最大踏板力一般為 500N(轎車)或 700N(貨車)。設計時,制動踏板力可在 200~350N 的范圍內選取。8.4 制動踏板工作行程)( 0210pi???S式中, 為主缸中推桿與活塞間的間隙,一般 =1.5—2.0mm,這里取01? 01?; 為主缸活塞的空行程,即主缸活塞從不工作的極限位置到使m8.01?2其皮碗完全封堵主缸上的旁通孔所經過的行程。代入數(shù)據(jù)m14928.65i0210p ??????)()( ?S制動器調整正常時的踏板工作行程 Sp,只應占計及制動襯片(襯塊)的容許磨損量在內的踏板行程的 40%-60%。為了避免空氣侵入制動管路,在計算制動主缸活塞回位彈簧(同時也是回油閥彈簧)時,應保證踏板放開后,制動管路中仍保持 0.05--0. 14MPa 的殘余壓力。踏板行程(計人襯片或襯塊的允許磨損量)對轎車最大應不大于100~150mm,對貨車不大于 180mm。此外,作用在制動手柄上的力對轎車最大不大于 400N,對貨車不大于 600N;制動手柄行程對轎車最大不大于 160mm,對貨車不大于 220mm。3 汽車整車參數(shù)計算華晨寶馬三系 整備質量 1510Kg滿載質量 滿載質心高 軸距 滿載質心距前軸距離最大車速 輪胎規(guī)格1990Kg 550mm 2810mm 1405mm 210km/h 225/50 R17即車輪名義斷面寬度為 225mm,扁平率為 50%,輪轂名義直徑為 17 英寸,轉化過來為 17*25.4=431.8mm故車輪有效半徑為 r=431.8/2+225*50%=328.4mm4 制動系的主要參數(shù)及其選擇4.1 制動力與制動力分配系數(shù)設前后輪制動器的制動力為 、 ,理想的前后輪制動器動力分配曲線公式:1fF2f滿載時:)]h(-4h[211fg21fg2gf FGLLGF???式中: —前軸車輪的制動器制動力,Nf1—后軸車輪的制動器制動力,Nf2G—汽車重力,N — 汽車質心離后軸距離,mm2L— 汽車質心高度 ,mm ghL—汽車軸距,mm代入數(shù)據(jù): ]25.08.941-8.910254.5.0891[2 1f12f )( FFF ??????對于轎車而言,滿載時的同步附著系數(shù) ,滿足要求6φ0?選定 0.7φ?g20hL??20φ?代入數(shù)據(jù): 63.81.457????所以制動分配系數(shù) β=0.634.2 制動強度和附著系數(shù)利用率①當 7.0φ?最大制動力 1365.4N0.7981??GFB制動強度 q附著系數(shù)利用率 ??②當 時,前輪先抱死0φ<最大制動力 5.0φ-7.405.14189h)φ(Lg02 ????)(FB制動強度 .-)(qg02??)(附著系數(shù)利用率 5.0φ-7.405.1h)φ(g02 ????)(L?③當 時,后輪先抱死0φ>最大制動力 5.07-φ405.1418.9h)φ(Lg01 ??????)(GFB附著系數(shù)利用率 .-)-(g01 )(?4.3 制動器最大制動力矩按所遇路面良好 0.8φ?一個前后輪的最大制動力矩分別為: MNLGT ????? 601.789324.085.70-4.1.29r)qh(maxfeg12 )( MN???? 9.36783.0-axf-21?4.4 制動因數(shù)對于鉗盤式制動器,設兩側制動塊對制動盤的壓緊力均為 P,則制動盤在其兩側工作面的作用半徑上所受的摩擦力為 2 ,此處 f 為盤與制動襯塊間的摩fp擦系數(shù),于是鉗盤式制動器的制動器因數(shù)為 BF=2f=2X0.3=0.6。4.5 駐車計算圖 4 汽車在上坡路上停駐時的受力情況根據(jù)受力圖不難得出停駐時的后橋附著力為: )( ?sinLhgφmg1a2??COSF汽車在下坡路上停駐時的后橋附著力為: )( si-g1a2?汽車可能停駐的極限上坡路傾角 ,可根據(jù)后橋上的附著力與制動力相等的條1?件求得,即由 1a1g1a sinmsiLhgφm???)( COS得到 g11φh-arctn??式中, 是保證汽車上坡行駛的縱向穩(wěn)定性的極限坡路傾角。1?代入數(shù)據(jù) 5.08-1.24arctn1??得 ?37?同理可得下坡極限坡路傾角g11φhLarctn????代入數(shù)據(jù) 0.582.4rt1??得 ???7.91?5 盤式制動器制動器的設計5.1 制動盤直徑制動盤直徑 D 應盡可能取大些,這時制動盤的有效半徑得到增加,可以減小制動鉗的夾緊力,降低襯塊的單位壓力和工作溫度。受輪輞直徑的限制,制動盤的直徑通常選擇為輪輞直徑的 70%~79%,取 75%。由于輪胎規(guī)格為 225/50 R17 17 英寸即 431.8mm,所以制動盤直徑D=431.8×75%=323.85,為方便加工及保證尺寸的一致性,在此將尺寸取整,故取 320mm;驗算:320/431.8*100%=74.1%,滿足 70%~79%要求。制動盤直徑為 70%~79%輪輞直徑,根據(jù)輪輞提供給制動器的可利用空間,并本著制動盤直徑盡可能大的原則及運動時不發(fā)生干涉。初選制動盤的直徑d=140mm。5.2 制動盤厚度制動盤厚度 h 對制動盤質量和工作時的溫升有影響,為使質量小些,制動盤不宜取得很大,為了減少溫升,制動盤厚度又不宜取得過小,制動盤可以作成實心的,或者為了散熱通風需要在制動盤中間鑄出通風孔道,而我所選的車型制動器采用的便是通風盤式,而通風式制動盤厚度取為 20~ 50mm,采用較多的是 20~ 30mm,取 25mm。5.3 摩擦襯塊外半徑 內半徑2R1推薦摩擦襯塊外半徑 R2,與內半徑 R 的比值不大于 1.5。若此比值偏大,工作時襯塊的外緣與內側圓周速度相差較多,磨損不均勻,接觸面積減少,最終將導致制動力矩變化大。取 ,由于摩擦襯塊外徑 略小于制動盤半徑 = =1602.1?R2R2D30故取 160mm所以 m13.6021?5.4 制動襯塊工作面積 A由于制動襯塊為扇形,選定其到圓心的夾角為 60°所以 2221 cm409.163.1-360??????)π ()π ( ?R5.5 摩擦襯塊摩擦系數(shù) f選擇摩擦襯塊時,不僅希望其摩擦系數(shù)要高些,更要求其熱穩(wěn)定性要好,受溫度和壓力的影響要小。不能單純地追求摩擦材料的高摩擦系數(shù),各種制動器用摩擦材料的摩擦系數(shù)的穩(wěn)定值約為 0.3~0.5, 一般來說,摩擦系數(shù)愈高的材料,其耐磨性愈差,所以在制動器設計時并非一定要追求高摩擦系數(shù)的材料。在假設的理想條件下計算制動器的制動力矩,為使計算結果接近實際,取f=0.3。另外,在選擇摩擦材料時,應盡量采用減少污染和對人體無害的材料,故選用粉末冶金材料。5.6 制動襯塊的設計計算假定襯塊的摩擦面全部與制動盤接觸,且各處單位壓力分布均勻,則制動器的制動力矩為 RFM0f2??式中 f 為摩擦系數(shù); 為單側制動塊對制動盤的壓緊力;R 為作用半徑。對0于常見的具有扇形摩擦表面的襯塊,其徑向寬度不是很大,取 R 等于平均半徑或有效半徑 ,在實際中已經足夠精確。mRe平均半徑 為m m5.14620321m???R式中, , 為摩擦襯塊扇形表面的外半徑和內半徑。2R1有效半徑 是扇形的面積中心至制動盤中心的距離,eRm92.1465.])83.01([4]m1[34)(32 2221e ????????R)()(式中, 8.06m2R因為 m<1, ,故 ,且 m 越小,兩者差值越大。41<)( ?eR>應當指出,若,m 過小,即扇形的徑向的寬度過大,襯塊摩擦面上各不同半徑處的滑磨速度相差太遠,磨損將不均勻,因而單位壓力分布均勻這一假設條件不能成立, 則上述計算方法也就不適用。m 值一般不小于 0.65。制動盤工作面的加工精度應達到下述要求:平面度公差為 0.012mm,表面粗糙度 R,值為 0.7 ~1.3μm,兩摩擦表面的平行度公差不應大于 0.05mm,制動盤的端面圓跳動公差不應大于 O.03mm。通常制動盤采用摩擦性能良好的珠光體灰鑄鐵制造。為保證足夠的強度和耐磨性能,其牌號不應低于 HT250。5.7 襯片磨損特性的計算摩擦襯片(襯塊)的磨損受溫度、摩擦力、滑磨速度、制動鼓(制動盤)的材質及加工情況,以及襯片(襯塊)本身材質等許多因素的影響,因此在理論上計算磨損性能極為困難。但試驗表明,影響磨損的最重要的因素還是摩擦表面的溫度和摩擦力。從能量的觀點來說,汽車制動過程即是將汽車的機械能(動能和勢能)的一部分轉變?yōu)闊崃慷纳⒌倪^程。在制動強度很大的緊急制動過程中,制動器幾乎承擔了汽車全部動能耗散的任務。此時,由于制動時間很短,實際上熱量還來不及逸散到大氣中就被制動器所吸收,致使制動器溫度升高。這就是所謂制動器的能量負荷。能量負荷越大,則襯片(襯塊)的磨損越嚴重。對于盤式制動器的襯塊,其單位面積上的能量負荷比鼓式制動器襯片大許多倍,所以制動盤的表面溫度比制動鼓的高。各種汽車的總質量及其制動襯片(襯塊)的摩擦面積各不相同,因而有必要用一種相對的量作為評價能量負荷的指標。目前,各國常用的指標是比能量耗散率,即單位時間內襯片(襯塊)單位摩擦面積耗散的能量,通常所用的計量單位為 。比能量耗散率有時也稱為單位功負荷,或簡稱能量負荷。2m/W雙軸汽車的單個前輪及后輪制動器的比能量耗散率分別為 ??12a1t4meAV)( ??)1(t4me21a2????AV)(jt1?式中, --汽車總質量(t)am----汽車回轉質量換算系數(shù);?--制動器初速度和終速度(m/s) ;21V、j--制動減速度( ) ;2s/--前、后制動器襯片(襯塊)的摩擦面積( ) ;21A、 2mβ--制動力分配系數(shù)。在緊急制動到停車的情況下, ,并認為 ,故02?V1???1at4meA)(t2a??據(jù)有關文獻推薦,鼓式制動器的比能量耗散率以不大于 1.8 為宜,2m/W計算時取堿速度 j=0.6g。制動初速度 :乘用車用 100km/h(27. 8m/s);總質量1V3.5t 以下的商用車用 80km/h(22.2m/s);總質量 3.5t 以上的商用車用65km/h(18m/s)。乘用車的盤式制動器在同上的 和 j 的條件下,比能量耗散率1應不大于 6.0 。對于最高車速低于以上規(guī)定的制動初速度的汽車,按上2m/W述條件算出的 e 值允許略大于 1.8 。比能量耗散率過高不僅引起襯片2m/W(襯塊)的加速磨損,且有可能使制動鼓或制動盤更早發(fā)生龜裂。即乘用車的盤式制動器在 (27.8m/s)和 j=0.6g 條件下,h/k10?V由于設計驅動輪制動器僅計算后摩擦襯塊的摩擦特性代入數(shù)據(jù)得s73.4896.02t??221 m/37.16.0473.8.9eW???222 /-)(另一個磨損特性指標是襯片(襯塊)單位摩擦面積的制動器摩擦力,化摩擦力越大,則磨損越嚴重。單個車輪制動器的比摩擦力為RAM??f式中, 為單個制動器的制動力矩;R 為襯塊平均半徑 或有效半徑 ;?MmReA 為單個制動器的襯片(襯塊)摩擦面積。當前輪處于最大制動力矩時,代入數(shù)據(jù)為:23/0.541.69307f NRA????當后輪處于最大制動力矩時,代入數(shù)據(jù)為:23m/9.05.8fM?6 制動器主要零部件的結構設計6.1 制動盤制動盤結構形狀有平板形和禮帽形,由于所設計的是鉗盤式制動器,故采用后者即禮帽形制動盤,其圓柱部分長度取決于布置尺寸。為了改善冷卻,所設計的鉗盤式制動器的制動盤鑄成中間有徑向通風槽的雙層盤,可大大增加散熱面積,但盤的整體厚度較大。制動盤工作面的加工精度應達到下述要求:平面度小于等于 0. 01mm,表面粗糙度值小于等于 0.06mm,兩摩擦表面的不平行度小于等于 0.01mm,制動盤的端面圓跳動小于等于 0.03mm。6.4 摩擦材料制動摩擦材料應具有高而穩(wěn)定的摩擦系數(shù),抗熱衰退性能好,不能在溫度升到某一數(shù)值后摩擦系數(shù)突然急劇下降,材料的耐磨性好,吸水率低,有較高的耐擠壓和耐沖擊性能;制動時不產生噪聲和不良氣味,應盡量采用少污染和對人體無害的摩擦材料。經過綜合考慮,制動盤采用摩擦性能良好的珠光體灰鑄鐵鑄造,為保證足夠的強度和耐磨性能,其牌號為 HT250。摩擦襯塊選用減少污染和對人體無害的粉末冶金材料。7 制動驅動機構的設計與計算6.2 制動鉗制動鉗由球墨鑄鐵 QT400-18 制造,做成整體的,其外緣留有開口,以便不必拆下制動器便可檢查或更換制動塊。制動鉗體應有高的強度和剛度。在鉗體中加工出制動油缸。為了減少傳給制動液的熱量,將杯形活塞的開口端頂靠制動塊的背板。活塞由鋼制造,為了提高耐磨損性能,活塞的工作表面要進行鍍鉻處理。6.3 制動塊制動塊由背板和摩擦襯塊構成,兩者直接牢固地壓嵌或鉚接或連接在一起。襯塊多為扇形,也有矩形、正方形或長圓形的。活塞應能壓住盡量多的制動塊面積,以免襯塊發(fā)生卷角而引起尖叫聲。制動塊背板由鋼板制成。為了避免制動時產生的熱量傳給制動鉗而引起制動液氣化和減小制動噪聲,可在摩擦襯塊與背板之間或在背板后粘(或噴涂)一層隔熱減震墊(膠)。由于單位壓力大和工作溫度高等特點,摩擦襯塊的磨損較快,因此其厚度較大。一般情況下,輕型汽車的摩擦塊厚度在 7.5 mm~16 mm 之間,中、重型汽車的摩擦襯塊的厚度在 14 mm~22 mm 之間。許多盤式制動器裝有摩擦襯塊達到磨損極限時的報警裝置,以便能及時更換摩擦襯塊。7.1 制動驅動機構的形式制動驅動機構將來自駕駛員或其它力源的力傳給制動器,使之產生制動力矩。根據(jù)制動力源的不同,制動驅動機構一般可分為簡單制動、動力制動和伺服制動三大類。根據(jù)制動器各方面綜合考慮采用液壓市制動驅動機構液壓式驅動機構:優(yōu)點:a.制動時可以得到必要安全性,因為液壓系統(tǒng)內系統(tǒng)內壓力相等,左右輪制動同時進行;b.易保證制動力正確分配到前、后輪,因為前、后輪分泵可以做出不同直徑;c.車振或懸架變形不發(fā)生自行制動;,d.不須潤滑和時常調整;缺點:a 當管路一處泄漏,則系統(tǒng)失效;b 低溫油液變濃,高溫則汽化;c 不可長時間制動。但綜合來看,油壓制動還是可取的,且得到了廣泛的應用。7.2 分路系統(tǒng)為了提高制動工作可靠性,應采用分路系統(tǒng),即全車的所有行車制動器的液壓或氣壓管路分為兩個或更多的互相獨立的回路,其中一個回路失效后,仍可利用其它完好的回路起制動作用。雙軸汽車的雙回路制動系統(tǒng)有以下常見的五種分路形式:圖 4 分路系統(tǒng)1)一軸對一軸(Ⅱ)型,如圖 a 所示,前軸制動器與后橋制動器各用一個回路(“Ⅱ型”是其形象的簡稱,下同)。2)交叉(X)型,如圖 b 所示,前軸的一側車輪制動器與后橋的對側車輪制動器同屬一個回路。3)一軸半對半軸(HI)型,如圖 c 所示,兩側前制動器的半數(shù)輪缸和全部后制動器輪缸屬于一個回路,其余的前輪缸則屬于另一回路。4)半軸一輪對半軸一輪(LL)型,如圖 d 所示,兩個回路分別對兩側前輪制動器的半數(shù)輪缸和一個后輪制動器起作用。5)雙半軸對雙半軸(HH)型,如圖 e 所示。每個回路均只對每個前、后制動器的半數(shù)輪缸起作用。Ⅱ型的管路布置較為簡單,可與傳統(tǒng)的單輪缸(或單制動氣室)鼓式制動.器配合使用,成本較低,目前在各類汽車特別是貨車上用得最廣泛。這種形式若后制動回路失效,則一旦前輪抱死即極易喪失轉彎制動能力。對于采用前輪驅動因而前制動器強于后制動器的轎車,當前制動回路失效而單用后橋制動時,制動力將嚴重不足(小于正常情況下的一半),并且若后橋負荷小于前軸,則踏板力過大時易使后橋車輪抱死而汽車側滑。X 型的結構也很簡單。直行制動時任一- 回路失效,剩余總制動力都能保持正常值的 50%。但是,一旦某一管路損壞造成制動力不對稱,此時前輪將朝制動力大的一邊繞主銷轉動,使汽車喪失穩(wěn)定性。因此,這種方案適用于主銷偏移距為負值(達 20mm)的汽車上。這時,不平衡的制動力使車輪反向轉動,改善了汽車穩(wěn)定性。HI、HH、LL 型結構都比較復雜。LL 型和 HH 型在任一回路失效時,前、后制動力比值均與正常情況下相同。LL 型和 HH 型的剩余總制動力可達正常值的50%左右。HI 型單用一軸半回路時剩余制動力較大,但此時與 LL 型一樣,緊急制動情況下后輪很容易先抱死。所以本次設計選擇 X 型的布置方案。8 液壓制動驅動機構的設計計算8.1 制動輪缸直徑 d 的確定制動輪缸對制動蹄(塊)施加的張開力 與輪缸直徑 d 和制動管路壓力 p 的0F關系為 )/(4d0pπ?制動管路壓力一般不超過 10—12MPa,對盤式制動器可更高。壓力越高,對管路(首先是制動軟管及管接頭)的密封性要求越嚴格,但驅動機構越緊湊。輪缸直徑 d 應在標準規(guī)定的尺寸系列中選(HG2865-1997),具體為19mm、22mm、24mm、25mm、28mm、30mm、32mm、35mm、38mm、40mm、45mm、50mm、55mm。我們這里油壓選取 12MPa,代入數(shù)據(jù)得到后輪輪缸直徑 45mm,前輪輪缸直徑為 35mm。8.2 制動主缸直徑 的確定0d第 i 個輪缸的工作容積為??n1i2id4?πV式中, 為第 i 個輪缸活塞的直徑;n 為輪缸中活塞的數(shù)目; 為第 i 個輪缸id i?活塞在完全制動時的行程,初步設計時,制動器可取 =2.0—2.5mm,這里取i=2mmi?前輪制動器單個輪缸工作容積 321wm194354??πV后輪制動器單個輪缸工作容積 278π輪缸的總容積:=2(3178+1924)10204 ??MV1w2在初步設計時,制動主缸的工作容積可取為:對于乘用車 V1.0?主缸活塞行程 和活塞直接 為0S0d4SVπ?一般 =(0.8—1.2) 。00我們這里取 dS主缸的直徑 應符合 QC/T311—1999 中規(guī)定的尺寸系列,具體為019mm、22mm、26mm、28mm、32mm、35mm、38mm、40mm、45mm。代入數(shù)據(jù)得到主缸直徑得300 m4.12.d4???SVπ m27.4d0?S查表后取 26mm,即 =26mm0d8.3 制動踏板力制動踏板力 為PFk1ipd420)(π ??式中, 為踏板機構的傳動比( =4-7) ; 為踏板機構及液壓主缸的機械pi p效率,可取 =0.82—0.86,這里我們取 0.85;K 為真空助力器增力背數(shù),這里?我們取 5。代入數(shù)據(jù):NFP 82.951.01264k1ipd420 ?????π)(π制動踏板力應滿足以下要求:最大踏板力一般為 500N(轎車)或 700N(貨車)。設計時,制動踏板力可在 200~350N 的范圍內選取。8.4 制動踏板工作行程)( 0210pi???S式中, 為主缸中推桿與活塞間的間隙,一般 =1.5—2.0mm,這里取01? 01?; 為主缸活塞的空行程,即主缸活塞從不工作的極限位置到使m8.01?2其皮碗完全封堵主缸上的旁通孔所經過的行程。代入數(shù)據(jù)m14928.65i0210p ?????)()( ?S制動器調整正常時的踏板工作行程 Sp,只應占計及制動襯片(襯塊)的容許磨損量在內的踏板行程的 40%-60%。為了避免空氣侵入制動管路,在計算制動主缸活塞回位彈簧(同時也是回油閥彈簧)時,應保證踏板放開后,制動管路中仍保持 0.05--0. 14MPa 的殘余壓力。踏板行程(計人襯片或襯塊的允許磨損量)對轎車最大應不大于100~150mm,對貨車不大于 180mm。此外,作用在制動手柄上的力對轎車最大不大于 400N,對貨車不大于 600N;制動手柄行程對轎車最大不大于 160mm,對貨車不大于 220mm。