十一輥矯直機液壓系統(tǒng)設計
53頁 22000字數+論文說明書+任務書+3張CAD圖紙【詳情如下】
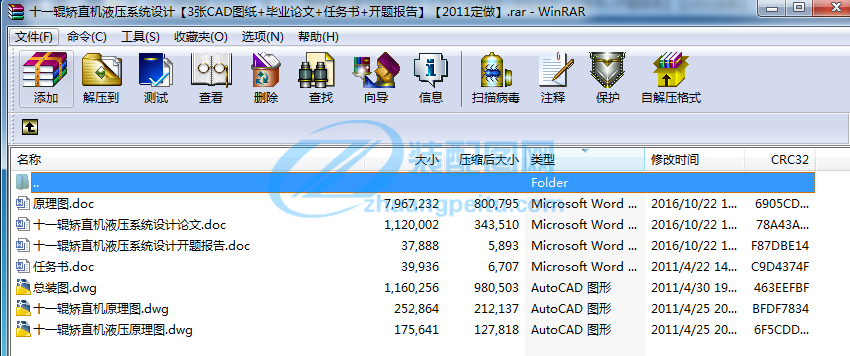
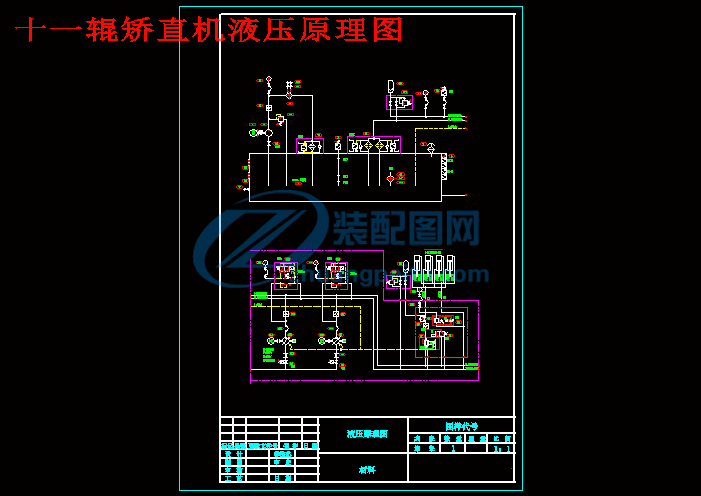
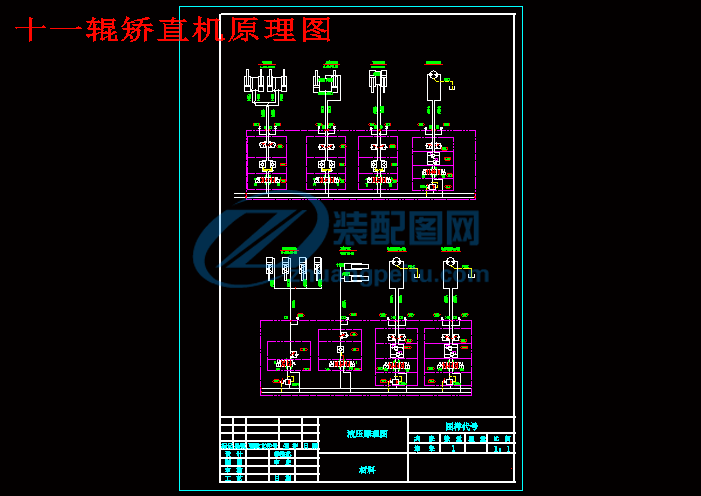
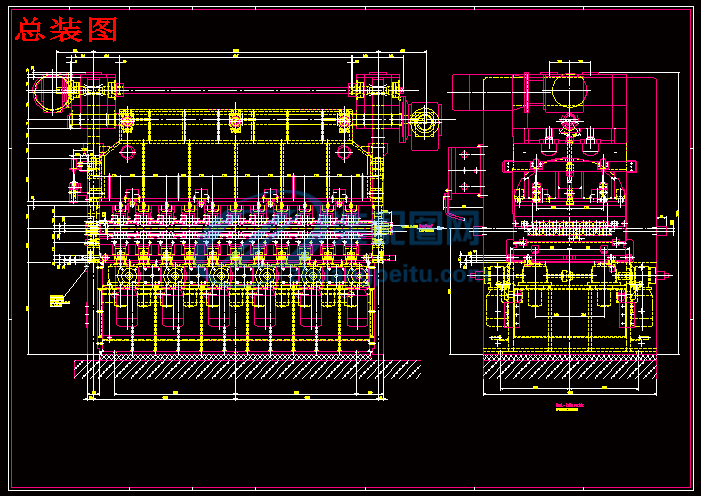
任務書.doc
十一輥矯直機原理圖.dwg
十一輥矯直機液壓原理圖.dwg
十一輥矯直機液壓系統(tǒng)設計開題報告.doc
十一輥矯直機液壓系統(tǒng)設計論文.doc
原理圖.doc
總裝圖.dwg
十一輥矯直機液壓系統(tǒng)設計
目 錄
第一章 前 言 1
1.1液壓機現狀概要 1
1.2 液壓傳動控制系統(tǒng)及設計要求 3
第二章 液壓機總體設計 4
2.1液壓機主要設計參數 4
2.2 液壓機工作原理分析 5
2.2.1 液壓機的基本組成 5
2.3 液壓機工藝方案設計 8
2.4 液壓機總體布局方案設計 8
總體布局如圖2.4所示 8
2.5 液壓機零部件設計 9
2.5.1.1 導柱設計 9
2.5.1.2 橫梁設計 10
第三章 液壓機液壓系統(tǒng)設計 13
3.1 液壓傳動的優(yōu)越性概述 13
3.2 液壓系統(tǒng)設計要求 13
3.3 液壓系統(tǒng)設計 14
3.4 液壓系統(tǒng)零部件設計 30
3.5 液壓站布局設計 38
3.6 液壓系統(tǒng)安全、穩(wěn)定性驗算 39
第四章 液壓機電氣系統(tǒng)設計 44
4.1 電氣控制概述 44
4.2 液壓機電氣控制方案設計 44
4.3 液壓機電氣控制電路設計 44
第五章 液壓機安裝調試和維護 48
5.1 液壓機的安裝 48
5.2 液壓機的調試 48
5.3 液壓機的保養(yǎng)維護 48
結 論 50
參考文獻 51
致 謝 52
第一章 前 言
1.1液壓機現狀概要
長期以來,矯直機因彎曲由人工檢測,壓彎量人為設定不夠準確,全過程都靠手工操作,效率低,矯直精度全憑操作者經驗來決定等缺點,一直作為一種補充矯直設備來使用。所以矯直必須檢測工件的原始彎曲,測量彎曲量、確定最佳矯直點、設定壓彎量。由于缺少可靠的檢測手段和認識上的一些人為因素,以前這些工作只能靠人工來完成。因此以前的矯直機有以下缺點:彎曲人工檢測、壓彎量人工設定不夠準確,效率低,矯直精度全憑操作者經驗來決定,降低了生產效率。而且現在人們對棒材的需求量越來越大、對其精度要求也越來越高,在情況下斜二輥矯直機的問世解決了以前平行輥矯直機所解決不了的棒材、管材的矯直精度問題,在這種情況下,我們對矯直機進行設計。
液壓傳動技術發(fā)展到今天已經有了較為完善、成熟的理論和實踐基礎。液壓傳動技術與傳統(tǒng)的機械傳動相比,操作方便簡單,調速范圍廣,很容易實現直線運動并且還具有自動過載保護功能。液壓傳動容易實現自動化操作,采用電液聯(lián)合控制后,可以實現更高程度的自動控制以及遠程遙控。由于液壓傳動的工作介質是流體礦物油,有較大的沿程和局部阻力損失。當系統(tǒng)的工作壓力比較高時,還會產生比較大的泄漏,泄漏的礦物油將直接對環(huán)境造成污染,有時候還容易引起安全事故。油液受溫度的影響很大,因此液壓油不能在很高或很低的溫度條件下工作。由于液壓油的可壓縮性和泄漏,液壓傳動不能保證恒定的傳動比和很高的傳動精度,這是液壓傳動的最大不足之處。此外,液壓傳動的故障排除不如機械傳動、電氣傳動那樣容易,因而對使用和維護人員有較高的技術水平要求。雖然液壓傳動存在這些缺陷,但總體上優(yōu)點還是蓋過了缺點,因而應用還是很廣泛。
液壓機自19世紀問世以來得到了很快的發(fā)展,在工業(yè)生產中已經有了廣泛的應用,成了產品壓力加工成型不可或缺的機械設備。隨著科學技術的日新月異,電子技術、液壓技術的不斷成熟,液壓機也得到了更進一步的發(fā)展。到目前為止,液壓機的最大公稱壓力已經達到了750MN,控制技術也由原來傳統(tǒng)的繼電器控制變?yōu)榭删幊炭刂破骱凸I(yè)計算機控制,這使液壓機的運行平穩(wěn)性、控制精度、產品質量有了保證,同時生產效率得到了很大的提高。
液壓機加工與傳統(tǒng)機械加工相比屬于無屑加工,應用范圍廣泛,一般用于塑性材料的冷擠、校直、彎曲、沖裁、拉伸等。此外液壓機還用于粉末冶金、翻邊、壓裝等產品的成型加工工藝。液壓機還能實現復雜工件和不對稱工件的加工,產品廢品率較低。液壓機根據加工工件的不同性質,還可進行適當的壓力行程調整,滿足產品的加工要求。液壓機主要由主機、液壓系統(tǒng)、電氣系統(tǒng)三部分組成。液壓機的整個工作過程的實現,首先是由電氣系統(tǒng)來控制液壓系統(tǒng),然后再由液壓系統(tǒng)控制主機主缸和頂出缸的順序動作??偟膩碚f,液壓機操作簡單,維護方便。
雖然液壓機目前應用十分廣泛,但是潛在的問題還很多。液壓機屬于高壓工作設備,進行壓力加工時,隨著壓力的不斷升高泄漏也會不斷增大,這樣不利于保證零件的加工精度,同時還會對環(huán)境造成污染。除此之外,液壓機還存在如下缺陷,液壓機壓力加工完成后,卸壓時存在很大的液壓沖擊,這樣對液壓元件及其它設備損害很大;按下啟動按鈕后,動作靈敏性不及電氣控制;液壓機出現故障不能夠正常工作,故障不容易及時找到并排除,給維護帶來了一定的技術難題和不便;液壓機工作時產生的液壓沖擊、氣蝕等現象,會縮短液壓元件的使用壽命。
為了催生更大的生產力,液壓機的設計需要改進。液壓油路設計、控制系統(tǒng)的優(yōu)化設計將是液壓機今后值得研究的方向。
(1)油路設計方面
為了防止泄油和外界的污染,液壓機油路的設計趨于集成化、封閉循環(huán)式,這樣可以延長設備的使用壽命。除此之外,液壓元件設計盡量標準化,集成化。集成液壓系統(tǒng)減少了管路連接,可以降低泄漏和污染。液壓元件的標準化給維護帶來了方便。
(2)控制系統(tǒng)方面
液壓機屬于高壓設備,控制系統(tǒng)除控制設備安全可靠的工作之外,還應該讓控制精度變得更高,人機交互變得更簡單,操作更方便,自動化、高速化、智能化程度更好。
綜上所述,液壓機的發(fā)展促進了生產力的發(fā)展。伴隨著電氣控制技術、液壓傳動技術的不斷發(fā)展,液壓機的自動化程度、加工精度將進一步得到提高,實現智能化控制。
1.2 液壓傳動控制系統(tǒng)及設計要求
液壓傳動控制是工業(yè)中經常用到的一種控制方式,它采用液壓完成傳遞能量的過程(見圖1-1)。因為液壓傳動控制方式的靈活性和便捷性,液壓控制在工業(yè)上受到廣泛的重視。液壓傳動是研究以有壓流體為能源介質,來實現各種機械和自動控制的學科。液壓傳動利用這種元件來組成所需要的各種控制回路,再由若干回路有機組合成為完成一定控制功能的傳動系統(tǒng)來完成能量的傳遞、轉換和控制。
第二章 液壓機總體設計
2.1液壓機主要設計參數
(1)鋼輥平衡缸:
最大負載: 450KN; 移動速度:60mm/s
(2)上箱體鎖緊缸:
使用柱塞缸:最大負載: 20KN; 移動速度:50mm/s
(3)橫梁預彎缸:
最大負載: 1400KN; 移動速度:60mm/s
(4).換輥提升缸:
最大負載: 180KN; 移動速度:70mm/s
(5)邊輥升降馬達:
轉速330r/min, 最大扭矩:5000NM
(2)液壓機的主要功能
通過液壓傳動系統(tǒng)傳遞動力,完成零件的壓力成型加工。
(3)液壓機的適用范圍
液壓機主要用于冷擠、校直、彎曲、沖裁、拉伸、粉末冶金、翻邊、壓裝等成型工藝。
2.2 液壓機工作原理分析
2.2.1 液壓機的基本組成
液壓機是由兩個大小不同的液缸組成的,在液缸里充滿水或油。充水的叫“水壓機”;充油的稱“油壓機”。兩個液缸里各有一個可以滑動的活塞,如果在小活塞上加一定值的壓力,根據帕斯卡定律,小活塞將這一壓力通過液體的壓強傳遞給大活塞,將大活塞頂上去。
設小活塞的橫截面積是S1,加在小活塞上的向下的壓力是F1。于是,小活塞對能夠大小不變地被液體向各個方向傳遞。大活塞所受到的壓強必然也等于P。
若大活塞的橫截面積是S2,壓強P在大活塞上所產生的向上的壓力截面積是小活塞橫截面積的倍數。
從上式知,在小活塞上加一較小的力,則在大活塞上會得到很大的力,為此用液壓機來壓制膠合板、榨油、提取重物、鍛壓鋼材等。
液壓機主要由主機、液壓控制系統(tǒng)、電氣控制系統(tǒng)三部分組成。 其中主機包括工作臺、導柱、滑塊、上缸、頂出缸等結構;液壓系統(tǒng)由控制元件、執(zhí)行元件、輔助元件、動力裝置、工作介質等組成;電氣控制控制系統(tǒng)主要由繼電器、接觸器、按鈕、行程開關、電器控制柜等組成。
結 論
本文重點對液壓機的液壓控制回路、液壓元件及安全保護措施等進行了方案設計。經多方案對比之后,本文液壓系統(tǒng)采用插裝閥集成控制系統(tǒng)。該液壓控制系統(tǒng)解決了普通閥系統(tǒng)密封性差、通流量小、壓力損失大等問題。為了讓系統(tǒng)的工作壓力隨負載的變化而自動調節(jié),液壓泵選用恒功率變量柱塞泵。為解決液壓沖擊對設備安全的影響,系統(tǒng)中設置泄壓回路。通過泄壓來降低系統(tǒng)的壓力,防止產生液壓沖擊;設置保壓回路讓工件有足夠的成型時間,保證產品的質量。速度換接通過行程開關來控制,這種換接方式,控制比較可靠,設備安裝方便,價格也實惠。通過流量計算發(fā)現主缸快進時會出現供油不足的情況,為了解決這一問題,在液壓系統(tǒng)中設置補油油箱。整體的方案確定后,對液壓系統(tǒng)的可行性進行校驗,該液壓系統(tǒng)可以滿足液壓機的加工工藝要求。此外,還對主機、電氣控制系統(tǒng)進行了簡明的總體設計。
液壓機在進行方案設計時,有些方案的選擇可能不是最佳??傮w來說,本文的總體設計方案可以滿足液壓機的加工工藝要求。
參考文獻
[1] 楊培元,朱福元.液壓系統(tǒng)設計簡明手冊.[M]北京:機械工業(yè)出版社,1999,1-191.
[2] 吳宗澤,羅圣國.機械設計課程設計手冊.第二版.北京:高等教育出版社,1999,1-260.
[3] 汪愷.機械設計標準應用手冊.第2卷. [M]北京:機械工業(yè)出版社,1997,213-226.
[4] 汪愷.機械設計標準應用手冊.第3卷. [M]北京:機械工業(yè)出版社,1996,22-3-22-182
[5] 毛謙德,李振清.機械設計師手冊.第二版 北京:機械工業(yè)出版社,2000.12
[6] JB3915-85.液壓機安全技術條件.北京:中華人民共和國機械工業(yè)部,1985~02~08發(fā)布
[7] GB9166-88.液壓機精度.北京:國家標準局,1988~05~05發(fā)布
[8] 成大先主編.機械設計手冊 單行本 機械傳動. [M]北京:化學工業(yè)出版社,2004
[9] 成大先.機械設計手冊 單行本 常用設計資料. [M]北京:化學工業(yè)出版社,2004
[10] 成大先.機械設計手冊 單行本 聯(lián)接與緊固. [M]北京:化學工業(yè)出版社,2004
[11] 李愛華.工程制圖基礎 北京:高等教育出版社,2003.8
[12] 王建中,李洪.公差與制圖手冊 沈陽:遼寧科學技術出版社,1999.1
[13] 王運炎,葉尚川.機械工程材料 第二版 北京:機械工業(yè)出版社1998
[14] 濮良貴,紀名剛.機械設計 第七版 北京:高等教育出版社,2001
[15] 許福玲,陳堯明.液壓傳動與氣壓傳動.第二版.北京:機械工業(yè)出版社,2004,1-290.
[16] 章宏甲,黃宜,王積偉.液壓傳動與氣壓傳動.北京:機械工業(yè)出版社,2000,1-356.
[17] 劉鴻文.材料力學(Ⅰ).第四版.北京:高等教育出版社,2004,1-366.
[18] 高安邦,張海根.機電傳動控制.北京:高等教育出版社,2001,1-215.
[19] 陳立定,吳玉香,蘇開才.電氣控制與可編程控制器.廣州:華南理工大學出版社,2001,5-148.
[20] 陳立定,吳玉香,蘇開才.電氣控制與可編程控制器.廣州:華南理工大學出版社,2001,5-148.
[21] 陳遠齡、黎亞元、傅國強.機床電氣的自動控制 重慶大學出版社
[22] 秦曾煌.電工學,北京:高等教育出版社,2003.2
[23] 李發(fā)海、王巖.電機與拖動基礎.第二版.北京:清華大學出版社.1994
[24] 趙程、楊建民.機械工程材料,北京:機械工業(yè)出版社 2003.1
[25] 王伯平.互換性與測量技術基礎,北京:機械工業(yè)出版社 2000.2
[26] 朱理.機械原理,北京:高等教育出版社,2004.4
[27] 李愛華等.工程制圖基礎 北京:高等教育出版社,2003.8
[28] 李建興.可編程序控制器應用技術. 北京:機械工業(yè)出版社 2004.7
致 謝
經過幾個月的努力,畢業(yè)設計已經接近尾聲。由于實踐經驗的匱乏,本次設計難免有考慮不周的地方。如果沒有教授的悉心指導以及本組人員的支持,恐怕設計不會這樣順利完成。自開題以來,設計的每個環(huán)節(jié)羅老師都認真指導,從資料的查閱到具體方案的修改,老師都提出了寶貴的建議,讓我受益匪淺。除此之外,老師科學嚴謹的治學態(tài)度和淵博的知識更是我永遠學習的榜樣。在此對羅教授及本組的同學表示衷心的感謝!最后還要感謝曾教導過和給我?guī)椭睦蠋?!是你們曾經辛勤的付出才有了我今天知識的積累。
1 十一輥矯直機液壓系統(tǒng)設計 目 錄 第一章 前 言 ............................................................................................................................... 2 壓機現狀概要 ................................................................................................................. 2 液壓傳動控制系統(tǒng)及設計要求 .............................................................................................. 3 第二章 液壓機總體設計 ............................................................................................................... 4 壓機主要設計參數 ......................................................................................................... 4 壓機工作原理分析 ........................................................................................................ 5 壓機的基本組成 ......................................................................................................... 5 壓機工藝方案設計 ........................................................................................................ 8 壓機總體布局方案設計 ................................................................................................ 9 總體布局如圖 示 ........................................................................................................... 9 壓機零部件設計 ............................................................................................................ 9 柱設計 ......................................................................................................... 10 梁設計 ......................................................................................................... 11 第三章 液壓機液壓系統(tǒng)設計 ..................................................................................................... 14 壓傳動的優(yōu)越 性概述 .................................................................................................. 14 壓系統(tǒng)設計要求 .......................................................................................................... 14 壓系統(tǒng)設計 .................................................................................................................. 15 壓系統(tǒng)零部件設計 ...................................................................................................... 31 壓 站布局設計 .............................................................................................................. 39 壓系統(tǒng)安全、穩(wěn)定性驗算 .......................................................................................... 40 第四章 液壓機電氣系統(tǒng)設計 ..................................................................................................... 45 氣控制概述 .................................................................................................................. 45 壓機電氣控制方案設計 .............................................................................................. 45 壓機電氣控制電路設計 .............................................................................................. 45 第五章 液壓機安裝調試和維護 ................................................................................................. 49 壓機的安裝 .................................................................................................................. 49 壓機的調試 .................................................................................................................. 49 壓機的保養(yǎng)維護 .......................................................................................................... 49 結 論 ............................................................................................................................................. 51 參考文獻 ......................................................................................................................................... 52 致 謝 ............................................................................................................................................. 53 2 第一章 前 言 壓機現狀概要 長期以來,矯直機因彎曲由人工檢測,壓彎量人為設定不夠準確,全過程都靠手工操作,效率低,矯直精度全憑操作者經驗來決定等缺點,一直作為一種補充矯直設備來使用。所以矯直必須檢測工件的原始彎曲,測量彎曲量、確定最佳矯直點、設定壓彎量。由于缺少可靠的檢測手段和認識上的一些人為因素,以前這些工作只能靠人工來完成。因此以前的矯直機有以下缺點:彎曲人工檢測、壓彎量人工設定不夠準確,效率低,矯直精度全憑操作者經驗來決定,降低了 生產效率。而且現在人們對棒材的需求量越來越大、對其精度要求也越來越高,在情況下斜二輥矯直機的問世解決了以前平行輥矯直機所解決不了的棒材、管材的矯直精度問題,在這種情況下,我們對 矯直機進行設計。 液壓傳動技術發(fā)展到今天已經有了較為完善、成熟的理論和實踐基礎。液壓傳動技術與傳統(tǒng)的機械傳動相比,操作方便簡單,調速范圍廣,很容易實現直線運動并且還具有自動過載保護功能。液壓傳動容易實現自動化操作,采用電液聯(lián)合控制后,可以實現更高程度的自動控制以及遠程遙控。由于液壓傳動的工作介質是流體礦物油,有較大的沿程和局部阻力損失 。當系統(tǒng)的工作壓力比較高時,還會產生比較大的泄漏,泄漏的礦物油將直接對環(huán)境造成污染,有時候還容易引起安全事故。油液受溫度的影響很大,因此液壓油不能在很高或很低的溫度條件下工作。由于液壓油的可壓縮性和泄漏,液壓傳動不能保證恒定的傳動比和很高的傳動精度,這是液壓傳動的最大不足之處。此外,液壓傳動的故障排除不如機械傳動、電氣傳動那樣容易,因而對使用和維護人員有較高的技術水平要求。雖然液壓傳動存在這些缺陷,但總體上優(yōu)點還是蓋過了缺點,因而應用還是很廣泛。 液壓機自 19 世紀問世以來得到了很快的發(fā)展,在工業(yè)生產中已經有 了廣泛的應用,成了產品壓力加工成型不可或缺的機械設備。隨著科學技術的日新月異,電子技術、液壓技術的不斷成熟,液壓機也得到了更進一步的發(fā)展。到目前為止,液壓機的最大公稱壓力已經達到了 750制技術也由原來傳統(tǒng)的繼電器控制變?yōu)榭删幊炭刂破骱凸I(yè)計算機控制,這使液壓機的運行平穩(wěn)性、控制精度、產品質量有了保證,同時生產效率得到了很大的提高。 液壓機加工與傳統(tǒng)機械加工相比屬于無屑加工,應用范圍廣泛,一般用于塑性材料的冷擠、校直、彎曲、沖裁、拉伸等。此外液壓機還用于粉末冶金、翻邊、壓裝等產品的成型加工工藝。液壓機 還能實現復雜工件和不對稱工件的加工,產 3 品廢品率較低。液壓機根據加工工件的不同性質,還可進行適當的壓力行程調整,滿足產品的加工要求。液壓機主要由主機、液壓系統(tǒng)、電氣系統(tǒng)三部分組成。液壓機的整個工作過程的實現,首先是由電氣系統(tǒng)來控制液壓系統(tǒng),然后再由液壓系統(tǒng)控制主機主缸和頂出缸的順序動作。總的來說,液壓機操作簡單,維護方便。 雖然液壓機目前應用十分廣泛,但是潛在的問題還很多。 液壓機屬于高壓工作設備 ,進行壓力加工時 ,隨著壓力的不斷升高泄漏也會不斷增大 ,這樣不利于保證零件的加工精度,同時還會對環(huán)境造成污染。除此之外 ,液壓機還存在如下缺陷,液壓機壓力加工完成后,卸壓時存在很大的液壓沖擊,這樣對液壓元件及其它設備損害很大;按下啟動按鈕后,動作靈敏性不及電氣控制;液壓機出現故障不能夠正常工作,故障不容易及時找到并排除,給維護帶來了一定的技術難題和不便;液壓機工作時產生的液壓沖擊、氣蝕等現象,會縮短液壓元件的使用壽命。 為了催生更大的生產力,液壓機的設計需要改進。液壓油路設計、控制系統(tǒng)的優(yōu)化設計將是液壓機今后值得研究的方向。 ( 1)油路設計方面 為了防止泄油和外界的污染,液壓機油路的設計趨于集成化、封閉循環(huán)式,這樣可以延長設 備的使用壽命。除此之外,液壓元件設計盡量標準化,集成化。集成液壓系統(tǒng)減少了管路連接,可以降低泄漏和污染。液壓元件的標準化給維護帶來了方便。 ( 2)控制系統(tǒng)方面 液壓機屬于高壓設備,控制系統(tǒng)除控制設備安全可靠的工作之外,還應該讓控制精度變得更高,人機交互變得更簡單,操作更方便,自動化、高速化、智能化程度更好。 綜上所述,液壓機的發(fā)展促進了生產力的發(fā)展。伴隨著電氣控制技術、液壓傳動技術的不斷發(fā)展,液壓機的自動化程度、加工精度將進一步得到提高,實現智能化控制。 液壓傳動控制系統(tǒng)及設計要求 液壓傳動控 制是工業(yè)中經常用到的一種控制方式,它采用液壓完成傳遞能量的過程(見圖 1因為液壓傳動控制方式的靈活性和便捷性,液壓控制在工業(yè)上受到廣泛的重視。液壓傳動是研究以有壓流體為能源介質,來實現各種機械和自動控制的學科。液壓傳動利用這種元件來組成所需要的各種控制回路,再由若干回路有機組合成為完成一定控制功能的傳動系統(tǒng)來完成能量的傳遞、轉換和控制。 4 圖 1壓傳動能量傳動過程 ( 1)液壓機總體方案設計,其中包括主機的結構設計和工藝設計、零部件的結構設計和工藝設計、部件裝配方案設計; ( 2)通過液壓系統(tǒng)總體設計方案的對比,確定合理的液壓系統(tǒng)設計方案。主要包括液壓系統(tǒng)原理圖設計、液壓元件結構、工藝設計、液壓站總體布局設計; ( 3)電氣控制系統(tǒng)設計,包括主電路和控制電路電路圖設計; ( 4)設計方案確定時,必須考慮選用什么樣的制造材料,達到什么樣的表面加工質量,采用什么樣的機械加工設備,選擇什么樣的熱處理方式等; ( 5)整個設備滿足拆裝方便,運輸方便的要求; ( 6)液壓機能夠準確完成如下工作循環(huán):主缸活塞滑塊快速下行、主缸活塞滑塊慢速加壓、主缸保壓、主 缸卸壓、主缸活塞滑塊回程、頂出缸頂出、頂出缸退回等; ( 7)設備達到總體布局合理,結構緊湊、工作穩(wěn)定可靠、操作簡單、維護方便、環(huán)境污染小、工作的時候噪音低、自動化程度高等,能夠完成沖壓、冷擠、校直、彎曲、粉末冶金壓制成型、薄板拉伸、壓裝成型等加工工藝。 第二章 液壓機總體設計 壓機主要設計參數 ( 1)鋼輥平衡缸: 最大負載 : 450 移動速度: 60mm/s ( 2)上箱體鎖緊缸 : 使用柱塞缸 :最大負載 : 20移動速度: 50mm/s ( 3)橫梁預彎缸: 最大負載 : 1400移動速度: 60mm/s ( 4) 最大負載 : 180移動速度: 70mm/s 動力元件 液壓能 控制回路 執(zhí)行元件 機械能 機械能等 5 ( 5)邊輥升降馬達: 轉速 330r/最大扭矩: 5000 2)液壓機的主要功能 通過液壓傳動系統(tǒng)傳遞動力,完成零件的壓力成型加工。 ( 3)液壓機的適用范圍 液壓機主要用于冷擠、校直、彎曲、沖裁、拉伸、粉末冶金、翻邊、壓裝等成型工藝。 壓機工作原理分析 壓機的基本組成 液壓機是由兩個大小不同的液缸組成的,在液缸里充滿水或油。充水的叫“水壓機”;充油的稱“油壓機”。兩 個液缸里各有一個可以滑動的活塞,如果在小活塞上加一定值的壓力,根據帕斯卡定律,小活塞將這一壓力通過液體的壓強傳遞給大活塞,將大活塞頂上去。 設小活塞的橫截面積是 在小活塞上的向下的壓力是 是,小活塞對能夠大小不變地被液體向各個方向傳遞。大活塞所受到的壓強必然也等于P。 若大活塞的橫截面積是 強 P 在大活塞上所產生的向上的壓力截面積是小活塞橫截面積的倍數。 從上式知,在小活塞上加一較小的力,則在大活塞上會得到很大的力,為此用液壓機來壓制膠合板、榨油、提取重物、鍛壓鋼材等。 液壓機主要由主機、液 壓控制系統(tǒng)、電氣控制系統(tǒng)三部分組成。 其中主機包括工作臺、導柱、滑塊、上缸、頂出缸等結構;液壓系統(tǒng)由控制元件、執(zhí)行元件、輔助元件、動力裝置、工作介質等組成;電氣控制控制系統(tǒng)主要由繼電器、接觸器、按鈕、行程開關、電器控制柜等組成。 6 壓機的工作原理 ( 1)液壓機主機組成簡圖 2 3 4 5 6 7 8 7 圖 液壓機主機組成簡圖 ( 2) 液壓機工作原理分析 液壓機的動作順序通過電氣系統(tǒng)、液壓系統(tǒng)控制,控制順序框圖如圖 啟 動電氣系統(tǒng) 液壓系統(tǒng) 液壓機主機行程開關手 動圖 液壓機控制順序圖 從上面的控制順序框圖可以看出,液壓機的工作原理由電氣控制系統(tǒng)控制液壓系統(tǒng),液壓控制系統(tǒng)再控制主機工作,主機動作觸及行程開關,將信號反饋給電氣控制系統(tǒng),實現循環(huán)控制。 ( 3) 液壓機工作循環(huán)分析 液壓機工作循環(huán)如圖 8 滑塊快速下行 工進、加壓 保壓頂出快速回程 停止圖 液壓機工 作循環(huán)圖 液壓機工作循環(huán)如圖 a) ,滑塊在自重的作用下快速下行,碰到行程開關后由快進變?yōu)楣みM,隨后進行加壓、保壓。保壓時間完成后,滑塊快速回程,直到回到原來的位置,停止運動;圖 b) 表示頂出缸的工作循環(huán)過程,主缸快進、工進、保壓、退回停止后,頂出缸才運動,將工件頂出。 壓機工藝方案設計 ( 1)控制方式的選擇 采用液壓系統(tǒng)與電氣系統(tǒng)相結合的控制方式。具有調整、手動、半自動三種工作方式,可實現定壓、定程兩種加工工藝; ( 2)液壓系統(tǒng): 液壓油路采用封閉式回路,供油方式選用變量泵供油,液壓 控制元件采用插裝閥形式。針對液壓機快進時供油不足以及工進時的高壓特性,系統(tǒng)應設有補油和卸壓裝置; ( 3)電氣控制: 采用繼電器、行程開關、接觸器、手動按鈕等元件進行手動、半自動控制; ( 4)主機: 主機結構形式采用“三梁四柱”的形式,主缸和頂出缸為執(zhí)行元件。 9 壓機總體布局方案設計 總體布局如圖 示 1 2 34 5 6 7圖 液壓機總體布局簡 圖 圖 為三個部分,即:主機、液壓系統(tǒng)、電氣控制系統(tǒng)。液壓系統(tǒng)的所有部件都集中安裝在液壓油箱上,使液壓站布局結構變得緊湊。電氣控制元件集中設計在電氣柜中。啟動、停止、快進、頂出、調整、等控制按鈕設置在控制臺上,方便及時操作。 壓機零部件設計 機載荷分析 鋼板在軋制過程中要矯直鋼板及控制板厚,矯直機由主機及輔機組成,主機液壓系統(tǒng) 由伺服系統(tǒng)控制,矯直機輔機所設計的液壓系統(tǒng)由 4個鋼輥平衡缸、 8 個上箱體鎖緊缸、 1 個活動橫梁預彎缸、 4 個換輥提升缸及邊輥升降馬達組成。 2、鋼輥平衡缸用來給輔助控制鋼輥的位置(鋼輥的位置由伺服系統(tǒng)控制),使鋼輥在軋制時 始終受到向上的作用力,用來平衡鋼輥的重力。 10 3、上箱體鎖緊缸在軋制過程中鎖緊上箱體;活動橫梁預彎缸用來在調整輥子時預彎橫梁; 換輥提升缸在換輥時提升鋼輥,以便換輥;邊輥升降馬達用來調整鋼輥的位置。 導柱受拉,受力如圖 橫梁導柱 圖 橫梁、導柱受力圖 柱設計 材料選擇:導柱在工作過程中主要承受拉力,材料 必須具備較高的抗拉強度。導柱材料選擇 45 圓鋼,也可選用鍛件形式。 熱處理要求:導柱除了承受拉力之外,外圓柱表面與滑塊之間還存在摩擦力。為了減少導柱表面的磨損,通過表面熱處理提高表面硬度增加表面耐摩性??偟臒崽幚砉に嚍檎{質和表面淬火。 理論設計計算: 液壓機的最大負載約為 100T,通過力傳遞后,最后由四根導柱承受 100T 的拉力,作用在每根導柱上的拉力為 25T。由許用拉應力公式 (可計算導柱的安全直徑 D。 [?(式中: ][? — 許用應力;取 45 鋼 ][? =80~ 100 F— 軸向拉力; A— 橫截面積。 即: 11 4 66 ??? ???? ?? 圓整后取導柱直徑 D=90了防止四根導柱因瞬間的受力不均而被破壞,導柱直徑可適當加大,取 D=110 梁設計 材料選擇:橫梁工作時的受力為彎曲力,材料應具有一定的抗彎強度。選用45 鋼,毛坯采用鍛件。 熱處理要求:橫梁進行調質處理。 理論計算校核: 橫梁受力可以簡化為簡直梁 ,中間受載的情形,如圖 示。 截 面 1 - 1圖 橫梁滑塊受力簡圖 初步確定橫梁的長、寬、高尺寸分別為 1310、 1045、 575面為矩形。即:在負載作用下的剪力和彎矩如圖 示。 12 圖 (a) 剪力圖 (b) 彎矩圖 由彎矩圖 2.7(b)可知,橫梁 C 點 1— 1 截面彎矩最大,該截面是危險截面。為了 保證橫梁能夠正常工作,必須對該截面進行強度校核。正應力計算公式為: WM ?(式中: 最大彎曲正應力; 最大彎矩; W — 抗彎截面系數 ( 3m )。 矩形截面抗彎系數 W 計算公式為: 62 (式中: b — 矩形截面的寬; h — 矩形截面的高。 即: 32 0 5 7 5.1 ?? M P am 47 5 3m a x ??? 45 鋼的彎曲許用應力 [? ]=100橫梁的最大彎曲應力小于材料的許用應力,經過校核,設計尺寸滿足要求 。 13 機工作臺設計 液壓機工作臺主要受壓,由于工作臺不是很高,剛度要求可以滿足,因此在設計計算時只要進行抗壓強度的校核即可,校核過程從略。 材料選擇:工作臺主要受壓,材料選用鑄鋼 45。 工藝要求: 機械加工時,工作臺表面做成 T 形槽,如圖 示。 圖 工作臺 T 形槽 制臺設計 材料選擇:控制臺主要用于安裝控制按鈕,不承受動載荷,強度要求不是很高,滿足使用要求即可,材料選用 加工工藝:控制臺的制作加工 采用焊接方式完成。 外形設計:控制臺外形尺寸設計應考慮操作方便。外形簡圖如圖 示。 1 2 3圖 液壓機控制臺外形簡圖 14 第三章 液壓機液壓系統(tǒng)設計 壓傳動的優(yōu)越性概述 科學技術迅猛發(fā)展的今天,液壓傳動技術隨之有了比較完善、成熟的理論基礎。目前液壓傳動技術正向著 高壓、高速、大功率、高效、低噪音、經久耐用、高度集成化的方向發(fā)展。 ( 1)液壓傳 動優(yōu)越性 1)液壓元件布局靈活; 2)液壓傳動操作控制方便,可實現無級調速; 3)液壓傳動容易實現直線傳動,可以進行自動過載保護; 4)液壓傳動采用電液控制相結合的控制方式,可實現自動化控制,還可實現遠程控制; 5)液壓系統(tǒng)中液壓元件的磨損比機械傳動小很多,液壓油除了作為傳動介質外還起到了潤滑的作用,延長了液壓系統(tǒng)中液壓元件的使用壽命。 ( 2)液壓傳動不足 1)液壓傳動沿程、局部阻力損失比較大; 2)液壓傳動壓力高時泄漏較大,效率降低,處理不好油液還會對環(huán)境構成污染; 3)液壓介質的泄漏和可壓縮性使系統(tǒng)沒有 嚴格的傳動比; 4)液壓傳動存在的液壓沖擊、氣蝕、困油現象影響了設備的安全工作和使用壽命; 5)液壓元件制造精度高,成本貴,系統(tǒng)故障不容易排除,維護技術成本高; 6)液壓系統(tǒng)工作環(huán)境受溫度影響較大,不宜在很高和很低的溫度條件下工作。 壓系統(tǒng)設計要求 壓機負載確定 參考液壓機技術參數表 知,液壓機的最大工作負載為 100T, 工進時液體最大壓力為 26此確定液壓機設計負載為 100T 型液壓機。 15 壓機主機工藝過程分析 壓制工件時主機的工藝過程:按下啟動按鈕后,主缸 上腔進油,橫梁滑塊在自重作用下快速下行,此時會出現供油不足的情況,補油箱對上缸進行補油。觸擊快進轉為工進的行程開關后,橫梁滑塊工進,并對工件逐漸加壓。工件壓制完成后進入保壓階段,讓產品穩(wěn)定成型。保壓結束后,轉為主缸下腔進油,滑塊快速回程,直到原位后停止。橫梁滑塊停止運動后,頂出缸下腔進油,將工件頂出,工件頂出后,頂出缸上腔進油,快速退回。 壓系統(tǒng)設計參數 液壓系統(tǒng)設計參數可參考表 系統(tǒng)壓力: 26② 上液壓缸、下液壓缸推力均為 100t。 ③ 上缸快進、快退速度速度 s,。 ④ 上液壓缸行程均為 460 ㎝;下液壓缸行程均為 50 ㎝。 ⑤ 上缸快進行程 300㎝; ⑥ 保壓時間 2s ⑦ 上缸工進速度 s. 壓系統(tǒng)設計 壓機主缸工況分析 缸速度循環(huán)圖 根據液壓機系統(tǒng)設計參數及表 主缸滑塊行程為 460以得到主缸的速度循環(huán)圖如下: 16 圖 主缸速度循環(huán)圖 缸負載分析 液壓機啟動時,主缸上腔充油主缸快速下行,慣性負載隨之產生。此外,還存在靜摩 擦力、動摩擦力負載。由于滑塊不是正壓在導柱上,不會產生正壓力,因而滑塊在運動過程中所產生的摩擦力會遠遠小于工作負載,計算最大負載時可以忽略不計。液壓機的最大負載為工進時的工作負載。通過各工礦的負載分析,液壓機主缸所受外負載包括工作負載、慣性負載、摩擦阻力負載,即: F = ( 式中: F — 液壓缸所受外負載; 工作負載; 滑塊與導柱、活塞與缸筒之間的摩擦阻力負載,啟動時為靜摩擦阻力負載,啟動后為動摩擦力負載; 運 動執(zhí)行部件速度變化時的慣性負載。 ( 1)慣性負載 算 計算公式: ??( 式中: G — 運動部件重量; g — 重力加速度 2S ; v? — t? 時間內的速度變化量; t? — 加速或減速時間,一般情況取 t? = 查閱相同型號的液壓機資料,初步估算橫梁滑塊的重量為 30液壓機所給設計參數可及: v? =s ,取 t? =入公式 即: s 0 00 2 ?= 4898N ( 2)摩擦負載 算 滑塊啟動時產生靜摩擦負載,啟動過后產生動摩擦負載。通過所有作用在主缸上的負載可以看出,工作負載遠大于其它形式的負載。由于滑塊與導柱 、活塞與缸體之間的摩擦力不是很大,因而在計算主缸最大負載時摩擦負載先忽略不計。 17 ( 3)主缸負載 F 計算 將上述參數 4898N 、 2000000 即: F = 2000000 + 4898 = 2004898N 缸負載循環(huán)圖 ( 1)主缸工作循環(huán)各階段外負載如表 主缸工作循環(huán)負載 工 作 循 環(huán) 外 負 載 啟 動 F = f 靜 + 5 梁滑塊快速下行 F = f 動 忽略不計 工 進 F = f 動 + 2000 速回程 F = f 回 + F 背 ≈ 400 :“ f 靜 ”表示啟動時的靜摩擦力,“ f 動 ”表示啟動后的動摩擦力。 ( 2)主缸各階段負載循環(huán)如圖 主缸負載循環(huán)圖 18 壓機頂出缸工況分析 出缸速度循環(huán)圖 根據液壓機系統(tǒng)設計參數和表 頂出缸活塞 行程為 250到頂出缸的速度循環(huán)圖如下: 圖 頂出 缸速度循環(huán)圖 出缸負載分析 主缸回程停止后,頂出缸下腔進油,活塞上行,這時會產生慣性、靜摩擦力、動摩擦力等負載。由于頂出缸工作時的壓力遠小于主缸的工況壓力,而且質量也比主缸滑塊小很多,慣性負載很小,計算時可以忽略不計;同理摩擦負載與頂出力相比也很小,也可不計;工件頂出時的工作負載比較大,計算頂出缸的最大工作負載時可以近似等于頂出力。將參數代入公式 算頂出缸的最大負載。 即: F = 350000N 式中: 頂出力; 19 出缸負載循環(huán)圖 ( 1)頂出缸工作循環(huán)各階段外負載如表 頂出缸工作循環(huán)負載 工 作 循 環(huán) 外 負 載 啟 動 F = F 靜 + 略不計 頂出缸頂出 F = = f 動 + 350 速退回 F = f 動 + F 背 ≈ 8 :“ f 靜 ”表示啟動時的靜摩擦力,“ f 動 ”表示啟動后的動摩擦力。 ( 2)頂出缸各階段負載循環(huán)如圖 頂出缸負載循環(huán)圖 壓系統(tǒng)原理圖擬定 壓系統(tǒng) 供油方式及調速回路的選擇 液壓機工進時負載大,運動速度慢,快進、快退時的負載相對于工進時要小很多,但是速度卻比工進時要快。為了提高液壓機的工作效率,可以采用雙泵或變量泵供油的方式。綜合考慮,液壓機采用變量泵供油,基本油路如圖 示。 由于液壓機工況時的負載壓力會逐步增大,為了使液壓機處于安全的工作狀態(tài),調速回路采用恒功率變量泵調速回路。當負載壓力增大時,泵的排量會自動跟著減小,保持壓力與流量的乘積恒為常數,即:功率恒定,如圖 示。 20 1 2 3 4 5圖 液壓機基本回路圖 圖 恒功率曲線圖 壓系統(tǒng)速度換接方式的選擇 液壓機加工零件的過程包括主缸的快進、工進、快退和頂出缸的頂出、快速回程。采用什么樣的方式進行速度的安全、準確換接是液壓機穩(wěn)定工作的基礎。為了達到控制要求,液壓系統(tǒng)的速度換接通過行程開關控制。這種速度換接方式具有平穩(wěn)、可靠、結構簡單、行程調節(jié)方便等特點,安裝也很容易。 21 壓系統(tǒng)原理圖 液壓系統(tǒng)采用插裝集成控制系統(tǒng),該控制系統(tǒng)具有密封性好、流通能力大、壓力損失小、易于集成等優(yōu)點。液壓機系統(tǒng)控制原理如圖 示。 1、 2、 6、 18、 15、 10、 11 1S、 2S、 3 3、 7 14單向閥 4、 5、 8、 9、 12、 13、 16、 17、 19、 20 21 22 23、 24 25 壓力表 26 27 28、 29、 30、 31梭閥 圖 液壓機插裝閥控制系統(tǒng)原理圖 壓系統(tǒng)控制過程分析 整個液壓控制系統(tǒng)包括五個插裝閥集成塊,插裝閥工作原理分析如下: 成進油調壓回路,其中 單向閥,用于防止系統(tǒng)中液壓油倒流回泵, 先導溢流閥 2 用于調整系統(tǒng)的壓力,先導溢流閥 1 用于限制系統(tǒng)的最高壓力,緩沖閥 3 與電磁換向 4 用于液壓泵卸載和升壓緩沖; 成主缸 23 油液三通回路,先導溢流閥 6 是用于保證主缸的安全 閥, 22 緩沖閥 7 與電磁換向閥 8 用于主缸上腔卸壓緩沖; 成主缸下腔油液三通回路,先導溢流閥 11 用于調整主缸下腔的平衡壓力,先導溢流閥 10 為主缸下腔安全閥; 成頂出缸上腔油液三通回路,先導溢流閥 15 為頂出缸上腔安全閥,單向閥 14 用于頂出缸作液壓墊,活塞浮動時上腔補油; 成頂出缸下腔油液三通回路,先導溢流閥 18 為頂出缸下腔安全閥。 除此之外,進油主閥 控制油路上都有一個壓力選擇梭閥,用于保證錐閥關閉可靠,防止反壓開啟。 壓機執(zhí)行部件動作過 程分析 液壓機主缸、頂出缸工作循環(huán)過程分析如下: ( 1)主缸 1)啟動 —— 按下啟動按鈕,所有電磁鐵處于失電狀態(tài),三位四通電磁閥 4閥芯處于中位。插裝閥 制腔經閥 3、閥 4 與油箱接通,主閥開啟。液壓泵輸出的油液經閥 回油箱,泵空載啟動。 2)主缸滑塊快速下行 —— 電磁鐵 1Y、 3Y、 6Y 得電,這時插裝閥 閉,啟,泵向系統(tǒng)供油,輸出油液經閥 入主缸上腔。主缸下腔油液經閥 速流回油箱。滑塊在自重作用下快速下行,這時會因為下行速度太快,泵的輸出流量來不及填充上腔而在上腔形成負壓。充液閥 21 打開,上部油箱對上腔進行補油,滑塊的快速下行。 3)滑塊減速下行 —— 當滑塊行至一定位置觸動行程開關 2S 后,電磁鐵 67Y 得電,插裝閥 制腔先導溢流閥 11 接通,閥 閥 11 的調定壓力下溢流,主缸下腔會產生一定的背壓。主缸上腔的壓力這時會相應升高,充液閥 21 關閉。主缸上腔進油僅為泵的輸出流量,滑塊減速下行。 4)工進 —— 當滑塊減速行進一段距離后接近工件,主缸上腔的壓力由壓制負載決定,主缸上腔的壓力會不斷升高,變量泵輸出流量會相應自動減少。當主缸上腔的壓力達到先導溢流閥 2 的調定壓力時,泵的輸出流量 全部經閥 流,此時滑塊停止運動。 5)保壓 —— 當主缸上腔的壓力達到所需要求的工作壓力后,電接點壓力表發(fā)出電信號,電磁鐵 1Y 、 3Y、 7Y 全部失電,閥 閉。主缸上腔閉鎖,實現保壓,同時閥 啟,泵卸載。 6)主缸上腔泄壓 —— 主缸上腔此時的壓力已經很高,保壓一段時間后,時間繼電器發(fā)出電信號,電磁鐵 4Y 得電,閥 制腔通過緩沖閥 7 及電磁換向閥 8 與油箱接通,由于緩沖閥 7 的作用,閥 慢開啟,主缸上腔實現無沖擊 23 泄壓,保證設備處于安全工作狀態(tài)。 7)主缸回程 —— 當主缸上腔的壓力降到一安全值后,電接點 壓力表發(fā)出電信號,電磁鐵 2Y、 5Y、 4Y、 12Y 得電,插裝閥 閉,閥 啟,充液閥 21 開啟,壓力油經閥 入主缸下腔,主缸上腔油液經充液閥 21 和閥別流回上部油箱和主油箱,主缸完成回程。 8)主缸停止 —— 當主缸回程到達上端點,觸擊行程開關 1S,全部電磁鐵失電,閥 啟,泵卸載。閥 主缸下腔封閉,上滑塊停止運動。 ( 2)頂出缸 1)工件頂出 —— 當主缸回程停止運動后,按下頂出按鈕,電磁鐵 2Y、 9Y、10Y 得電,插裝閥 啟,液壓油經閥 入頂出缸下腔,上腔油液經閥 回油箱,工件頂出。 2)頂出缸退回 —— 按下退回按鈕,電磁鐵 9Y、 10Y 失電,電磁鐵 2Y、 8Y、11Y 得電,插裝閥 啟,液壓油經閥 入頂出缸上腔,下腔油液經閥 回油箱,頂出缸回程。 ( 3)液壓系統(tǒng)電磁鐵動作順序表 電磁鐵動作順序如表 液壓機液壓系統(tǒng)電磁鐵動作順序表 執(zhí)行部件 工 況 1Y 2Y 3Y 4Y 5Y 6Y 7Y 8Y 9Y 10Y 11Y 12Y 主 缸 快速下行 + + + 工進、加壓 + + + 保 壓 泄 壓 + 回 程 + + + + 停 止 頂 出 缸 頂 出 + + + 退 回 + + + 停 止 注:“ +”表示電磁鐵處于得電狀態(tài)。 24 壓系統(tǒng)基本參數計算 壓缸基本尺寸計算 ( 1)主缸工作壓力、內徑、活塞桿直徑的確定 查表 21]并參考表 液壓機的工作負載比較 大,取主缸的工作壓力為 P=26 計算主缸內徑和活塞桿直徑。由主缸負載圖 知最大負載 F=100T。查表 21],由主缸工作壓力為 26d/D 為 液壓缸的機械效率 η 壓缸受力如圖 圖 液壓機主缸受力簡圖 由圖 22212 )(44 ?? ??D=]})(1[1{42121 ???(式中 : 液壓缸工作壓力; 液壓缸回路背壓,對于高壓系統(tǒng)初算時可以不計; F— 工作循環(huán)中最大負載; η 液壓缸機械效率,一般η 將參數代入公式( 求得液壓缸內徑 即: D=??? 32725 查表 21],將液壓缸的內徑圓整為標準系列直徑,取 D=320么由d/D= 即: d= 229理查表 21],將活塞桿直徑圓整為標準系 列直徑,取 d=220 經過計算液壓機主缸的內徑、活塞桿直徑分別為: D=320 d=220 ( 2)頂出缸工作壓力、內徑、活塞桿直徑的確定 頂出缸工作負載與主缸相比要小很多,查表 21],取頂出缸的工作壓力P=12計算頂出缸內徑和活塞桿直徑。由頂出缸負載圖 =350表 21],缸工作壓力為 12取 d/D 為 液壓缸的機械效率 η 壓缸受力如圖 圖 液壓機頂出缸缸受力簡圖 將參數代入公式( 求得液壓缸內徑 即: D=??? 198表 21],將液壓缸的內徑圓整為標準系列直徑,取 D=200么由d/D= 即: d= 138理查表 21],將活塞桿直徑圓整為標準系列直徑,取 d=140 經過計算液壓機頂出缸的內徑、活塞桿直徑分別為: D=200 d=140 26 壓系統(tǒng)流量計算 ( 1)主缸所需流量計算 參考表 主缸各個工況所需流量進行計算。已知主缸的快進速度為 s,工進速度為 s,快速回程速度為 s,主缸內徑為 320塞桿直徑為 220 由流量計算公式: ??? ( 快進時: 快進快進 ??? 32 ????? )(?≈ 進時: 工進工進 ??? 32 ????? )(?≈ 退時: 快退快退 ??? 3322 ?????? (?≈ 2)頂出缸所需流量計算 參考表 頂出缸各工況所需流量進行計算。已知頂出缸的頂出速度為 s,快退速度為 s,頂出缸內徑為 200塞桿直徑為 140入公式( 即: 頂出時: 頂出頂出 ??? 32 ????? )(?≈ 退時: 快退快退 ??? 3322 ?????? ()(?=48L/ 3)液壓泵額定壓力、流量計算及泵的規(guī)格選擇 1)泵工作壓力確定 實際工作過程中,液壓油在進油路中有一定的壓力損失,因此在計算泵的工作時必須考慮壓力損失。泵的工 作壓力計算公式為: ??? 1 ( 27 式中: 液壓泵最大工作壓力; 執(zhí)行部件的最大工作壓力; P?? — 進油路中的壓力損失,對于簡單的系統(tǒng),取 于復雜系統(tǒng),取 本液壓機執(zhí)行部件的最大工作壓力 6油路中的壓力損失,取P?? =入公式( 可求得泵的工作壓力。 即: M ?? 通過計算,泵的工作壓力 壓力是系統(tǒng)的靜壓力,而系統(tǒng)在各種工礦的過渡階段出現的動態(tài)壓力有時會超過靜壓力。此外,為了延長設備的使用壽命,設備在設計時必須有一定的壓力儲備量,并確保泵的壽命,因此在選取泵的額定工作壓力 滿足,取 即: )液壓泵最大流量計算 通過對液壓缸所需流量的計算 ,以及各自的運動循環(huán)原理,泵的最大流量可由公式 (算得到。 m P ??(式中: 液壓泵的最大流量; 液壓系統(tǒng)泄漏系數,一般取 q?— 同時動作的各執(zhí)行元件所需流量之和的最大值。如果這時溢流閥正處于溢流狀態(tài),還應加上溢流閥的最小溢流量。 將參數代入公式( ,即: m ?? ≈ 463L/)液壓泵規(guī)格選擇 查表 51],根據泵的額定壓力,選取液壓泵的型號為: 250 基本參數如下: 排量: 250mm/r ; 額定壓力: 32 額定轉速: 1000r/ 容積效率: 92% ; 4)泵的流量驗算: 由液壓泵的基本參數可知泵每分鐘排量 q =160ml/r× 1000r/50L/28 而泵實際所需的最大流量63L/壓機出現供油不足,快進無法實現。為了滿足液壓機的正??爝M,必須在液壓系統(tǒng)中設置補油油箱。 動機的選擇 液壓機的執(zhí)行件有兩個,即:主缸和頂出缸。主缸和頂出缸各自工況的快進、工進、回程速度又不盡相同,這樣對功率的消耗也不同。電動機額定功率的確定必須根據消耗功率最大的工況來確定,因此要分別計算主缸、頂出缸各工況消耗的功率。功率計算公式如下: P=? (式中: 液壓泵的流量; η η = ( 1)主缸各工況功率計算 1)快進功率 主缸滑塊快進時,在自重作用下速度比較快,而液壓泵此時的輸出油量不能滿足滑塊的快速下行??爝M時的負載很小,只有活塞與缸筒、導柱與滑塊之間的摩擦負載,這樣泵的出口壓力也很小,消耗的功率不會很大。 2)工進功率 由主缸負載循環(huán)圖 及,工進時主缸最大負載為 100T,無桿腔面 積A= ( m??≈ ,進油回路壓力損失取 ? P=液壓泵的壓力 算。 ?? ( 即: P P 6526 02 ?????? 將 ? 、 =,求得工進功率為 : a m 5 ???? 29 3)快退功率 由圖 退負載為 40022 ??? )()(?,取進油回路壓力損失取 ? P=入公式( 求得泵的壓力 P 。 即: P P 6523 04 0 0 ?????? 將 ? 、 =入公 式( ,求得快退功率即為: a m ???? 出時主缸最大負載為 350桿腔面積 A= ( m??≈ 進油回路壓力損失取 ? P=么液壓泵的壓力 算。 即: P P 6526 ????? 將 ? 、 =,求得工進功率即為: a m 1