【溫馨提示】壓縮包內(nèi)含CAD圖有下方大圖片預(yù)覽,下拉即可直觀呈現(xiàn)眼前查看、盡收眼底縱觀。打包內(nèi)容里dwg后綴的文件為CAD圖,可編輯,無水印,高清圖,壓縮包內(nèi)文檔可直接點(diǎn)開預(yù)覽,需要原稿請自助充值下載,所見才能所得,請見壓縮包內(nèi)的文件及下方預(yù)覽,請細(xì)心查看有疑問可以咨詢QQ:11970985或197216396

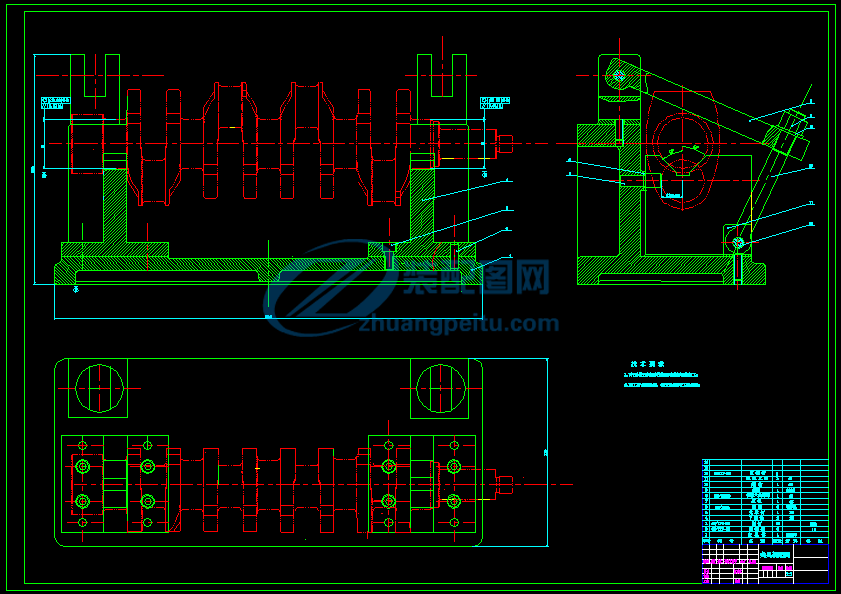
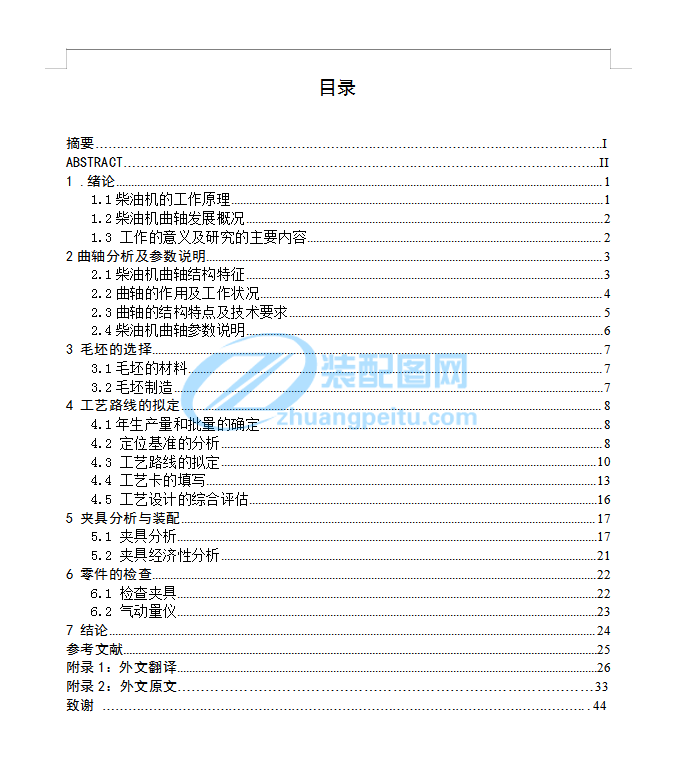
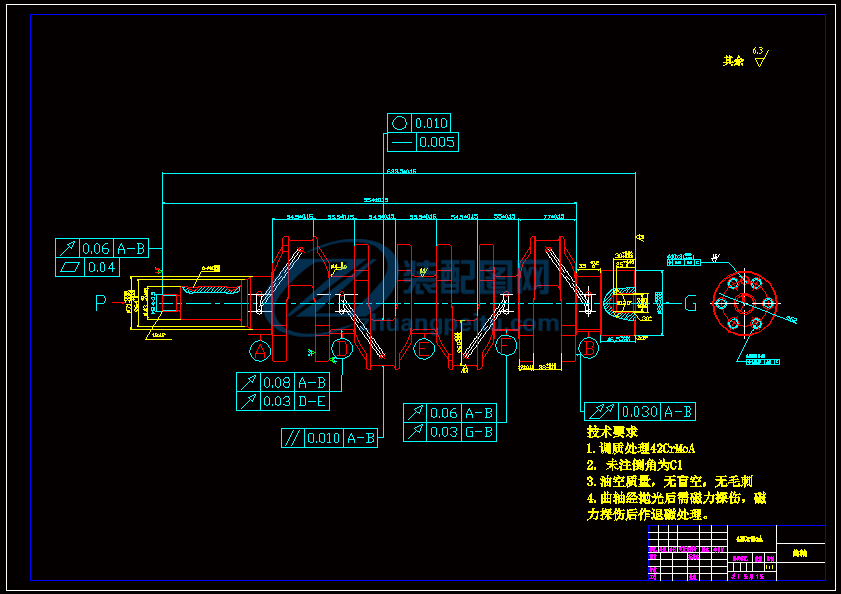

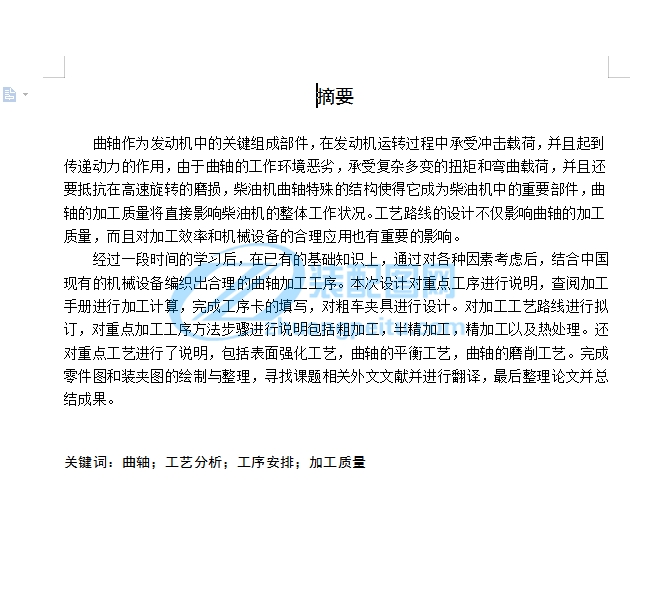
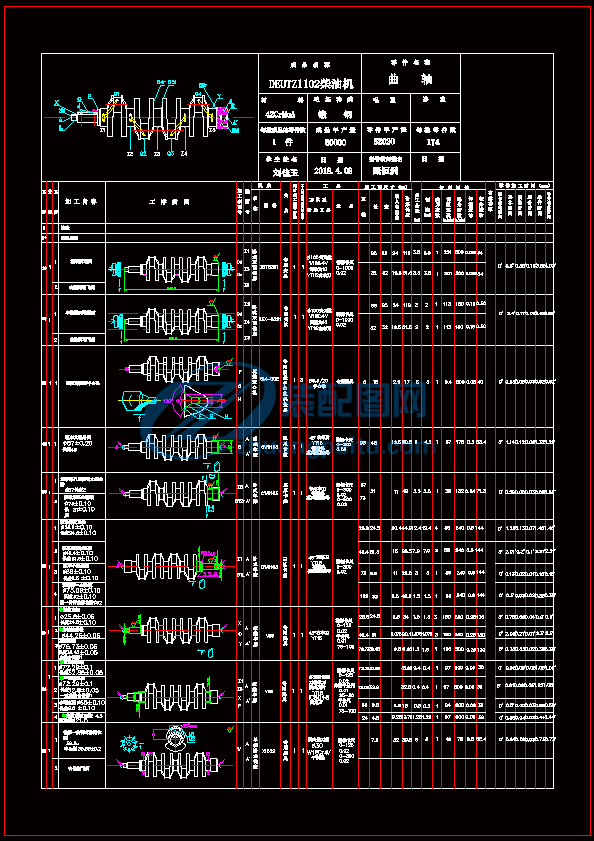
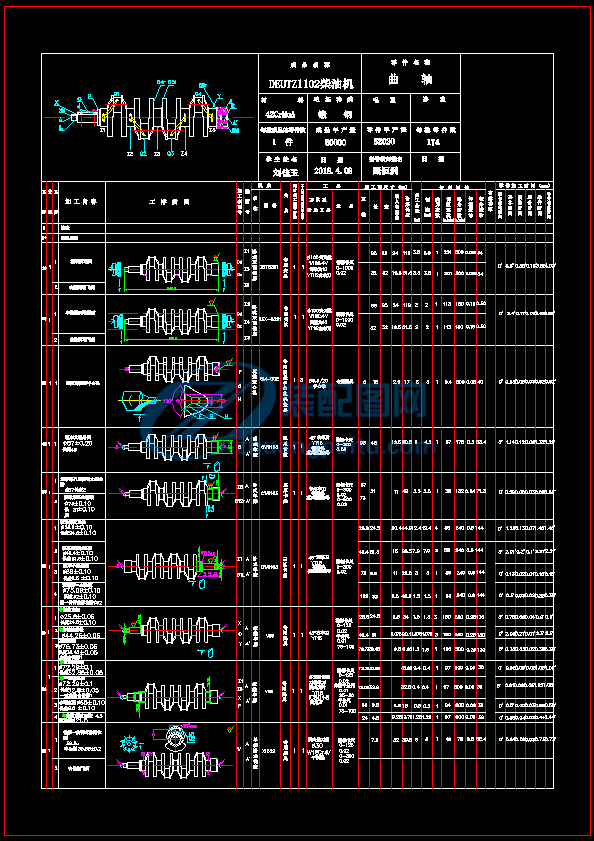


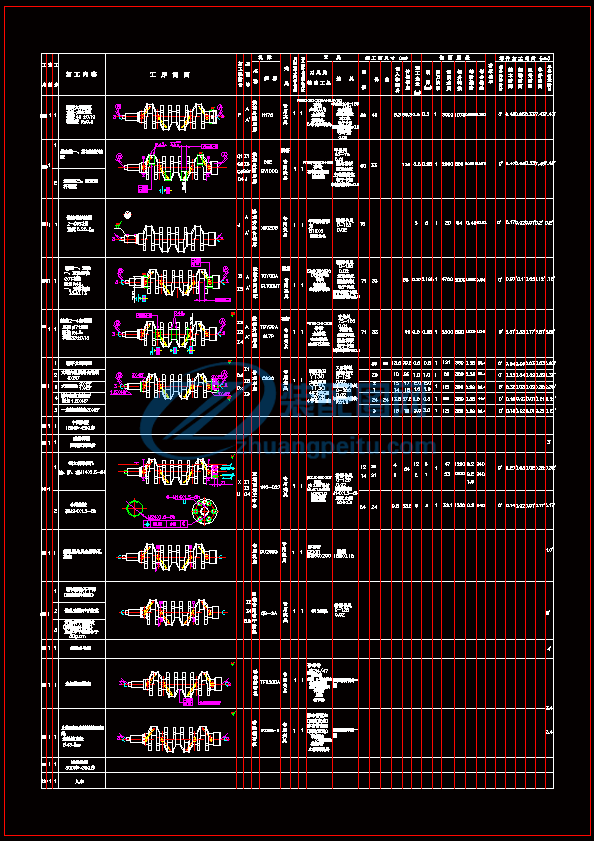

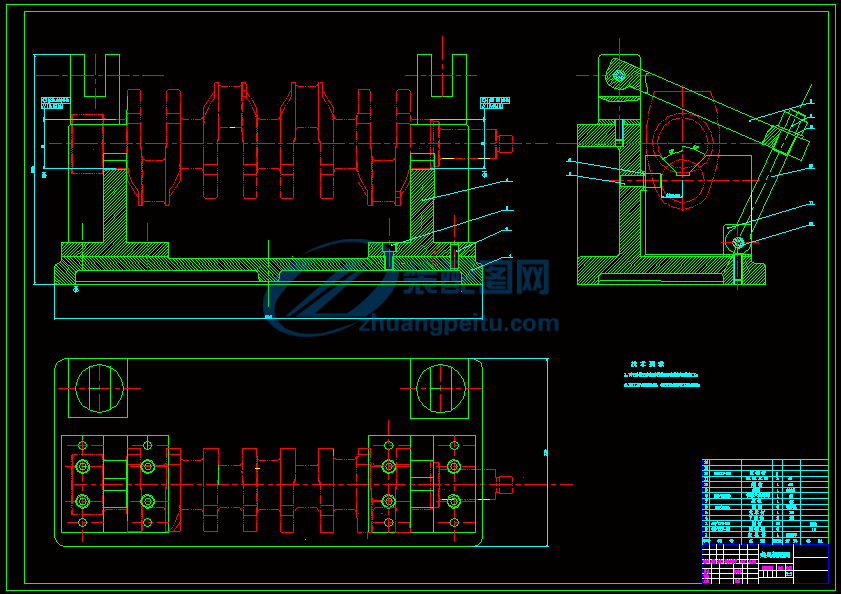
大型汽車柴油機(jī)曲軸工藝規(guī)程設(shè)計(jì)
附錄A: 外文翻譯
用數(shù)值與實(shí)驗(yàn)調(diào)查氮鋼曲軸大功率集成電路發(fā)動機(jī)疲勞特性
氮化通常適用于提高機(jī)械零部件的表面性能,也可提高耐疲勞性。本文的目的是探討,通過數(shù)值模型的方法和實(shí)驗(yàn)測試,誘發(fā)氮化對船用柴油機(jī)曲軸的疲勞性能殘余應(yīng)力的影響。殘余應(yīng)力梯度引起的熱化學(xué)處理考慮到了有限元模型的方法。進(jìn)行了具有軸向試驗(yàn)機(jī),以驗(yàn)證該數(shù)值模型,并評估所述曲軸的機(jī)械參數(shù),諸如屈服強(qiáng)度和疲勞極限。通過施加應(yīng)變測量手段下彎曲,以評估曲軸殘余應(yīng)力的實(shí)驗(yàn)創(chuàng)新的方法也被開發(fā)。這種方法被證明是有用的,以確定誘導(dǎo)熱處理成曲軸的殘余應(yīng)力的大小,并且它可能在一些情況下被應(yīng)用于殘余應(yīng)力場的評價。[DOI: 10.1115/1.4001834]
關(guān)鍵詞:氮化,有限元模型,曲軸,殘余應(yīng)力,耐疲勞性
1引言
曲軸是內(nèi)燃機(jī)中最關(guān)鍵的組分之一。在其使用壽命時期,它受到來自燃燒過程中和相對運(yùn)動的部件的慣性產(chǎn)生的循環(huán)彎曲壓力和扭轉(zhuǎn)載荷[1,2]。曲軸的機(jī)械故障疲勞現(xiàn)象是由于曲柄銷和配重之間的圓角半徑引起的。在這運(yùn)轉(zhuǎn)過程中達(dá)到多軸應(yīng)力狀態(tài)下的最高級別,是因?yàn)楦叩膽?yīng)力集中系數(shù)[3,5]。
為了防止疲勞破壞,施加到曲軸的圓角的主要機(jī)械處理是感應(yīng)淬火和滾壓,而熱化學(xué)是表面硬化和滲氮[6-9]。機(jī)械部件的表面處理方法通常應(yīng)用于用于增加硬度和耐磨損性,而無需修改散裝材料的機(jī)械特性,但最近的研究表明,它們也增加,因?yàn)檎T導(dǎo)的表面和次表面層的壓縮殘余應(yīng)力的疲勞極限[10-13]。
一些研究表明,提高耐疲勞性氮化是最有效的方法[14,15] 。與其他熱化學(xué)處理相比,氮不涉及任何物質(zhì)微觀結(jié)構(gòu)的修改(溫度在此過程中達(dá)到一般不超過520℃[16] )。這保證了最小的失真和機(jī)械部件的良好的尺寸控制?,F(xiàn)今可用的不同的氮化過程是:它們包括氣體,液體,和等離子滲氮,即第一個是最常用的。 此過程中,氮被引入到鐵類合金的表面上是通過保持金屬與含氮?dú)怏w如氨接觸。擴(kuò)散層的厚度為約200?600 um,在表面上,脆性nitrogenrich層厚度(5-50um),這就是所謂的白色氮化物層的產(chǎn)生,它在該氮化工序后取出。間質(zhì)性氮?dú)夂偷锍恋碓跀U(kuò)散層的分布產(chǎn)生的增加,元件的尺寸和殘余應(yīng)力相關(guān)聯(lián)的領(lǐng)域。殘余應(yīng)力必須是自平衡的,它們是一般地在負(fù)的表面和正面于主體材料中。
耐疲勞性的改善主要?dú)w因于兩個殘余應(yīng)力場和表面硬化。壓縮應(yīng)力,實(shí)際上是有益的,用于防止疲勞裂紋萌生在表面和延緩裂紋擴(kuò)展[17-19]。表面硬度,此外,連接到極限強(qiáng)度和由經(jīng)驗(yàn)公式的疲勞極限[19]。在這項(xiàng)工作中,研究了氮化殘余應(yīng)力對一個2000千瓦的船用柴油發(fā)動機(jī)的曲軸的疲勞性能的影響。在滿刻度元件上的數(shù)值模型和合適的實(shí)驗(yàn)進(jìn)行測試,以檢測殘余應(yīng)力與應(yīng)變的測量,并確定疲勞阻力。還開發(fā)了試樣的數(shù)值模型,具有曲軸圓角區(qū),承受彎曲載荷的相同的幾何形狀。試樣的簡單的幾何形狀初步評估應(yīng)力集中作用由于變化的部分和滲氮過程對由于彎曲載荷的應(yīng)力 - 應(yīng)變狀態(tài)的影響[20]。測量技術(shù)中的殘余應(yīng)力的評價可以被劃分成破壞性和非破壞性。與前者的技術(shù),殘余應(yīng)力誘導(dǎo)通過去除材料的位移測量。最常用的方法是塊切片,分條,層去除,鉆孔,和輪廓的方法[21-26] 。非破壞性技術(shù)通常圍繞衍射,其可以被用于測量特定的原子晶格面的彈性應(yīng)變,如X-射線衍射,XRD,和中子衍射[21,27-30]。據(jù)作者所知,在文中非破壞性的實(shí)驗(yàn)方法來估計(jì)表面殘余應(yīng)力場和集中應(yīng)力值是不可行的??紤]到這一點(diǎn),一個創(chuàng)新的實(shí)驗(yàn)步驟進(jìn)行表面殘余應(yīng)力的間接評價,以不同的彎曲載荷下表面應(yīng)變測量的手段被開發(fā)了。為了認(rèn)真評估應(yīng)力 - 應(yīng)變狀態(tài)在重要領(lǐng)域中, 殘余應(yīng)力和實(shí)驗(yàn)數(shù)值計(jì)算結(jié)果值比較的影響,幾個有限元素(FE)模型與ABAQU ?被操作[31]。
2幾何形狀和材料
對一個船用四沖程循柴油發(fā)動機(jī)的燃油直噴技術(shù)和廢氣渦輪增壓器的曲軸進(jìn)行了研究。發(fā)動機(jī)有16個汽缸和90度V行結(jié)構(gòu),約2000千瓦的功率,最大轉(zhuǎn)速等于2000轉(zhuǎn)。為了評價滲氮對表面應(yīng)力狀態(tài)的影響,對一個具有帶圓角半徑的曲軸也進(jìn)行了分析。
曲軸的幾何形狀和部分圖像以及式樣在圖表1_a_–1_c_中。根據(jù)歐洲標(biāo)準(zhǔn) EN10083-1曲軸和試樣的材料是淬火和氮化的35CrMo4,以前評價材料的化學(xué)組成和主要機(jī)械特征[30,31],分別列于表1和2分別。
3數(shù)值模型
式樣應(yīng)用了直線彈性和理想彈塑性數(shù)值模型,以便應(yīng)力集中系數(shù)來評估由于橫截面減小而引起的應(yīng)力 - 應(yīng)變狀態(tài)下的氮化過程中的殘余應(yīng)力場的影響。由于幾何形狀的對稱性和彎曲載荷的施加,只有四分之一的標(biāo)本被建模,并適當(dāng)?shù)倪吔鐥l件對稱平面進(jìn)行了施加。1410為N m彎曲載荷,對應(yīng)2820N m,從總體上看是由兩個集中力的應(yīng)用,具有相同的數(shù)量級23,500 N'和相反方向上,位于離對稱軸30毫米。對稱邊界條件假設(shè),并采用點(diǎn)荷載證明不影響應(yīng)力場的最小截面為線性分析。另一方面,模型具有可塑性的存在,為了避免收斂問題所用分布載荷。具有約機(jī)型50,000自由度采用八節(jié)點(diǎn)實(shí)體被開,線性元素來生成網(wǎng)格,如圖所示2。為了提高分析的準(zhǔn)確度,合適的網(wǎng)格細(xì)化也被認(rèn)為是在圓角區(qū),陡峭的應(yīng)力梯度顯示在圖 2(a)中。收斂性分析是所進(jìn)行的模型裝置具有越來越細(xì)網(wǎng)眼直到差異,在最大von Mises節(jié)點(diǎn)而言應(yīng)力是最小的橫截面,兩個連續(xù)間模型是小于3%。一個完整的幾何線性彈性模型也進(jìn)行處理,并將結(jié)果在最小橫獲得部分是相同的對稱模型。
對殘余應(yīng)力場進(jìn)行了引入,在節(jié)點(diǎn)條件下通過預(yù)應(yīng)力手段,通過氮化處理把所述實(shí)體分割模擬,重現(xiàn)誘導(dǎo)外表面下面的改性層。殘余應(yīng)力趨勢的分析功能是通過考慮一個軸對稱自我平衡和極坐標(biāo)系(P-R-q)顯示于圖表2b,其中p和r為分別是軸向和徑向的方向的極角,在圖表Eq(1)中,殘余應(yīng)力大小只依賴于徑向坐標(biāo)。
為了得到一個自平衡場即所得試樣縱截面的拉伸應(yīng)力必須等于壓縮的1到2個不同區(qū)域的所得進(jìn)行了鑒定。
根據(jù)以前的工作,其中,所述不同的氮化試樣的殘余應(yīng)力深度輪廓是由X射線衍射方法測定,采用SIN2方法結(jié)合使用的子層去除并用鉆孔法[32,33],在緊接層外表面下方的3毫米深壓縮殘余應(yīng)力場被假設(shè),而所述芯材從3mm的外部表面的下方朝向試樣的軸線拉伸殘余應(yīng)力進(jìn)行了審議。分別對應(yīng)殘余應(yīng)力的最大值和最小值分別等于375Mpa和95Mpa[33]。
根據(jù)實(shí)驗(yàn)結(jié)果[32],一個近似 ,拋物線形趨勢被選定為分析殘余應(yīng)力的功能,所報(bào)告的方程2和3',其中α1 =α1≤γ≤2和θ2 =θ2≤γ≤2是分析殘余應(yīng)力,分別作用在拉伸和壓縮層。應(yīng)力趨勢近似可以認(rèn)為充足考慮到對殘余應(yīng)力趨勢的認(rèn)識并不像表面應(yīng)力和殘余應(yīng)力的表面坡度重要。
報(bào)中所示的擬合常數(shù)在圖表2 d中,計(jì)算考慮到適當(dāng)?shù)倪吔鐥l件殘余應(yīng)力的功能必須滿足在試樣外表面r= 23mm,在對稱軸使r = 0mm,而且在拉伸的接口和壓縮層r= 20 mm。
在拉伸層,下面的邊界條件被應(yīng)用:
對于壓縮層,下面的邊界條件必須滿足:
確保拉伸和壓縮應(yīng)力合成在縱向試樣部分之間的平衡,兩殘余應(yīng)力的區(qū)域的等效性,必須施加
兩種不同的分析是在受到彎曲載荷的試樣進(jìn)行:最初,一個純粹的彈性材料性能被用來以檢查模型的精度,比較力集中系數(shù)值得到相應(yīng)文獻(xiàn)[34]。在這些初步的模型中,殘余應(yīng)力場沒有被引入到數(shù)字模型。
假設(shè)在下面的分析的理想彈塑性材料與屈服強(qiáng)度等于700Mpa,殘余應(yīng)力場也被考慮,目的評估在圓角區(qū)域的實(shí)際應(yīng)力 - 應(yīng)變狀態(tài)和影響力的氮化處理。
應(yīng)用曲軸的數(shù)值模型和兩個對稱面是為了用來減少自由度(運(yùn)算時間)。
曲柄銷油潤滑孔,對應(yīng)力分布有一個小的影響,未建模,并夾緊裝置,它在實(shí)驗(yàn)測試時試驗(yàn)機(jī)施加拉伸載荷是有用的用,是在該模型具有簡化的幾何引入。
適當(dāng)?shù)倪吔鐥l件施加于對稱平面和集中力等于45000 N,應(yīng)用在夾緊裝置200毫米的主軸頸軸,如圖 3。
開發(fā)了具有20個節(jié)點(diǎn)的實(shí)心磚約48,000自由度二次元模型。二次元被用來降低計(jì)算成本的分析。然而,在最關(guān)鍵的地方,如曲柄銷和主軸頸的連接,約七倍元素 比其它區(qū)域更小的被用來獲得一個詳細(xì)的應(yīng)力映射,如圖所示。在萬能試驗(yàn)機(jī)實(shí)驗(yàn)室考慮到負(fù)荷配置是相同的適用于曲軸。既是一個純粹的彈性和理想彈塑性材料性能被假定為不同的分析。
4實(shí)驗(yàn)測試
實(shí)驗(yàn)測試是由一個軸向試驗(yàn)機(jī)裝置上的氮化曲軸部執(zhí)行,一個具體的把持裝置的目的為了防止在加載周期外來曲載荷向曲軸傳遞。耐疲勞性和應(yīng)力狀態(tài)中所指出的有限元模型諸如曲柄銷和主軸頸圓角最關(guān)鍵的曲軸的區(qū)域,是由應(yīng)變儀測量的方法進(jìn)行評價。在下面的段落中描述的簡化創(chuàng)新的實(shí)驗(yàn)方法殘余應(yīng)力大小在曲軸表面也被估計(jì)。
4.1創(chuàng)新的殘余應(yīng)力評估程序。殘余應(yīng)力可存在于工程部件制造及熱過程的結(jié)果,或它們可以被引入以實(shí)現(xiàn)有益的機(jī)械性能如耐疲勞性。在簡支梁幾個部分評估殘余應(yīng)力的方法是可行的[35]。加載梁,采用了左右對稱的彎曲,進(jìn)入全塑系列使中間段轉(zhuǎn)換為一個塑料鉸鏈,該行為卸載期間的光柱直接彈性,殘余應(yīng)力得到是通過向全塑性力矩應(yīng)力分布所引起的反向彈性應(yīng)力分布。
所有這些方法都有其局限性,即破壞性的,時間耗時,昂貴,深度和準(zhǔn)確性有限,不可移植,或 僅限于簡單的幾何形狀的樣品。
由于這些原因,另一種創(chuàng)新的方法簡單,基于表面張力有和沒有殘余應(yīng)力場的存在之間差值被開發(fā)了。
通過考慮,例如,具有矩形氮化棒部分承受彎曲負(fù)荷,剩余的與該區(qū)段中的彎曲應(yīng)力互重疊,以最大壓縮應(yīng)力的增加量和在拉伸的減少。通過固定在棒部的相對側(cè)上的兩個應(yīng)變儀裝置,它可以測量的壓縮和拉伸應(yīng)變的最大值,并且,通過增加彎曲載荷,這兩個上壓側(cè)識的彈性極限,在這里屈服應(yīng)力將首先到達(dá),然后在拉伸。通過參照二維主應(yīng)力和使用由拉伸試驗(yàn)中給出的彈性極限。
圖4a顯示了馮?米塞斯橢圓面,其中線段AB表示壓縮之間的區(qū)別 和拉伸彈性限。
彎曲載荷引僅引起應(yīng)力,因此線段AB轉(zhuǎn)換平行于軸直到點(diǎn)A和B相切馮?米塞斯橢圓。通過報(bào)告的彈性極限和它可以識別的C點(diǎn),其坐標(biāo)所代表的殘余應(yīng)力在兩個方向上的大小。
4.2負(fù)載應(yīng)用設(shè)備。曲軸承受燃燒循環(huán)中復(fù)雜載荷的條件很難在實(shí)驗(yàn)室測試中精確地復(fù)制。因?yàn)閺澢?fù)載是主要的負(fù)載和彎曲應(yīng)力是最關(guān)鍵耐疲勞性,偏心拉伸負(fù)荷施加到曲軸是通過借助于液壓軸向試驗(yàn)機(jī),如圖 5a。負(fù)載器件包括兩個部分高梁具有高剛性連接到所述曲軸的兩個螺絲由180bar氣動千斤頂裝置收緊。夾持裝置,由兩個連接交叉構(gòu)件構(gòu)成,兩個螺絲鎖組成扭矩等于280 NM被固定在梁的頂部。
由試驗(yàn)機(jī)給定的拉伸載荷通過球形裝置傳送到固定在梁上的曲軸,這允許負(fù)荷施加在單個點(diǎn),并避免任何傳輸額外的彎曲載荷,由于在結(jié)構(gòu)中的過約束而引起的整個系統(tǒng)的裝配對準(zhǔn)誤差。在圖5b中示出了夾緊裝置的裝配圖。
4.3曲軸準(zhǔn)備。數(shù)值分析結(jié)果表明,曲柄銷軸頸和配重之間的圓角都圖中最關(guān)鍵應(yīng)力 - 應(yīng)變狀態(tài)。在這些領(lǐng)域幾個應(yīng)變儀被應(yīng)用到仔細(xì)測量的軸向和周向應(yīng)變。圖6示出了應(yīng)變片的安排:三個90度圓環(huán)每個圓角沿著對稱平面并沿兩個15度的固定平面旋轉(zhuǎn),如圖6.
在對稱平面四進(jìn)一步線性應(yīng)變片固定,以評估的彎曲應(yīng)力大小。另外在飛機(jī)上加入圓角中心,這是確定的有限元模型是最關(guān)鍵的壓力,通過放置一個90度圓環(huán)和線性應(yīng)變計(jì)的主軸頸圓角評價。這些應(yīng)變片允許殘余應(yīng)力評估。
為了評價作用于負(fù)載裝置上的彎曲應(yīng)力能夠使機(jī)器的液壓方式缸的偏轉(zhuǎn),所述夾持裝置的應(yīng)變的測定。
HBM?120線性應(yīng)變儀與0.6毫米網(wǎng)格長度和應(yīng)變系數(shù)等于1.82+1.5%,和MM?12090度圓環(huán)0.6 mm間隔長度和應(yīng)變系數(shù)等于2.101.5%被使用。在圖表6中鍵合在曲柄銷軸頸和配重之間的圓角應(yīng)變片被顯示。
該測量進(jìn)行了考慮,對于每一個應(yīng)變儀具有測量應(yīng)變儀一半的惠斯通電橋配置和補(bǔ)償。HBM UPM 100采集系統(tǒng)被用于動態(tài)應(yīng)變措施,以及數(shù)據(jù)存儲與采樣,時間假定為等于5毫秒。在疲勞試驗(yàn)中的載荷被施加有頻率0.8赫茲。
5結(jié)果分析
5.1數(shù)值結(jié)果。在試樣上的線狀彈性分析表明,正如所料,最關(guān)鍵的區(qū)域中,具有馮米塞的最高值應(yīng)力,于圓角底座具有最大應(yīng)力在縱向上等于905 兆帕,應(yīng)用彎曲載荷等于1410Nm。
從彼得森的獲得圖參考應(yīng)力集中系數(shù)的值[34],為1.53,而從有限元模型的值
等于1.534。應(yīng)力集中系數(shù)的計(jì)算方法考慮了最大比例 縱向節(jié)點(diǎn)應(yīng)力,用有限元模型進(jìn)行評估,并標(biāo)稱彎曲應(yīng)力中的最小橫截面。
和之間的最小差異,指出該有限元模型的網(wǎng)格具有適當(dāng)?shù)募?xì)化并且計(jì)算結(jié)果可靠的。圖7(a)和7(b) 顯示應(yīng)力的趨勢,并且沒有殘余應(yīng)力場應(yīng)中,在后一個圓角底座部
彎曲載荷分別等于987N m和1410N m。
殘余應(yīng)力,如假定,降低拉伸應(yīng)力的最大值并增加最小壓縮。殘余應(yīng)力場的影響是比較明顯如圖7(a),其中該材料仍具有彈性性能,同時,通過施加最大彎曲載荷,屈服強(qiáng)度達(dá)到中壓側(cè)和最小應(yīng)力值具有和不具有殘余應(yīng)力大致相同。
在曲軸上關(guān)于數(shù)值分析的結(jié)果,最大von Mises應(yīng)力是位于曲柄銷軸頸和配重之間的接,
其中的應(yīng)力集中系數(shù)為最大,在主軸頸和配重之間的連接,由于軸向載荷的下偏心,最大von Mises應(yīng)力等于625Mpa。
在45℃下平面連接兩個圓角的中心,如圖所示8(b),證明有應(yīng)力的最高值,如圖所示8(c);
因此,它代表從圖中的耐疲勞性和疲勞裂紋形核的概率的點(diǎn)中最關(guān)鍵的部分。
圖9(a)指出了馮?米塞斯的價值觀上強(qiáng)調(diào)曲柄銷和主軸頸圓角相對于一個二維 極坐標(biāo)r,其起原點(diǎn)在圓角中心圖。
談到von Mises應(yīng)力最大值 應(yīng)力集中系數(shù),由于彎矩和 軸向力可以計(jì)算,對于所施加負(fù)荷相等 90KN,通過考慮下列給出的額定壓力公式:
計(jì)算出連桿軸頸和主軸頸應(yīng)力集中系數(shù)分別約為6.5和5 。對曲軸氮化殘余應(yīng)力的影響進(jìn)行了評價,具有通過重疊的簡化方法中,對最大壓力平面,殘余應(yīng)力場,通過實(shí)驗(yàn)測量裝置評估彎曲應(yīng)力的趨勢。在圖表9 (c)中顯示了應(yīng)力引起的彎曲載荷,所施加的殘余應(yīng)力趨勢,并且疊加應(yīng)力趨勢。
滲氮過程的有益效果得到證實(shí);由于高的壓縮殘余應(yīng)力的存在,事實(shí)上,在曲軸表面進(jìn)行在負(fù)載周期,平均壓縮應(yīng)力,這有助于提高疲勞壽命。
5.2實(shí)驗(yàn)結(jié)果。初步交替疲勞試驗(yàn)(r =-1)施加的負(fù)載等于60千牛頓中進(jìn)行。在圖10(a)載荷 - 應(yīng)變曲線的例子所示:可以忽略不計(jì)的滯后區(qū)域以及沒有對應(yīng)變曲線異常趨勢指出,沒有相當(dāng)大的增塑出現(xiàn)和沒有表面疲勞裂紋啟動。通過參照von Mises應(yīng)力在倒角的中間,對實(shí)驗(yàn)應(yīng)力集中系數(shù)進(jìn)行了計(jì)算。
在表3中的是曲柄銷軸頸和配重之間的圓角區(qū)域測得的應(yīng)變值報(bào)告,而表4總結(jié)了von Mises應(yīng)力在曲柄銷和主軸頸圓角,并用公式計(jì)算標(biāo)稱應(yīng)力。
實(shí)驗(yàn)應(yīng)力集中系數(shù),對于曲柄銷和主軸頸分別為7.13和5.47。在數(shù)值模擬和實(shí)驗(yàn)應(yīng)力中之間的區(qū)別因素的影響,在6%至9%的范圍內(nèi),可以通過考慮了實(shí)驗(yàn)測試的不確定性和簡化的數(shù)學(xué)模型引入認(rèn)為是可接受的。
為了確定材料的彈性極限,進(jìn)行了加載 - 卸載準(zhǔn)靜態(tài)測試。當(dāng)觀察到一些應(yīng)變計(jì)的塑性轉(zhuǎn)變時,彎曲載荷增加是通過機(jī)器施加高達(dá)90KN的負(fù)載。測得的應(yīng)變值指出殘余氮化壓縮應(yīng)力,它有降低表面張應(yīng)力和增加所需的最大負(fù)荷,實(shí)現(xiàn)了材料的屈服強(qiáng)度的效果的影響。
通過舉例的方式,在應(yīng)變片上施加9到90KN的載荷 - 應(yīng)變曲線的磁滯的載荷示于圖103(b),其中,所述壓縮和拉伸材料的行為之間的差別是明顯的。
參照秒4.1,并使用剛剛描述的加載 - 卸載試驗(yàn)的結(jié)果,對氮化殘余應(yīng)力的大小進(jìn)行評。在壓縮和拉伸屈服強(qiáng)度分別提取由縱向應(yīng)變片4和9分別給出的措施。壓縮屈服強(qiáng)度是通過施加60KN頓的載荷來實(shí)現(xiàn),而沒有相當(dāng)大的塑性移檢測到最大拉伸負(fù)荷施加等于90千牛頓。為60KN頓和90KN施加的載荷測得的縱向和周向應(yīng)變值分別列于表5。通過應(yīng)用方程(10) - (14)以及考慮應(yīng)變測量的結(jié)果,對縱向和周向應(yīng)力極限進(jìn)行計(jì)算,值列于表6。通過馮?米塞斯橢圓,然后得出考慮縱向拉伸和壓縮應(yīng)力極限1353Mpa之間的代數(shù)差。
因?yàn)橛梢粋€標(biāo)準(zhǔn)拉伸試驗(yàn)裝置估算氮化試樣的力學(xué)特性的難度,材料的屈服強(qiáng)度被認(rèn)為是在范圍700/800兆帕。這個假設(shè)是有一個道理的事實(shí),即滲氮鋼的屈服強(qiáng)度比母材更高為了研究這個參數(shù)的不確定性的影響,屈服強(qiáng)度的下限和上限分別用于構(gòu)建馮米塞斯橢圓。在圖11馮?米塞斯橢圓形的曲軸殘余應(yīng)力的評價顯示: AB偏轉(zhuǎn)角θ大約75度,殘余應(yīng)力在縱向和圓周方向,由點(diǎn)C的坐標(biāo)所表示的范圍內(nèi),列于表6。因此,6%的屈服強(qiáng)度的不確定性導(dǎo)致在18%的所計(jì)算的殘余應(yīng)力的變化。
對于疲勞性的評價,曲軸是下一個拉壓負(fù)荷測試,用60千牛頓為106個循環(huán)的初始負(fù)載,然后所施加的負(fù)荷增加到90千牛頓。在第一步驟中,負(fù)載,在測試過程中測得的應(yīng)變曲線沒有相當(dāng)大的修改,均發(fā)現(xiàn)檢測既不用沒有明顯的表面裂紋宏觀光學(xué)調(diào)查,也不符合滲透劑無損墨評估。在第二個步驟-負(fù)荷中,應(yīng)變片數(shù)4突出顯示,從試驗(yàn)開始,拉伸和壓縮區(qū)域之間的負(fù)載 - 應(yīng)變偏轉(zhuǎn)角的如圖所示12(a),這表明存在應(yīng)變片下存在表面疲勞裂紋。應(yīng)變片4的負(fù)載 - 應(yīng)變圖中的變形變得更加明顯隨著載荷循環(huán)的增加,直到本身出現(xiàn)繞100循環(huán)應(yīng)變片的失敗,確認(rèn)一個表面疲勞裂紋的存在,也指出了由增量在應(yīng)變片14的正應(yīng)變。經(jīng)過103個循環(huán)的第二步加載應(yīng)變片也失敗,可見裂紋已經(jīng)傳播到在對面的圓角 ,從如預(yù)期般沿45度平面主軸頸數(shù)值分析。曲軸然后被測試,直到完成斷裂發(fā)生在第二步驟中加載的個周期。
6結(jié)論
文的目的是數(shù)值模擬和實(shí)驗(yàn)研究氣體滲氮上的船用柴油機(jī)曲軸的疲勞行為的影響。準(zhǔn)確彈性和彈塑性有限元模型被建立,論對于曲軸和用于具有部分還原和一個圓角半徑相同的式樣,這些曲軸的評價應(yīng)力狀態(tài),并在關(guān)鍵區(qū)域的應(yīng)力集中系數(shù)下彎曲,并估算殘余應(yīng)力場的影響。實(shí)驗(yàn)結(jié)果與數(shù)值吻合良好,并指出,主體和曲柄銷軸頸圓角之間的45度的平面是從視圖的角度來看最關(guān)鍵的耐疲勞性。
一個創(chuàng)新的簡化實(shí)驗(yàn)過程由下彎曲應(yīng)變測量的方法來確定殘余應(yīng)力場也被開發(fā)。進(jìn)行在曲軸部分的實(shí)驗(yàn)測試指出的殘余應(yīng)力場,從而降低了最大拉伸彎曲應(yīng)力的有益效果。
- 20 -