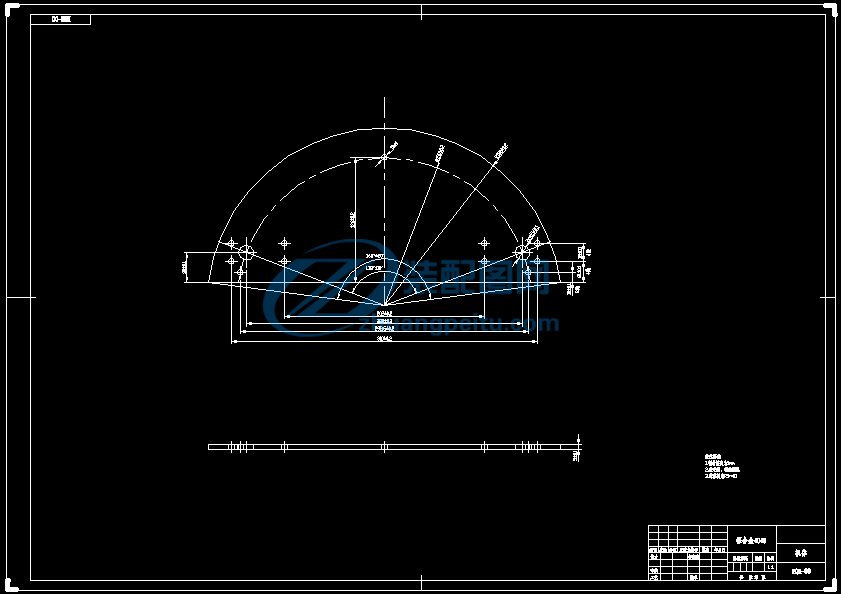
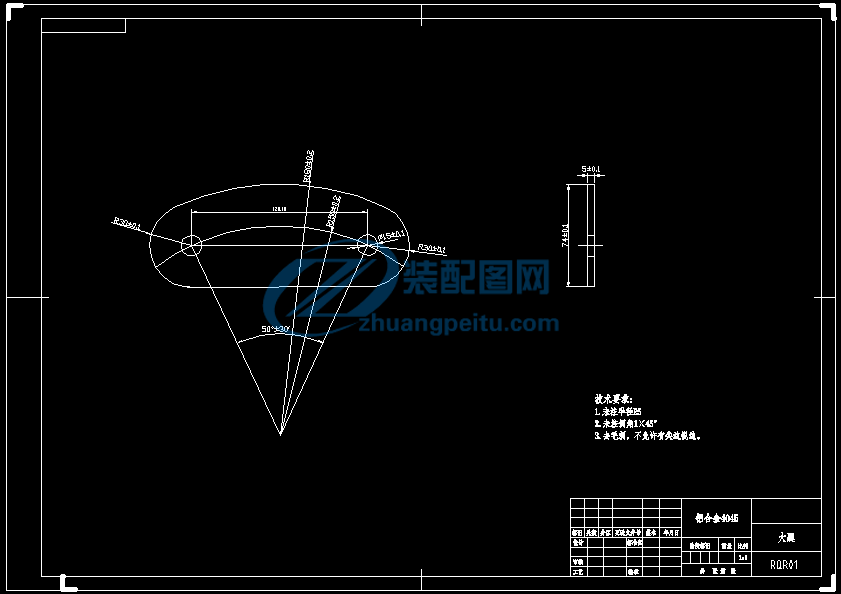
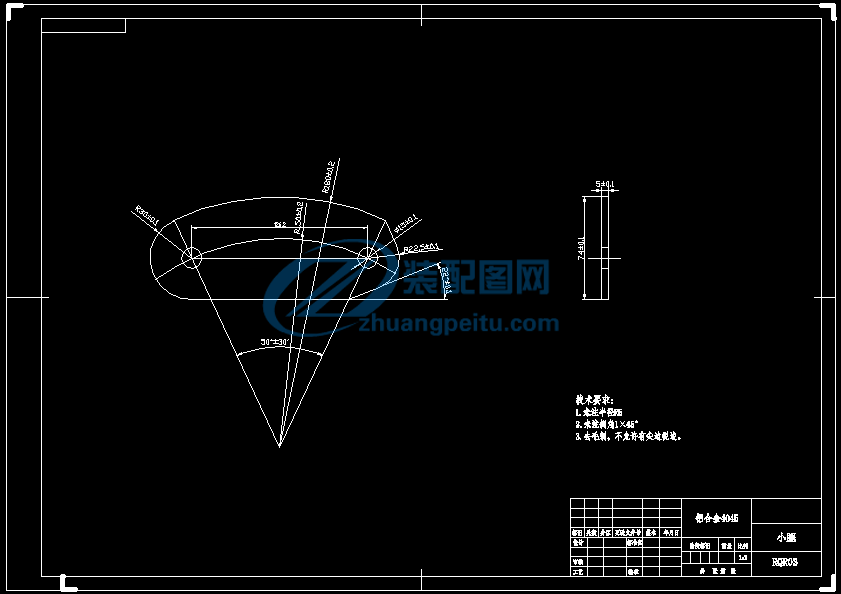
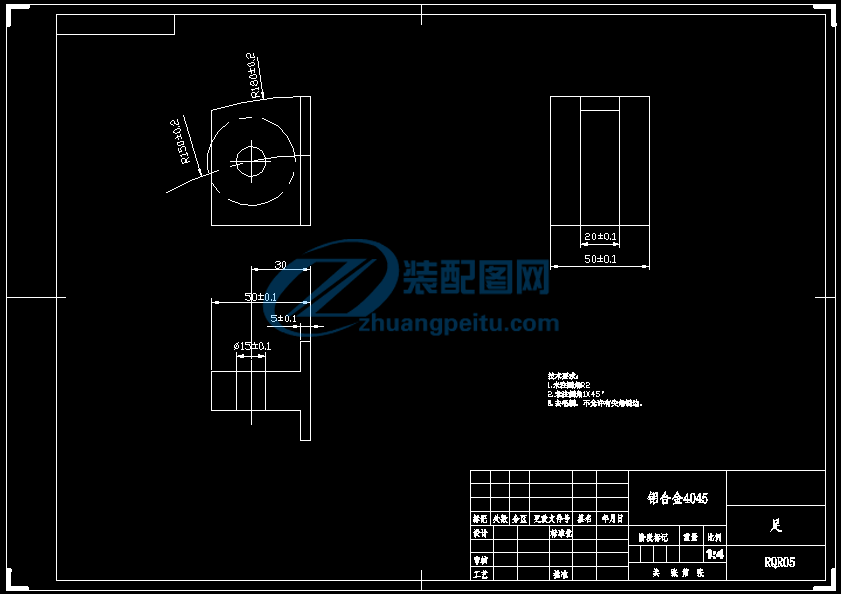

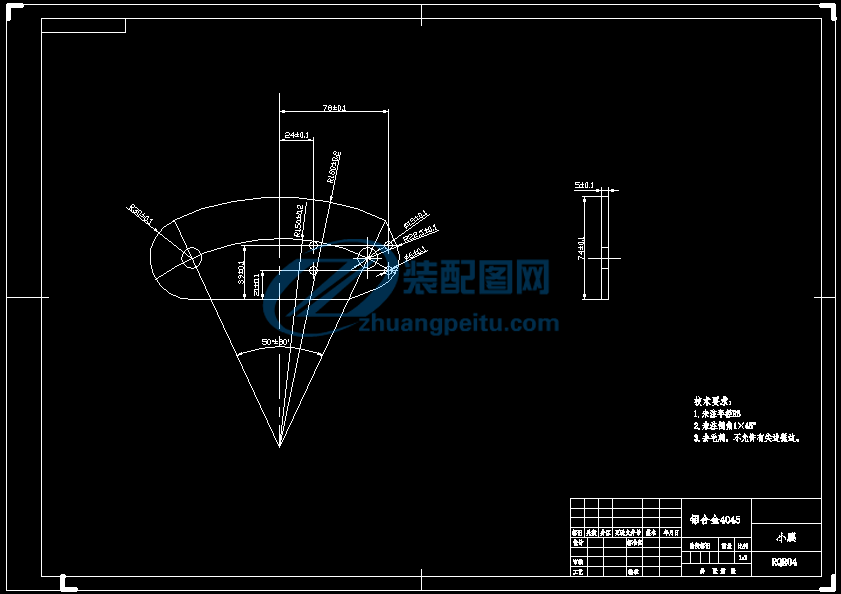
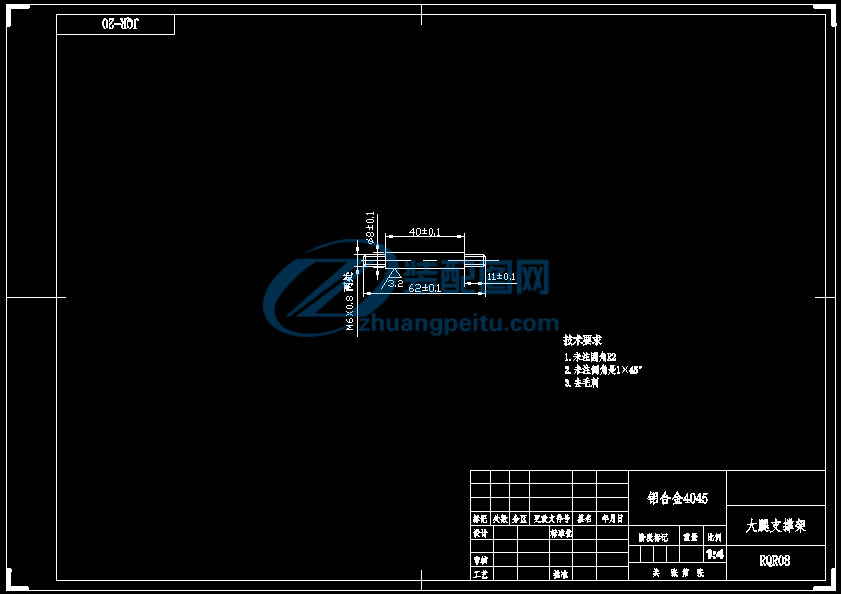
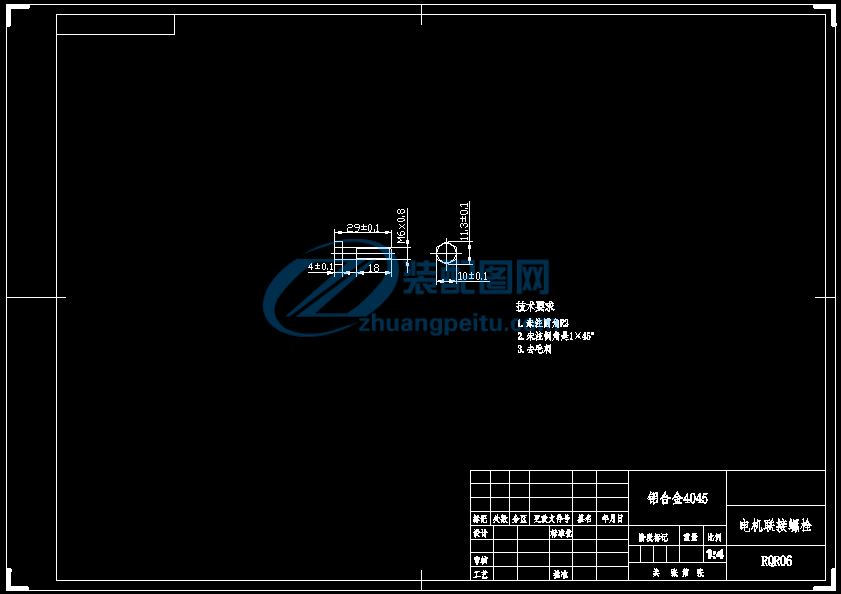
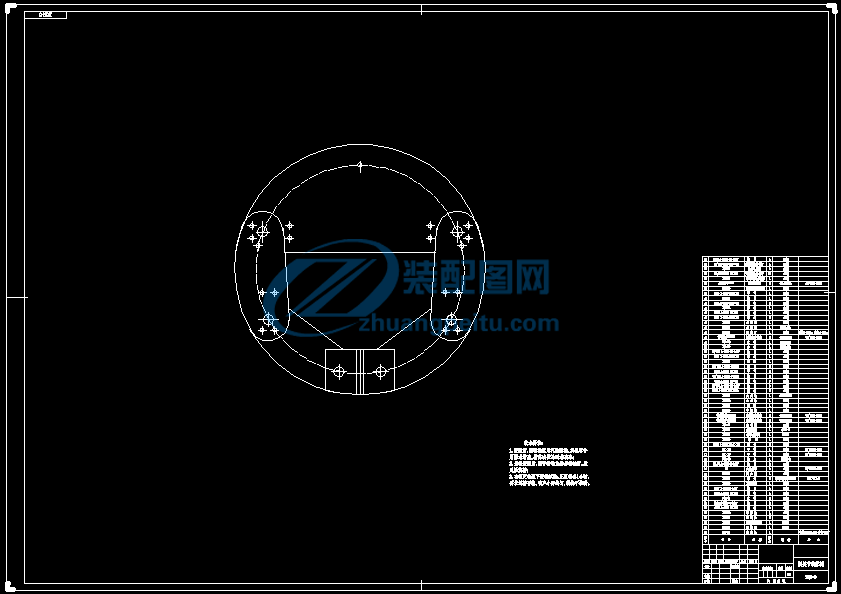
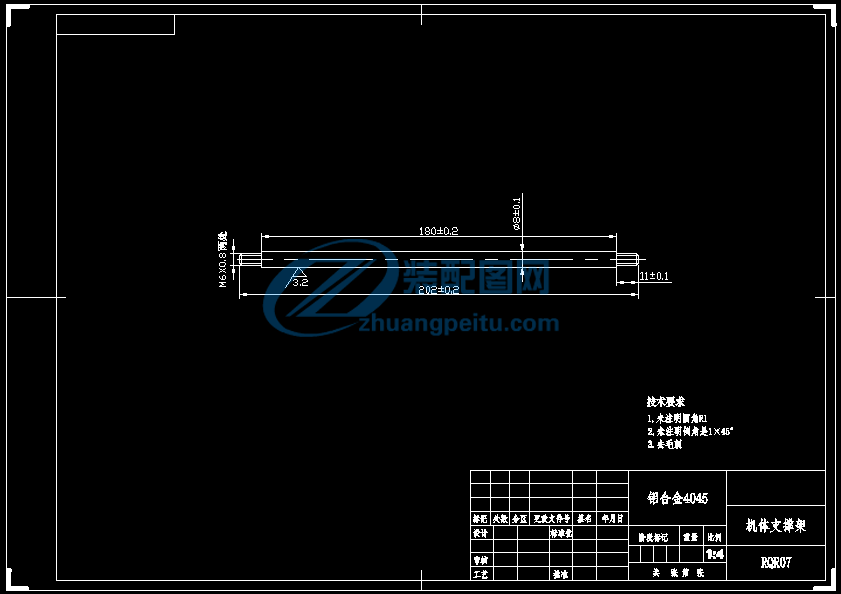
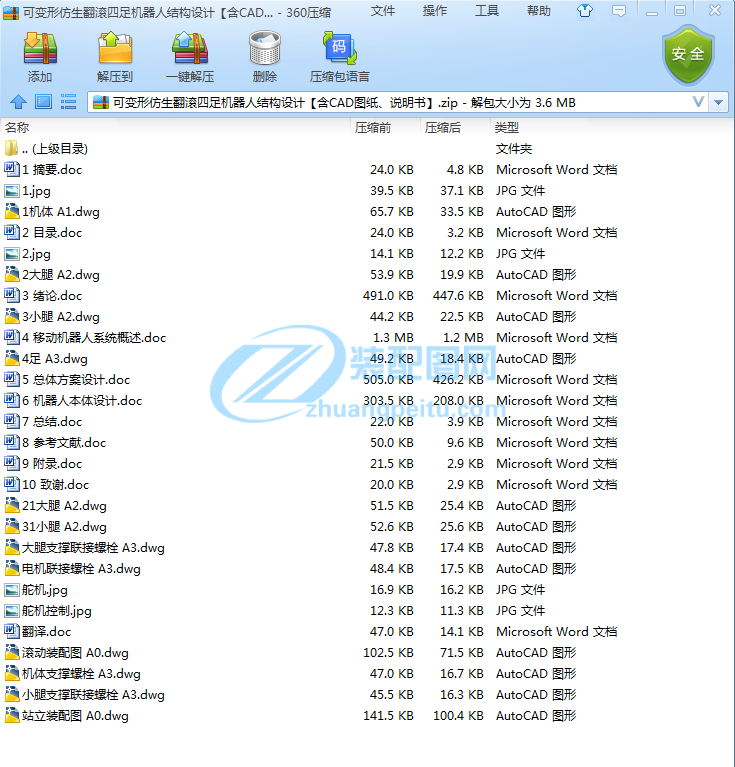
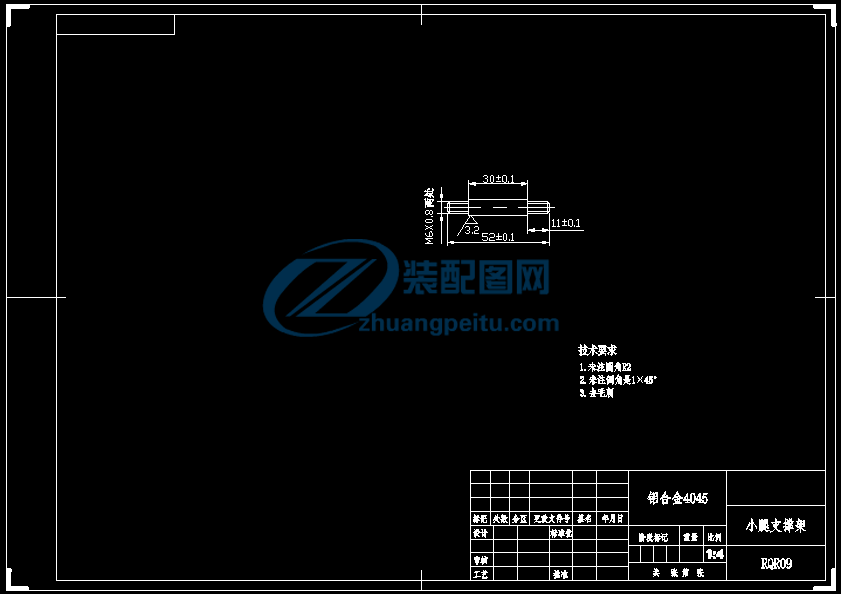
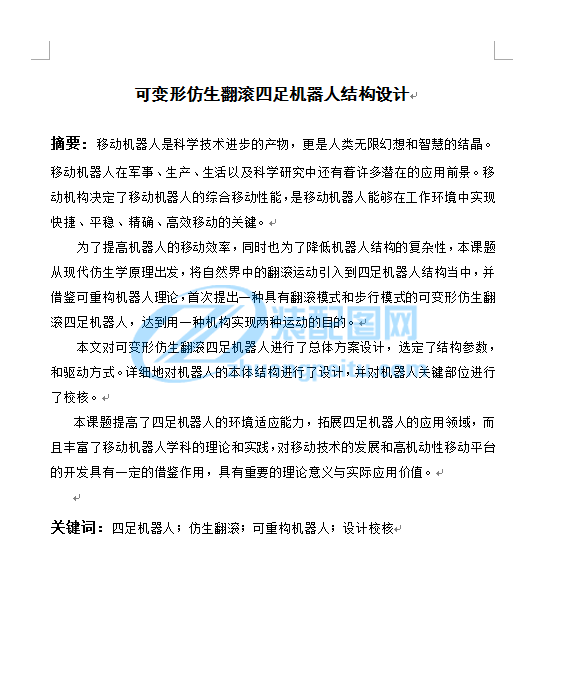
外文資料High-speed machining and demand for the development ofHigh-speed machining is contemporary advanced manufacturing technology an important component of the high-efficiency, High-precision and high surface quality, and other features. This article presents the technical definition of the current state of development of China's application fields and the demand situation.High-speed machining is oriented to the 21st century a new high-tech, high-efficiency, High-precision and high surface quality as a basic feature, in the automobile industry, aerospace, Die Manufacturing and instrumentation industries gained increasingly widespread application, and has made significant technical and economic benefits. contemporary advanced manufacturing technology an important component part.HSC is to achieve high efficiency of the core technology manufacturers, intensive processes and equipment packaged so that it has a high production efficiency. It can be said that the high-speed machining is an increase in the quantity of equipment significantly improve processing efficiency essential to the technology. High-speed machining is the major advantages : improve production efficiency, improve accuracy and reduce the processing of cutting resistance.The high-speed machining of meaning, at present there is no uniform understanding, there are generally several points as follows : high cutting speed. usually faster than that of their normal cutting 5 -10 times; machine tool spindle speed high, generally spindle speed in -20000r/min above 10,000 for high-speed cutting; Feed at high velocity, usually 15 -50m/min up to 90m/min; For different cutting materials and the wiring used the tool material, high-speed cutting the meaning is not necessarily the same; Cutting process, bladed through frequency (Tooth Passing Frequency) closer to the “machine-tool - Workpiece “system the dominant natural frequency (Dominant Natural Frequency), can be considered to be high-speed cutting. Visibility high-speed machining is a comprehensive concept.1992. Germany, the Darmstadt University of Technology, Professor H. Schulz in the 52th on the increase of high-speed cutting for the concept and the scope, as shown in Figure 1. Think different cutting targets, shown in the figure of the transition area (Transition), to be what is commonly called the high-speed cutting, This is also the time of metal cutting process related to the technical staff are looking forward to, or is expected to achieve the cutting speed.High-speed machining of machine tools, knives and cutting process, and other aspects specific requirements. Several were from the following aspects : high-speed machining technology development status and trends.At this stage, in order to achieve high-speed machining, general wiring with high flexibility of high-speed CNC machine tools, machining centers, By using a dedicated high-speed milling, drilling. These equipment in common is : We must also have high-speed and high-speed spindle system feeding system, Cutting can be achieved in high-speed process. High-speed cutting with the traditional cutting the biggest difference is that “Machine-tool-workpiece“ the dynamic characteristics of cutting performance is stronger influence. In the system, the machine spindle stiffness, grip or form, a long knife set, spindle Broach, torque tool set, Performance high-speed impact are important factors.In the high-speed cutting, material removal rate (Metal Removal Rate, MRR), unit time that the material was removed volume, usually based on the “machine-tool-workpiece“ whether Processing System “chatter.“ Therefore, in order to satisfy the high-speed machining needs, we must first improve the static and dynamic stiffness of machine spindle is particularly the stiffness characteristics. HSC reason at this stage to be successful, a very crucial factor is the dynamic characteristics of the master and processing capability.In order to better describe the machine spindle stiffness characteristics of the project presented new dimensionless parameter - DN value, used for the evaluation of the machine tool spindle structure on the high-speed machining of adaptability. DN value of the so-called “axis diameter per minute speed with the product.“ The newly developed spindle machining center DN values have been great over one million. To reduce the weight bearing, but also with an array of steel products than to the much more light ceramic ball bearings; Bearing Lubrication most impressive manner mixed with oil lubrication methods. In the field of high-speed machining. have air bearings and the development of magnetic bearings and magnetic bearings and air bearings combined constitute the magnetic gas / air mixing spindle.Feed the machine sector, high-speed machining used in the feed drive is usually larger lead, multiple high-speed ball screw and ball array of small-diameter silicon nitride (Si3N4) ceramic ball, to reduce its centrifugal and gyroscopic torque; By using hollow-cooling technology to reduce operating at high speed ball screw as temperature generated by the friction between the lead screw and thermal deformation.In recent years, the use of linear motor-driven high-speed system of up to'' Such feed system has removed the motor from workstations to Slide in the middle of all mechanical transmission links, Implementation of Machine Tool Feed System of zero transmission. Because no linear motor rotating components, from the role of centrifugal force, can greatly increase the feed rate. Linear Motor Another major advantage of the trip is unrestricted. The linear motor is a very time for a continuous machine shop in possession of the bed. Resurfacing of the very meeting where a very early stage movement can go, but the whole system of up to the stiffness without any influence. By using high-speed screw, or linear motor can greatly enhance machine system of up to the rapid response. The maximum acceleration linear motors up to 2-10G (G for the acceleration of gravity), the largest feed rate of up to 60 -200m/min or higher.2002 world-renowned Shanghai Pudong maglev train project of maglev track steel processing, Using the Shenyang Machine Tool Group Holdings Limited McNair friendship company production plants into extra-long high-speed system for large-scale processing centers achieve . The machine feeding system for the linear guide and rack gear drive, the largest table feed rate of 60 m / min, Quick trip of 100 m / min, 2 g acceleration, maximum speed spindle 20000 r / min, the main motor power 80 kW. X-axis distance of up to 30 m, 25 m cutting long maglev track steel error is less than 0.15 mm. Maglev trains for the smooth completion of the project provided a strong guarantee for technologyIn addition, the campaign machine performance will also directly affect the processing efficiency and accuracy of processing. Mold and the free surface of high-speed machining, the main wiring with small cut deep into methods for processing. Machine requirements in the feed rate conditions, should have high-precision positioning functions and high-precision interpolation function, especially high-precision arc interpolation. Arc processing is to adopt legislation or thread milling cutter mold or machining parts, the essential processing methods.Cutting Tools Tool Material development high-speed cutting and technological development of the history, tool material is continuous progress of history. The representation of high-speed cutting tool material is cubic boron nitride (CBN). Face Milling Cutter use of CBN, its cutting speed can be as high as 5000 m / min, mainly for the gray cast iron machining. Polycrystalline diamond (PCD) has been described as a tool of the 21st century tool, It is particularly applicable to the cutting aluminum alloy containing silica material, which is light weight metal materials, high strength, widely used in the automobile, motorcycle engine, electronic devices shell, the base, and so on. At present, the use of polycrystalline diamond cutter Face Milling alloy, 5000m/min the cutting speed has reached a practical level. In addition ceramic tool also applies to gray iron of high-speed machining;Tool Coating : CBN and diamond cutter, despite good high-speed performance, but the cost is relatively high. Using the coating technology to make cutting tool is the low price, with excellent mechanical properties, which can effectively reduce the cost. Now high-speed processing of milling cutter, with most of the wiring between the Ti-A1-N composite technology for the way of multi-processing, If present in the non-ferrous metal or alloy material dry cutting, DLC (Diamond Like Carbon) coating on the cutter was of great concern. It is expected that the market outlook is very significant;Tool clamping system : Tool clamping system to support high-speed cutting is an important technology, Currently the most widely used is a two-faced tool clamping system. Has been formally invested as a commodity market at the same clamping tool system are : HSK, KM, Bigplus. NC5, AHO systems.In the high-speed machining, tool and fixture rotary performance of the balance not only affects the precision machining and tool life. it will also affect the life of machine tools. So, the choice of tool system, it should be a balanced selection of good products.Process Parameters.Cutting speed of high-speed processing of conventional shear velocity of about 10 times. For every tooth cutter feed rate remained basically unchanged, to guarantee parts machining precision, surface quality and durability of the tool, Feed volume will also be a corresponding increase about 10 times, reaching 60 m / min, Some even as high as 120 m / min. Therefore, high-speed machining is usually preclude the use of high-speed, feed and depth of cut small cutting parameters. Due to the high-speed machining cutting cushion tend to be small, the formation of very thin chip light, Cutting put the heat away quickly; If the wiring using a new thermal stability better tool materials and coatings, Using the dry cutting process for high-speed machining is the ideal technology program.High-speed machining field of application.Flexible efficient production line.To adapt to the needs of new models, auto body panel molds and resin-prevention block the forming die. must shorten the production cycle and reduce the cost of production and, therefore, we must make great efforts to promote the production of high-speed die in the process. SAIC affiliated with the company that : Compared to the past, finishing, further precision; the same time, the surface roughness must be met, the bending of precision, this should be subject to appropriate intensive manual processing. Due to the extremely high cutting speed, and the last finishing processes, the processing cycle should be greatly reduced.To play for machining centers and boring and milling machining center category represented by the high-speed machining technology and automatic tool change function of distinctions Potential to improve processing efficiency, the processing of complex parts used to be concentrated as much as possible the wiring process, that is a fixture in achieving multiple processes centralized processing and dilute the traditional cars, milling, boring, Thread processing different cutting the limits of technology, equipment and give full play to the high-speed cutting tool function, NC is currently raising machine efficiency and speed up product development in an effective way. Therefore, the proposed multi-purpose tool of the new requirements call for a tool to complete different parts of the machining processes, ATC reduce the number of ATC to save time, to reduce the quantity and tool inventory, and management to reduce production costs. More commonly used in a multifunctional Tool, milling, boring and milling, drilling milling, drilling-milling thread-range tool. At the same time, mass production line, against the use of technology requires the development of special tools, tool or a smart composite tool, improve processing efficiency and accuracy and reduced investment. In the high-speed cutting conditions, and some special tools can be part of the processing time to the original 1 / 10 below, results are quite remarkable.HSC has a lot of advantages such as : a large number of materials required resection of the workpiece with ultrafine, thin structure of the workpiece, Traditionally, the need to spend very long hours for processing mobile workpiece and the design of rapid change, short product life cycle of the workpiece, able to demonstrate high-speed cutting brought advantages.中文翻譯高速加工和高速加工的發(fā)展,高效率,高精度,高表面質(zhì)量,以及其他功能是當代先進制造技術(shù)的重要組成部分。本文主要介紹技術(shù)定義,目前的狀況發(fā)展,我國的應(yīng)用領(lǐng)域和需求情況。 高速加工是面向 21 世紀的一門新興的高科技,高效率,高精度,高表面質(zhì)量的一門工藝,在汽車行業(yè),航空航天,模具制造和儀器儀表行業(yè)日益得到廣泛應(yīng)用,并已取得了重大技術(shù)和經(jīng)濟利益,是當代先進制造技術(shù)的重要組成部分。 高速加工是實現(xiàn)高效率的核心技術(shù),制造商,密集的生產(chǎn)工序和設(shè)備,包裝,使其具有較高的生產(chǎn)效率??梢哉f,高速加工是提高設(shè)備的數(shù)量顯著提高加工效率必不可少的技術(shù)。高速加工的主要優(yōu)點是:提高生產(chǎn)效率,提高準確性和減少加工切削阻力。高速加工中的意義,目前還沒有統(tǒng)一的理解,有一般的幾點如下:高切削速度。通??煊谡G懈?5-10 倍;機床主軸轉(zhuǎn)速高,一般轉(zhuǎn)速在 -20000r/min 高速切削;送料速度很高,通常為 15 -50m/min;對于不同的切削材料和電線用刀具材料,高速切削的含義不一定是相同的;切削過程中,刀片通過頻率(傳遞頻率)更接近于“機床 -工件” 系統(tǒng)的優(yōu)勢自然頻率(主導的固有頻率) ,可以被認為是高速切削??梢姼咚偌庸な且粋€綜合概念。 1992 年。德國達姆施塔特技術(shù)大學教授舒爾茨閣下增加高速切削的概念和范圍,認為不同的切割指標,圖中所示的過渡區(qū)(過渡) ,是所謂的高速切削,這也是金屬切削過程中有關(guān)技術(shù)人員正期待著,或者是預(yù)計能實現(xiàn)的切削速度。高速加工機床,刀具和切削過程,和其他方面的具體要求主要來自以下幾個方面:高速加工技術(shù)發(fā)展現(xiàn)狀和趨勢。在這一階段,為了實現(xiàn)高速加工,一般電線具有高靈活性的高速數(shù)控機床,加工中心,通過一個專用的高速銑,鉆。這些設(shè)備的共同特點是:我們還必須有高速和高速主軸系統(tǒng)喂料系統(tǒng),切割,才能實現(xiàn)高速進程。高速切削與傳統(tǒng)切削的最大區(qū)別是,“機床,工件”的動態(tài)特性,切削性能強的影響力。在該系統(tǒng)中,機床主軸的剛度,控制或形式,長期套刀,主軸拉刀,扭矩工具,性能高,速度的影響的重要因素。 在高速切削,材料去除率(金屬去除率,降低死亡率) ,單位時間的材料去除量,通常是根據(jù)“機床,工件”是否處理系統(tǒng)“聊天” 。因此,為了滿足高速加工的需求,我們必須首先提高靜態(tài)和動態(tài)剛度,尤其是機床主軸的剛度特性。造血干細胞的理由在這個階段要取得成功,一個非常關(guān)鍵的因素是動態(tài)特性的掌握和處理能力。為了更好地描述了機床主軸剛度特性的項目提出了新的無量綱參數(shù)- DN 值,用于評估機床主軸結(jié)構(gòu)對高速加工的適應(yīng)性。 DN 值所謂的“邪惡軸心直徑速度每分鐘的產(chǎn)品。 ”新開發(fā)的加工中心主軸的 DN 值已超過 100 萬偉大。為了減少負重,而且還提供了一系列的鋼鐵產(chǎn)品,而不是更加輕陶瓷球軸承,軸承潤滑最令人印象深刻的方式混合油潤滑的方法。領(lǐng)域中的高速加工。有空氣軸承和發(fā)展磁力軸承和磁力軸承和空氣軸承相結(jié)合構(gòu)成的磁氣體/空氣混合主軸。 飼料機械部門,高速加工飼料中使用驅(qū)動器通常是較大的鉛,多個高速滾珠絲杠和球的小直徑氮化硅( Si3N4 陶瓷)陶瓷球,以減少其離心和陀螺力矩;使用中空冷卻技術(shù),以降低運營高速滾珠絲杠作為所產(chǎn)生的溫度之間的摩擦和絲杠熱變形。 近年來,利用直線電機驅(qū)動的高速系統(tǒng)最多''這種飼料系統(tǒng)已經(jīng)取消了汽車從工作站幻燈片中所有的機械傳動鏈,實現(xiàn)機床進給系統(tǒng)的零傳動。由于沒有直線電機旋轉(zhuǎn)部件,從離心力的作用,可以大大提高了進給速度。直線電機的另一個主要優(yōu)勢,此行是無限制的。直線電機是一種非常的時間,連續(xù)車間擁有床位。重的非常會議上,非常初級的階段,可以去運動,但整個系統(tǒng)的行動的剛度沒有任何影響。通過使用高速螺絲,或直線電機可以大大提高計算機系統(tǒng)的行動的快速反應(yīng)。最大加速度直線電機的 2 -萬兆( G 的重力的重力加速度) ,最大進給速度高達 60 -200m/min 或更高。 2002 年世界著名的上海浦東磁懸浮列車項目的磁懸浮軌道鋼鐵加工,利用沉陽機床集團控股有限公司捷友誼公司的生產(chǎn)工廠到超長高速系統(tǒng)的大型加工中心實現(xiàn)。本機進給系統(tǒng)的直線導軌和齒條齒輪傳動,最大的表進給速度 60 米/分,快速行程為 100 米/分鐘,二克加速,最高時速主軸 20000 轉(zhuǎn)/分,主電機功率 80 千瓦。X 軸的距離可達 30 米,長 25 米切削鋼磁懸浮軌道誤差小于 0.15毫米。磁懸浮列車的順利完成該項目提供了強有力的保證技術(shù) 。此外,該系列機器的性能也將直接影響到加工效率和精度加工。模具和自由表面的高速加工,主要的線路與小切口深的方法進行處理。機所需飼料率條件下,應(yīng)該有高精密定位功能和高精度的插值函數(shù),特別是高精密圓弧插補。電弧處理是通過立法或螺紋銑刀加工模具或零件的基本處理方法。 刀具刀具材料的發(fā)展,高速切削技術(shù)的發(fā)展歷史,是刀具材料不斷進步的歷史。代表性的高速切削刀具材料是立方氮化硼( cBN ) 。面銑刀使用立方氮化硼,其切削速度可高達五 000 米/分鐘,主要用于灰鑄鐵加工。聚晶金剛石(聚晶金剛石)已被描述為一個工具, 21 世紀的工具,它特別適用于切割含有硅鋁合金材料,這是重量輕金屬材料,強度高,廣泛應(yīng)用于汽車,摩托車發(fā)動機,電子設(shè)備的外殼,該基地,等等。目前,使用聚晶金剛石刀具面銑刀合金, 5000m/min 的切削速度已達到實用水平。此外陶瓷刀具也適用于灰口鑄鐵的高速加工; 刀具涂層:立方氮化硼和金剛石刀具,盡管良好的高速性能,但成本也相對較高。采用涂層技術(shù),使刀具的價格低,具有優(yōu)良的力學性能,可有效降低成本。現(xiàn)在的高速加工銑刀,大部分線路之間的鈦格 A1 - N 復(fù)合技術(shù),以多種方式處理,如果目前在非鐵金屬或合金材料干切削,金剛石(類金剛石)涂層刀具是非常關(guān)注的問題。預(yù)計該市場前景是非常重要的; 刀具夾緊系統(tǒng):刀具夾緊系統(tǒng),以支持高速切削是一項重要的技術(shù),目前使用最廣泛的是兩面工具夾緊系統(tǒng)。已正式投入市場作為一種商品在同一夾緊工具系統(tǒng)是:阿霍系統(tǒng)。在高速加工,工具和夾具旋轉(zhuǎn)性能的平衡,不僅影響精密加工和刀具壽命。它也將影響到生活的機床。因此,在選擇工具系統(tǒng),它應(yīng)該是一個平衡的選擇好的產(chǎn)品。工藝參數(shù),切削速度高速加工常規(guī)剪切速度的 10 倍左右。每齒刀進給速度基本保持不變,以保證零件的加工精度,表面質(zhì)量和耐用性的工具,飼料量也將相應(yīng)增加約 10 倍,達到 60 米/分鐘,有的甚至高達 120 米/ 民。因此,高速加工通常是排除使用高速,飼料和切削深度小切削參數(shù)。由于高速加工切割墊往往很小,形成非常薄的片光,熱切割把消失;如果使用新的布線熱穩(wěn)定性更好的工具,材料和涂料,使用干式切削加工過程中的高高速加工技術(shù)是一種理想的計劃。 高速加工領(lǐng)域的應(yīng)用,靈活高效的生產(chǎn)線,為了適應(yīng)需求的新車型,汽車車身模具和樹脂小組預(yù)防阻止成形模具。必須縮短生產(chǎn)周期,降低生產(chǎn)成本,因此,我們必須作出巨大努力,以促進生產(chǎn)高速芯片的過程中。上汽集團下屬公司:與過去相比,精加工,進一步精度;同時,表面粗糙度必須滿足的,彎曲的精確度,本應(yīng)受到適當?shù)拿芗娜斯ぬ幚怼S捎跇O高的切削速度,最后整理過程,處理周期應(yīng)大大減少。 發(fā)揮的加工中心和鏜銑類加工中心為代表的高速加工技術(shù)和自動換刀功能的區(qū)別可能改善加工效率,加工復(fù)雜零件用來集中盡可能布線過程中,這是一個固定在實現(xiàn)多個進程的集中處理和淡化傳統(tǒng)的車,銑,鏜,線切割加工不同的限制的技術(shù),設(shè)備和充分發(fā)揮高速切削工具的功能,目前正在提高數(shù)控機床效率和加快產(chǎn)品開發(fā)的一條有效途徑。因此,擬議的多用途工具的新的要求需要一個工具來完成不同地區(qū)的加工過程,空中交通管制的次數(shù)減少了,空管,以節(jié)省時間,減少數(shù)量和工具清單,和管理,以降低生產(chǎn)成本。較常用的一種多功能工具,銑削,鏜銑,鉆銑,鉆,銑螺紋范圍工具。與此同時,大規(guī)模的生產(chǎn)線,對技術(shù)的利用,需要制定專門的工具,工具或智能復(fù)合工具,提高加工效率和精度,并減少投資。在高速切削條件下,和一些特殊的工具,可以部分的時間來處理原始的 1 / 10 以下,結(jié)果是相當驚人的。 高速加工有很多優(yōu)點,如:大量的材料需要切除工件超細,超薄結(jié)構(gòu)的工件,傳統(tǒng)上,需要花費很長的時間處理移動工件和設(shè)計的快速變化,短期產(chǎn)品生命周期工件,能夠證明高速切削帶來的好處。