
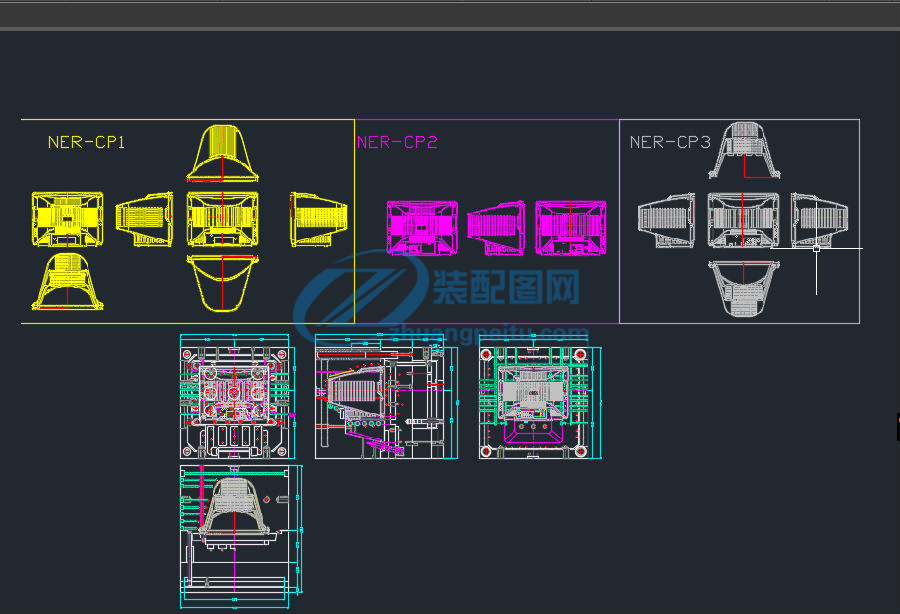
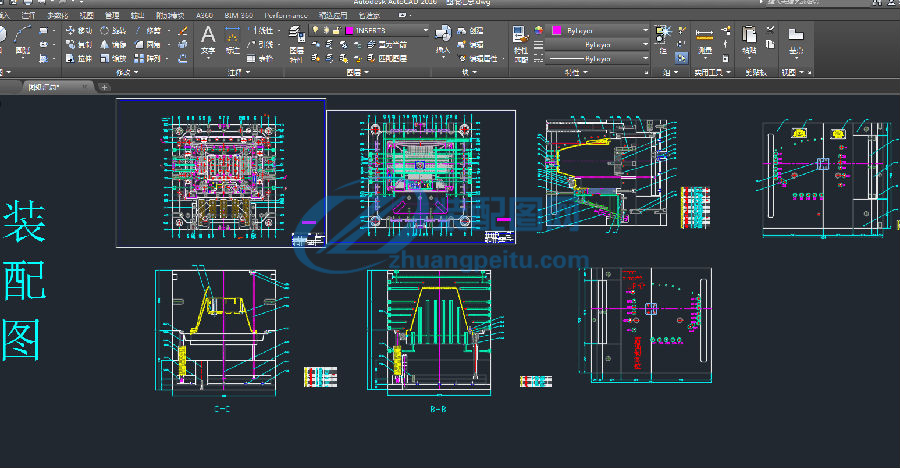


如上圖所示塑料制件(電視機后殼),材料采用HIPS(高沖擊聚苯乙烯) 收縮率0.4 %密度1.06注射溫度177-316 注射壓力 10-30MP合適的薄厚2-3mm。一 工藝性分析1、 該制件一般精度等級。 2、 尺寸大,型腔深且壁厚,因此采用直接澆口。 3、 為了方便加工與熱處理,采用拼鑲結(jié)構(gòu)。 二 主要工作部位尺寸的確定產(chǎn)品尺寸:附圖 1、2、3、4、5、6、7前模鑲件:附圖 2后模鑲件:附圖 3行位尺寸:附圖 4三 模具結(jié)構(gòu)設(shè)計1.導(dǎo)向構(gòu)的設(shè)計導(dǎo)向機構(gòu)是保證動定?;蛏舷履:夏r正確定位和導(dǎo)向的零件。 導(dǎo)向機構(gòu)的形式主要有導(dǎo)柱導(dǎo)向和錐面定位兩種。一、 導(dǎo)向機構(gòu)的作用1. 定位作用 模具閉合后,保證動定?;蛏舷履N恢谜_,保證行腔的形狀和尺寸精確;導(dǎo)向機構(gòu)在模具裝配過程中也起到定位作用,便于裝配和調(diào)整。2. 導(dǎo)向作用 合模時,首先是導(dǎo)向零件的接觸,引導(dǎo)動定?;蛏舷履?zhǔn)確閉合,避免型芯先進入行腔,造成成型零件的損壞。3. 承受一定的側(cè)向壓力 塑料熔體在充模過程中可能產(chǎn)生單向側(cè)壓力,或者由于成型設(shè)備精度低的影響,使導(dǎo)柱承受了一定的側(cè)向壓力,一保證模具的正常工作。若側(cè)向壓力不大時,不能單靠導(dǎo)柱來承擔(dān),需增設(shè)錐面定位機構(gòu)。二、導(dǎo)柱導(dǎo)向機構(gòu)導(dǎo)柱導(dǎo)向機構(gòu)的主要零件是導(dǎo)柱和導(dǎo)套。主要應(yīng)用于動定模導(dǎo)向及針板推出機構(gòu)導(dǎo)向,如右圖所示,其結(jié)構(gòu)形式見標(biāo)準(zhǔn)件。動定模導(dǎo)柱導(dǎo)向應(yīng)合理均布于模具分型面的四周,導(dǎo)柱中心至模具邊緣應(yīng)不小于其直徑的 1 倍。為防止動定模裝配或合模時錯位,導(dǎo)柱的布置可采用等直徑導(dǎo)柱不對稱布置。針板推出機構(gòu)導(dǎo)柱不對稱布置,針板推出機構(gòu)導(dǎo)柱應(yīng)四角對稱均布。三、錐面定位機構(gòu)在成型精度要求高的大型,深腔,薄壁塑件時,型腔內(nèi)側(cè)向壓力可能引起型腔或型芯的偏移,如果這種側(cè)向壓力完全有導(dǎo)柱承擔(dān),會造成導(dǎo)柱折短或咬死,這時除了設(shè)置導(dǎo)柱導(dǎo)向外,應(yīng)增設(shè)錐面定位機構(gòu),如右圖所示通常我們在兩錐面間留有間隙,在型腔一側(cè)鑲上淬火耐磨塊,使它與兩錐面配合,阻止型腔與型芯的偏移。淬火耐磨塊結(jié)構(gòu)形式見標(biāo)準(zhǔn)件。在錐面定位機構(gòu)設(shè)計中要注意錐面配合形式,型芯應(yīng)環(huán)抱型腔,型腔則無法向外張開,在分型面上不會形成間隙,同時也避免分型面上排氣槽益料傷人。2.澆注系統(tǒng)的設(shè)計澆注系統(tǒng)的設(shè)計原則:1 了解塑料的成型性能和塑料的流動性.設(shè)計澆注系統(tǒng)應(yīng)適用于所用塑料的成型特性要求以保證塑料制作的質(zhì)量2 采用盡量短的流程,以減少熱量與壓力的損失.3 防止型芯變形和鑲件位移.盡量避免直沖型芯和鑲件.4 便于修整澆口,以保證產(chǎn)品外觀質(zhì)量5 在一模多腔時,澆注系統(tǒng)應(yīng)結(jié)合型芯排位同時考慮.應(yīng)在設(shè)計時盡可能的保證在同一時間塑料溶體充滿各型腔.一. 主流道是澆注系統(tǒng)中從注射機噴嘴與模具向接觸的部位開始,到分流道為止的塑料熔體的流動通道。二. 分流道是指主流倒末端與澆口之間這一段塑料熔體的流動通道。它是澆注系統(tǒng)中熔融狀態(tài)的塑料由主流道流型腔前,通過截面積的變化及流向轉(zhuǎn)換以獲得平穩(wěn)的過渡段,因此分流道設(shè)計應(yīng)能滿足良好的壓力傳輸和保持理想的填充狀態(tài),使塑料熔體盡快的流經(jīng)分流道充滿型腔。并且流動過程中壓力損失及熱量損失盡可能小,能將塑料溶體均衡地分配至型腔。為了便于機械加工及凝料脫模,分流道大多設(shè)置在分型面上。分流道截面形狀一般可分為圓形,梯形,u 形,半圓形及矩形等。分流道截面形狀及尺寸應(yīng)根據(jù)塑料的工藝特性,成型工藝條件及分流道的長度等因素來確定,從流動性,傳熱性,等方面考慮,圓形截面是分流道比較理想的形狀。常用的分流道截面形狀三. 澆口的位置及尺寸對塑件的成型性能及成型質(zhì)量影響很大,合理選擇澆口的位置是提高塑件質(zhì)量的重要環(huán)節(jié),澆口位置不同,也將直接影響模具的結(jié)構(gòu)。要使塑件具有良好的性能與外觀,使塑件的成型在技術(shù)上合理,經(jīng)濟上可行,一定要考慮澆口位置的選擇。在設(shè)計實踐中,澆口位置的選擇通常要遵循以下原則:(1)澆口位置的安排應(yīng)該保證塑料熔體迅速及均勻地充填型腔,并盡量縮短熔體的流動距離。(2)盡量避免或減少熔接痕跡,并要同時考慮熔接痕跡對塑件質(zhì)量及強度的影響。(3)澆口的位置一般應(yīng)設(shè)在塑件壁的最厚處,以便于壓力的傳遞及補射作用的進行。(4)必須便于型腔氣體的排除,避免型腔氣體的滯留。(5)避免注射時產(chǎn)生蛇形流動。(6)由于澆口位置附近強度較弱,一般不在承受沖擊載荷或彎曲的部位設(shè)置澆口。(7)澆口的設(shè)置應(yīng)該考慮塑件的外觀質(zhì)量,不在影響塑件質(zhì)量及美觀的部位設(shè)置澆口。常用澆口形式:1: 直接澆口 : 塑料熔體直接由主流道進入型腔 ,因此具有流動阻力,料流速度快及及補縮時間長的特點,但注射壓力直接作用在塑件上,容易在進料處產(chǎn)生較大的殘余應(yīng)力而導(dǎo)致塑件翹曲變形,澆口痕跡也較明顯.這類澆口多用于單型腔模具,注射成型大型后壁長流程型腔的塑件。2: 側(cè)澆口 : 又稱標(biāo)準(zhǔn)澆口, 一般設(shè)在分型面上,于型腔的側(cè)面充模,此澆口易加工,修整方便,可靈活的選擇進料的位置,應(yīng)用較廣泛,普遍用于中小型多型腔模具,但有澆口痕跡存在,會形成熔接痕 縮孔,氣孔等缺陷,且注射壓力損失大,對深型腔排氣不便 .3 : 澆口: 這類澆口由于前后存在較大的壓力差,流動性增強,利于充模,并且去除澆口后殘留痕跡小,也利于自動化操作但壓力損失大,收縮大,塑件易變形,同時在定模部分需加一個分型面,以便澆口凝料脫模. 4: 潛伏澆口: 由點澆口演變而來 ,分流道位于分型面上,通過型腔側(cè)面斜向注入型腔,不致因澆口痕跡而影響塑件表面質(zhì)量及美觀效果。澆口采用圓形或橢圓形截面,錐角取 10~20度,在推出塑件時,由于澆口及分流道成一定斜角與型腔相連,形成能切斷澆口的刃口,這一刃口所形成的剪切力可以將澆口切斷。四 . 在完成一次注射循環(huán)的間隔,注射機噴嘴和主流道入口小端間的溫度會低于所要求的塑料溶體溫度,從噴嘴端部到注射機`料筒以內(nèi)約 10~25mm 的深度有個溫度逐漸升高的區(qū)域,這時才能達到正常的塑料熔體溫度。位于這一區(qū)域內(nèi)的塑料的流動性能及成型性能不佳,如果這里溫度相對較低的冷料冷料進入型腔,便會產(chǎn)生次品。為克服這一現(xiàn)象的影響,用一個井穴將主流道延長以接受冷料,防止冷料進入澆注系統(tǒng)的流道和型腔,把這一用來容納注射間隔所產(chǎn)生的冷料的井穴稱為冷料穴。冷料穴一般開設(shè)在主流道對面的動模板上(既塑料流動的轉(zhuǎn)向處) ,其標(biāo)稱直徑與主流道大端直徑相同或稍大一些,深度約為直徑的 1~1.5 倍,最終要保證冷料的體積小于冷料穴的體積。有時因分流道較長塑料熔體充模的溫度較大時,也要在其延伸端開設(shè)較小的冷料穴,以防止分流道末端的冷料進入型腔。冷料穴除了具有容納冷料以外,同時還具有在開摸時將主流道和分流道的冷料勾住,使其保留在動模一側(cè),便于脫模的功能。3:推出機構(gòu)的設(shè)計 塑件在從模具上取下之前,還有一個從模具的成型零件上脫出的過程,使塑件從成型零件上脫出的機構(gòu)稱為推出機構(gòu),推出機構(gòu)的動作是通過裝在注塑機合模機構(gòu)上的頂棍或液壓缸來完成的。推出機構(gòu)主要由推出零件(頂針,司筒,拉料桿,推方,斜頂?shù)龋?,頂針板,低針板,推出機構(gòu)的導(dǎo)向與復(fù)位部位(推板導(dǎo)柱導(dǎo)套,推桿推司,復(fù)位桿,彈簧,強制復(fù)位法蘭等)組成。1— 司筒內(nèi)針 2—復(fù)位桿 3—彈簧 4—司筒外針 5—底針板 6—面針板7—推桿 8—推司 9—推塊 10—推板導(dǎo)柱 11—推板導(dǎo)套 12—強復(fù)位法蘭 13—格釘 14—延時針 15—頂針 推出機構(gòu)的設(shè)計原則:1. 推出機構(gòu)應(yīng)盡量設(shè)置在動模一側(cè),由于推出機構(gòu)的動作是通過裝在注射機合模機構(gòu)上的頂棍來驅(qū)動的,所以一般情況下,推出機構(gòu)設(shè)置在動模一側(cè),在分型面設(shè)計時應(yīng)盡量注意,開模后使塑件能留在動模一側(cè)。2. 保證塑件不應(yīng)推出而變形損壞,為了保證塑件在推出過程中不變形,不損壞,設(shè)計時應(yīng)仔細分析塑件對模具的包緊力和黏附力的大小,合理的選擇推出方式及推出位置,從而使塑件受力均勻,不變形,不損壞。3. 機構(gòu)簡單動作可靠,推出機構(gòu)應(yīng)使推出動作可靠靈活,機構(gòu)本身要有足夠的強度,剛度和硬度,以承受推出過程中的各種力的作用,確保塑件順利地脫模。4. 良好的塑件外觀,推出塑件的位置應(yīng)盡量設(shè)在塑件內(nèi)部,以便推出痕跡影響塑件的外觀質(zhì)量。5. 合模時的正確復(fù)位,設(shè)計推出機構(gòu)時,還必須考慮合模機構(gòu)的正確復(fù)位,并保證不與其他模具零件干涉。頂針?biāo)就驳臋C構(gòu)的配合形式如右圖4:復(fù)位機構(gòu)的設(shè)計為了保證推出機構(gòu)在工作過程中的靈活,復(fù)位,每次合模后, 推出元件能回到原來的位置,通常還需要設(shè)計推出機構(gòu)的導(dǎo)向與復(fù)位裝置。一導(dǎo)向零件推出機構(gòu)的導(dǎo)向零件,通常由推板 導(dǎo)柱與導(dǎo)套所組成,導(dǎo)向零件使各推出元件得以保持一定的配合間隙,從而保證推出和復(fù)位動作的順利進行,導(dǎo)柱應(yīng)四角對稱均布。二復(fù)位零件1.復(fù)位桿復(fù)位 為了使推出元件合模后順利回到原來的位置,面針板四角裝有復(fù)位桿。復(fù)位桿采用圓形截面,其位置盡量設(shè)置在面針板四周,以便推出機構(gòu)合模時復(fù)位桿復(fù)位,復(fù)位桿端部與所在動模分型面平齊。推出機構(gòu)推出后,復(fù)位桿高出分型面(其高度即位推出距離的大?。?。復(fù)位桿復(fù)位作用是利用合模動作來完成的,合模時,復(fù)位桿先與動模分型面與定模分型面接觸,在動模向定模逐漸合攏的過程中,推出機構(gòu)便被復(fù)位桿頂住,從而與動模產(chǎn)生相對移動,直至分型面合攏時,推出機構(gòu)便回到原來的位置,這種結(jié)構(gòu)合模和復(fù)位同時完成。2.彈簧先復(fù)位 彈簧復(fù)位是利用彈簧的彈力使推出機構(gòu)復(fù)位。彈簧復(fù)位與復(fù)位桿復(fù)位的主要區(qū)別是:彈簧復(fù)位是推出機構(gòu)的復(fù)位先與合模動作完成,為了便于活動部件如推方的安放而采用彈簧先復(fù)位機構(gòu)。合模一定距離后,在彈簧力的作用下,推出機構(gòu)先復(fù)位,為了避免工作時彈簧扭斜,可將彈簧安裝在復(fù)位桿或?qū)д斏?,此類設(shè)計須綜合考慮彈簧的預(yù)壓縮,最大壓縮量及模具注塑行程等問題。3 強復(fù)位機構(gòu) 為了有效保證推出機構(gòu)完全復(fù)位,將注塑機頂棍與底針板剛性機械連接起來,開模后,頂棍帶動推出機構(gòu)推出塑件,回程時有帶動推出機構(gòu)強行復(fù)位。為了模具的安全可靠性能,在模具設(shè)計中,以上三種復(fù)位方式通常綜合運用,在一種方式失效的情況下,另兩種方式還可以維持模具的正常工5: 冷卻系統(tǒng)的設(shè)計在注塑成型工藝過程中,模具溫度對塑料熔體的沖模流動,固化定型,注塑周期及塑件的形狀和尺寸精度具有重要影響。模溫過底,熔體流動差,塑料成型性能差,塑件輪廓不清晰,表面產(chǎn)生明顯的銀絲,云紋,甚至充不滿或形成熔接痕;模具溫度高,成型收縮率大,脫模或脫模后塑件變形大,并且易造成溢料或粘模;模溫不均勻,型腔和型芯溫度差過大,塑件收縮不均勻,導(dǎo)致塑件翹曲變形,影響塑件的形狀和尺寸精度。在注塑成型過程中,注射時間約占成型周期 5%,冷卻時間約占 80%,推出(脫模)時間約占 15%,因此,注塑周期主要取決與冷卻定型時間,而縮短冷卻時間,可通過調(diào)節(jié)塑料和模具的溫差。在保證塑件質(zhì)量和成型工藝順利進行的前提下,通過降低模具溫度來縮短冷卻時間,是提高生產(chǎn)效率的關(guān)鍵。模具的冷卻時間就是將熔融狀態(tài)的塑料傳給模具的熱量,盡可能迅速地帶走,以便塑件冷卻定型,并獲得最佳的塑件質(zhì)量。模具的冷卻方式有:水冷卻,空氣冷卻和油冷卻等,但常用的是水冷卻方法。冷卻形式一般在型腔和型芯等部位合理的設(shè)置冷卻通道,并通過調(diào)節(jié)冷卻水流量及流速來控制模溫,冷卻水一般為室溫冷水,必要時也采用低溫水來加強冷卻效率。冷卻系統(tǒng)的設(shè)計原則:冷卻系統(tǒng)的設(shè)計需考慮模具結(jié)構(gòu)形式,模具的大小,鑲塊的位置,以及塑件熔接痕位置等諸多因素,其設(shè)計原則如下:1, 冷卻水道應(yīng)盡量多,截面尺寸應(yīng)盡量大, 型腔表面的溫度與冷卻水道的數(shù)量,截面尺寸及冷卻水的溫度有關(guān)。模具內(nèi)的溫度分布為了使型腔表面溫度分布趨與均勻,防止塑件不均勻收縮和產(chǎn)生殘余應(yīng)力,在模具結(jié)構(gòu)允許的情況下,應(yīng)盡可能多設(shè)冷卻水道,并使用較大的截面尺寸。2:冷卻水道至型腔表面距離應(yīng)盡量相等。塑件壁厚均勻時,冷卻水道至型腔表面距離最好相等,即冷卻水道的排列與型腔的形狀相吻合。當(dāng)塑件壁厚不均勻時,厚壁的地方應(yīng)增加冷卻水道,加強冷卻。水道孔邊至型腔表面距離不宜太近或太遠,以免影響冷卻效果和模具的強度,其距離一般為冷卻水道的 1——2 倍。3:澆口處需加強冷卻。塑料熔體充填型腔時,澆口附近溫度最高,距澆口越遠溫度就越低,因此,澆口附近應(yīng)加強冷卻,通??墒估渌攘鹘?jīng)澆口附近,然后再流向澆口遠端。4:冷卻水道出入口溫差應(yīng)盡量小,如果冷卻水道過長,則冷卻出入口溫差就較大,易使模溫不均勻,因此設(shè)計時應(yīng)盡量單循環(huán),多排布冷卻水道。5:冷卻水道要避免接近塑件的熔接部位,以免使塑件產(chǎn)生熔接痕,降低塑件強度。6:冷卻水道內(nèi)不應(yīng)有死水或回流水的相象,應(yīng)暢通無阻。冷卻水道直徑一般為 8-12mm,進水管直徑的選擇,應(yīng)使進水處的流速不超過冷卻水道中的水流速度,要避免過大的壓力降。7:型芯的型腔要分別冷卻,且需保證冷卻的平衡,對于型芯內(nèi)部的冷卻要注意水道穿過型芯和 B 板時需密封,以防漏水。8:要防止冷卻水道中的冷卻水泄露,水管與水嘴連接處必須密封。水管接頭的部位要設(shè)置在不影響操作的方向,通常朝向注射機的背面。大型深型腔塑件的冷卻系統(tǒng)結(jié)構(gòu)形式:6: 排氣系統(tǒng)的設(shè)計在注射成型過程中,模具內(nèi)除了型腔和澆注系統(tǒng)中原有的空氣外,還有塑料受熱或凝固產(chǎn)生的底分子揮發(fā)氣體,這些氣體若不能被熔融塑料順利地排出型腔,則可能因填充時氣體被壓縮而產(chǎn)生高溫,引起塑件局部炭化燒焦,或使塑件產(chǎn)生氣泡,或使塑料熔接不良而引起塑件強度降低,甚至阻凝塑料填充等,為了使這些氣體從型腔中及時排出,在設(shè)計模具時必須考慮排氣問題。注射模的排氣方式主要有如下三種方法:1.在分型面上開設(shè)排氣槽 分型面上開設(shè)排氣槽的形式如下圖所示,排氣的間隙值根據(jù)塑料的流動性而定,通常為 0.03——0.05mm,以不產(chǎn)生溢料為限。2.;利用模具零件配合間隙排氣 頂針及鑲件與型芯配合間隙自然排氣,設(shè)計和制造都比較方便,故大多數(shù)情況都采用這種排氣方式。3.利用排氣鑲件(透氣鋼)排氣如果型腔最后填充的部位不在分型面上,其附近有無供排氣的頂針及鑲件時,如喇叭碰穿網(wǎng)孔區(qū)域,可在網(wǎng)孔中部區(qū)域鑲嵌透氣鋼(燒結(jié)的多孔金屬塊) 。 七:校核注塑機校核 參數(shù)主要有:最大注射量、注射壓力、鎖模力、開模行程、頂出裝置、噴嘴尺寸、定位孔尺寸、拉桿間距、最大模具厚度和最小模具厚度以及碼模孔尺寸。5. 成型機型號INCH 前殼 后殼 備注17〞以下 650-850 650-85021〞 850 85025〞 1300 1300-160029〞 1300-1600 1300-180032〞 1600-1800 1800-2200其它 另行說明*頂出孔必須適用對應(yīng)的各種成型機。成型機均指 LG 機械成型機。五 模具結(jié)構(gòu)確定。模架采用非標(biāo)準(zhǔn)的,詳細結(jié)構(gòu)如下附圖所示:目 錄一、工藝性分析 二、產(chǎn)品及主要工作部位尺寸的確定三、模具結(jié)構(gòu)設(shè)計1:導(dǎo)向機構(gòu)的設(shè)計2:澆注系統(tǒng)的設(shè)計3:推出機構(gòu)的設(shè)計4:復(fù)位機構(gòu)的設(shè)計5:冷卻系統(tǒng)的設(shè)計6:排氣系統(tǒng)的設(shè)計四、注塑機的選用五、模具結(jié)構(gòu)的確定