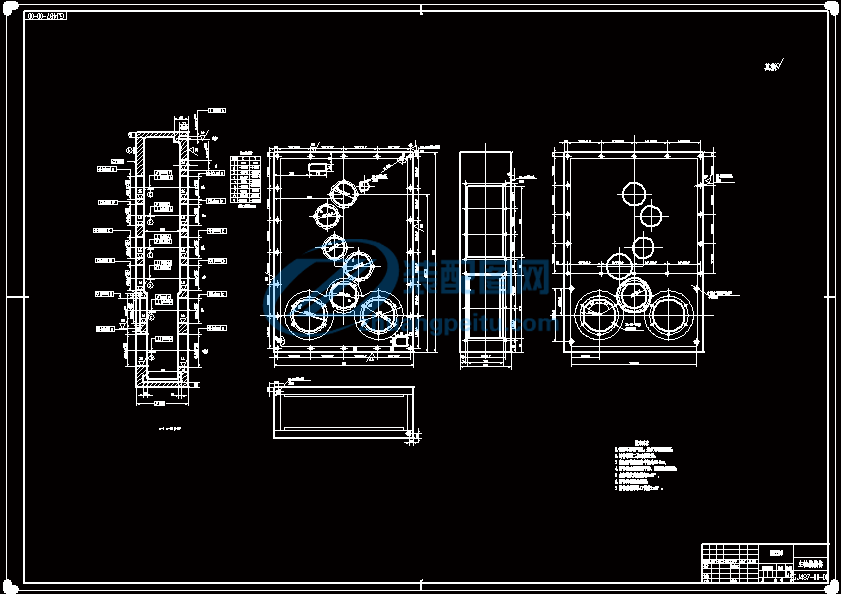
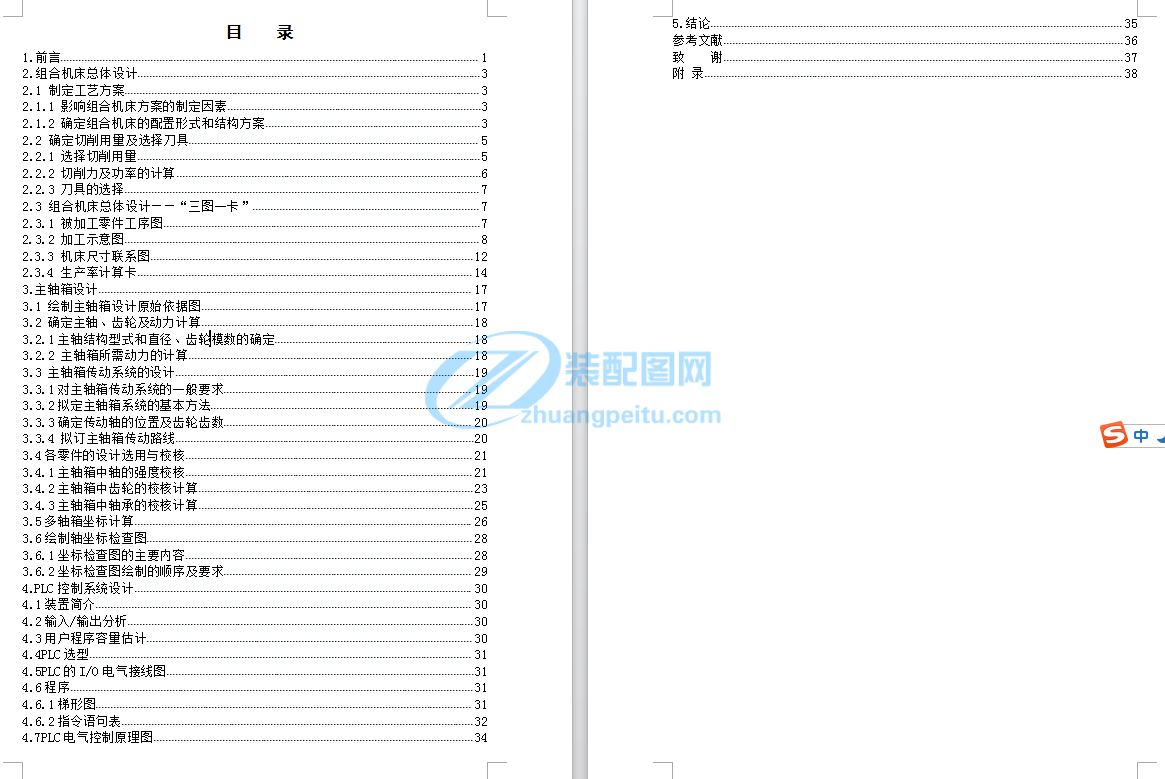
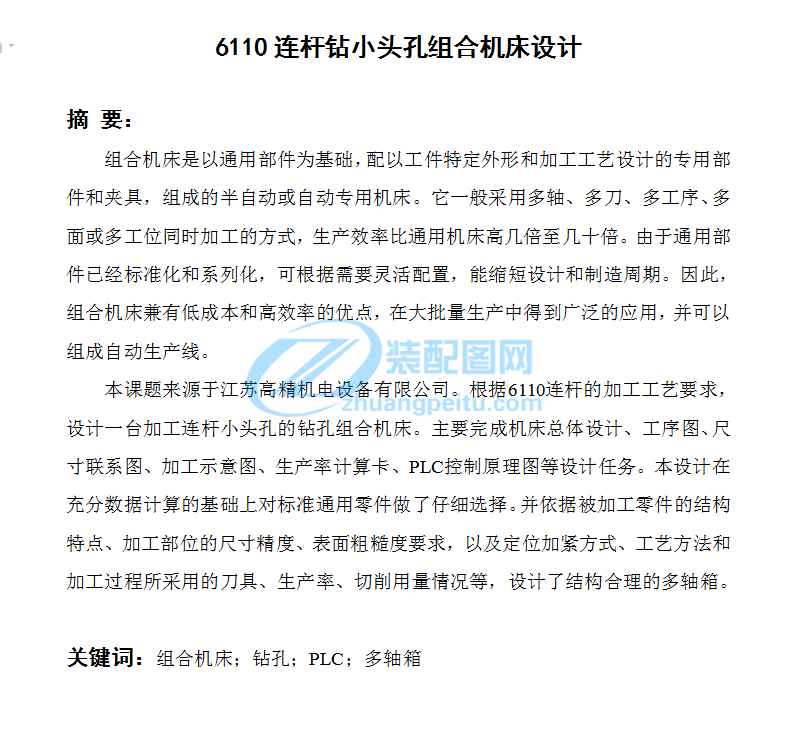
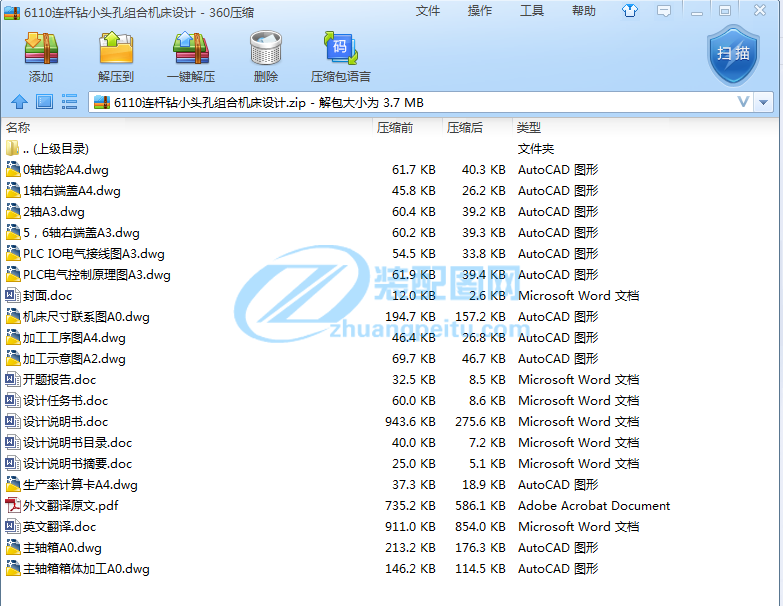
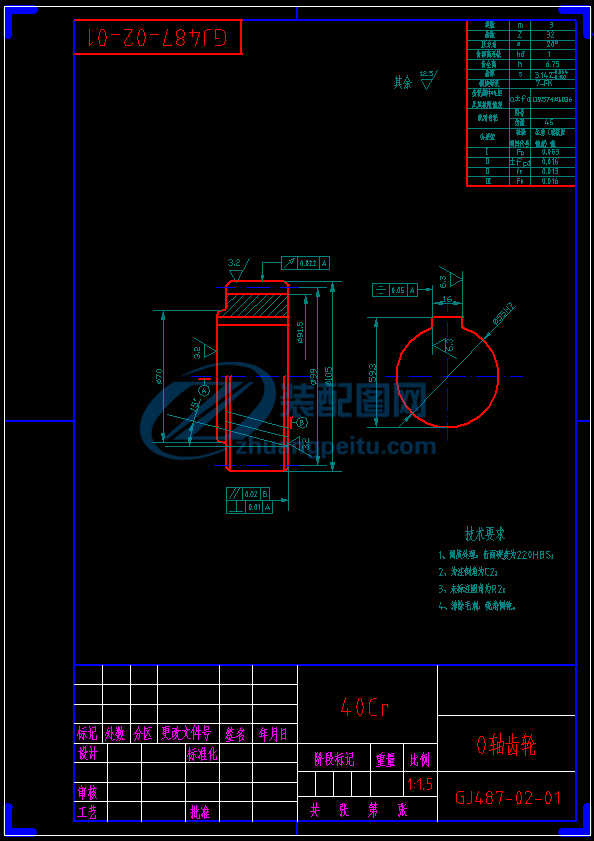
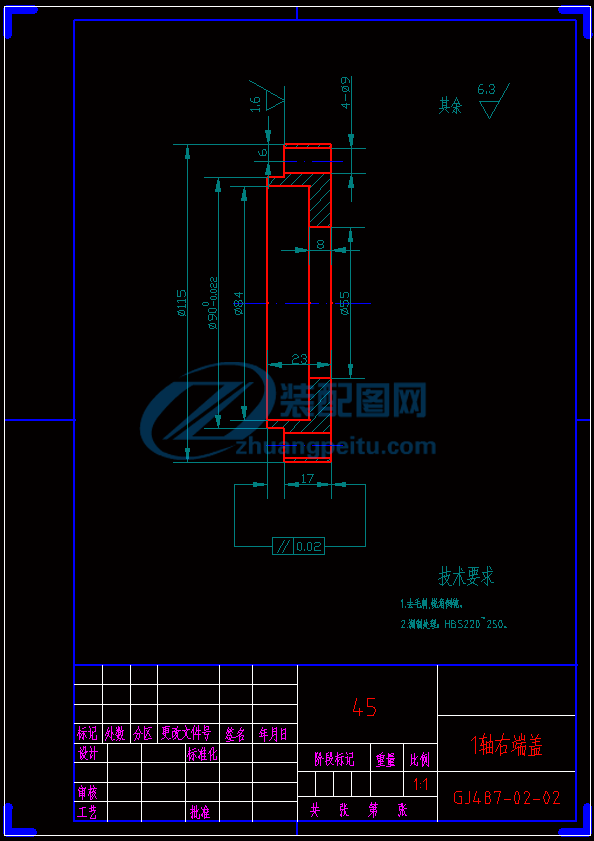
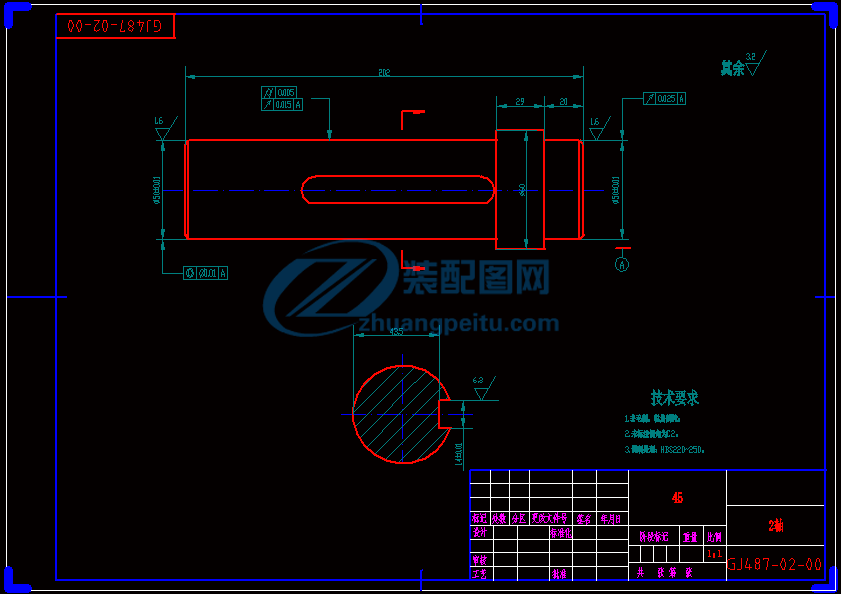
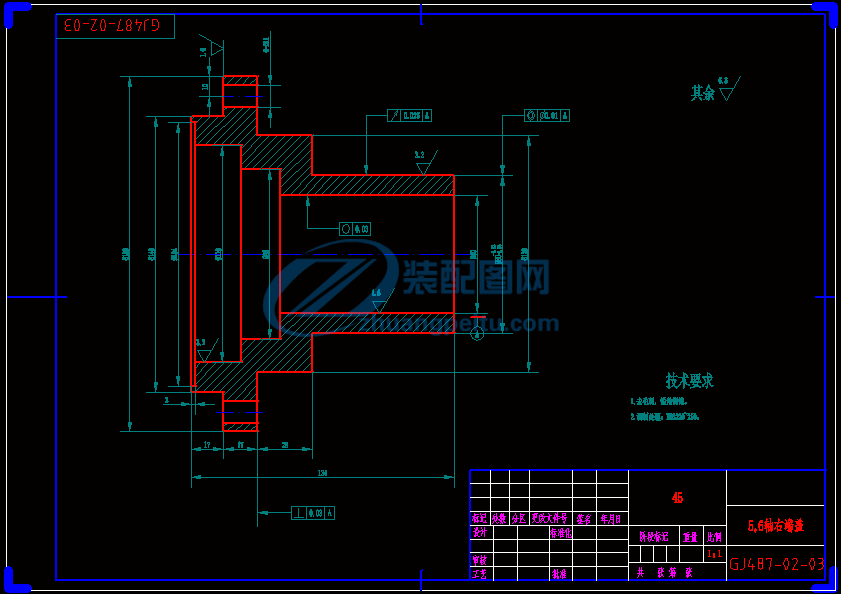
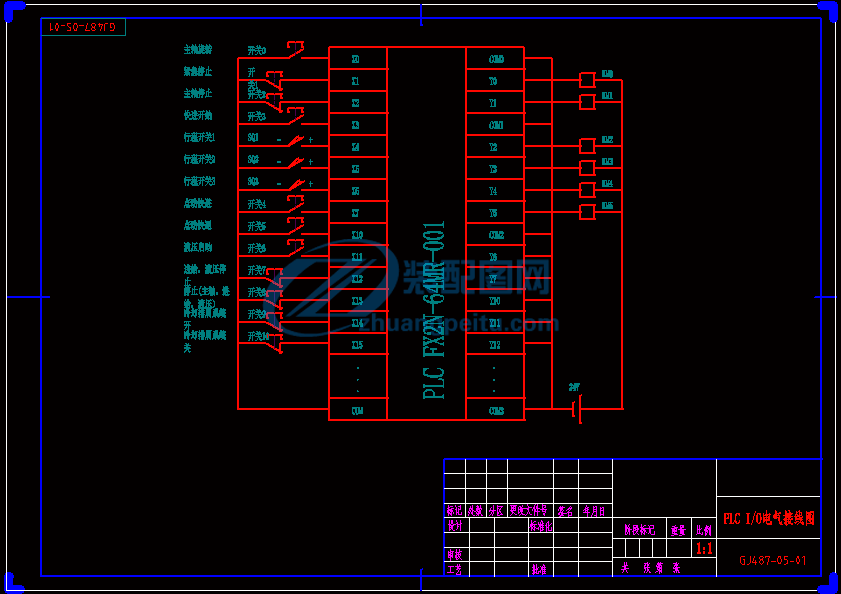
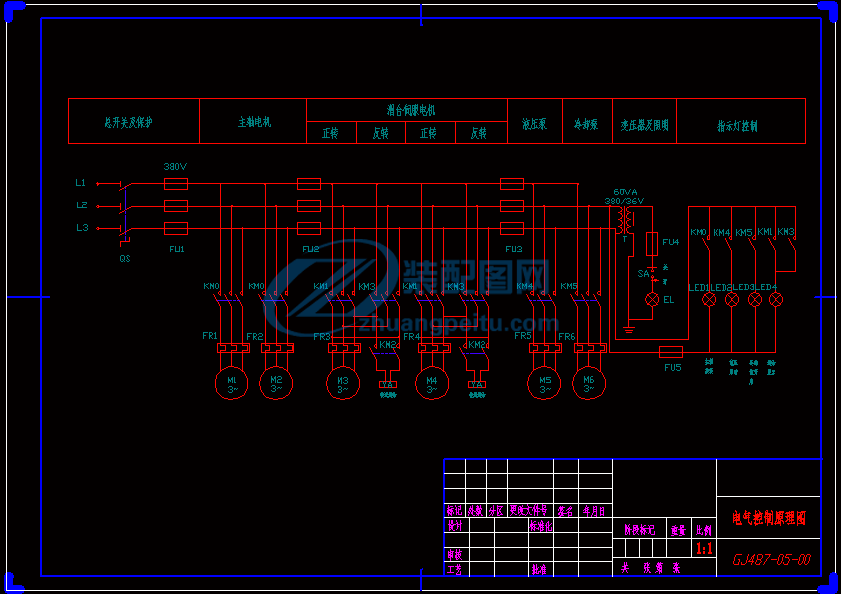
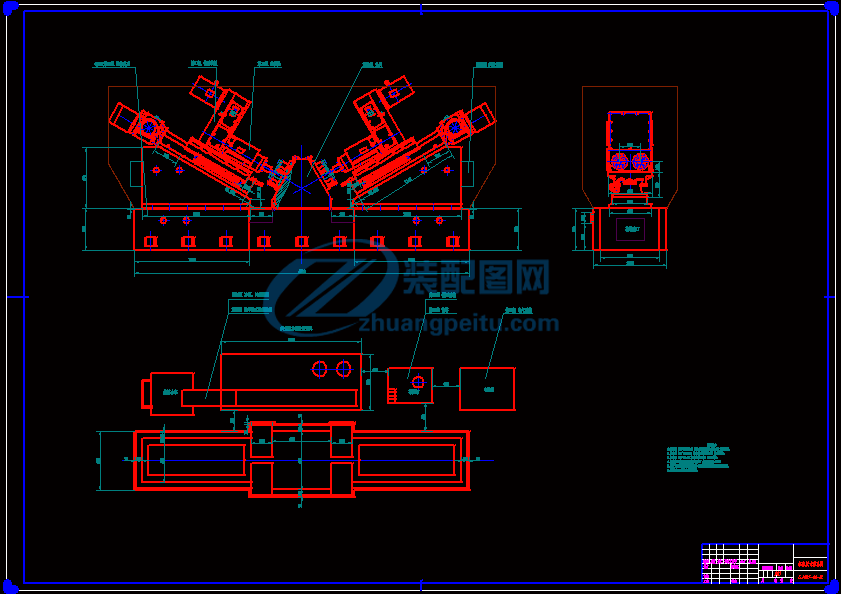
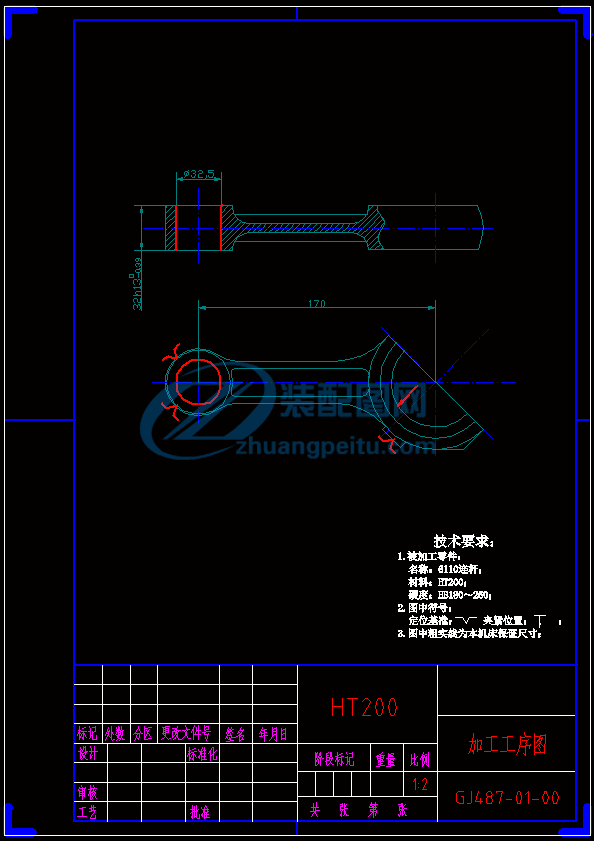
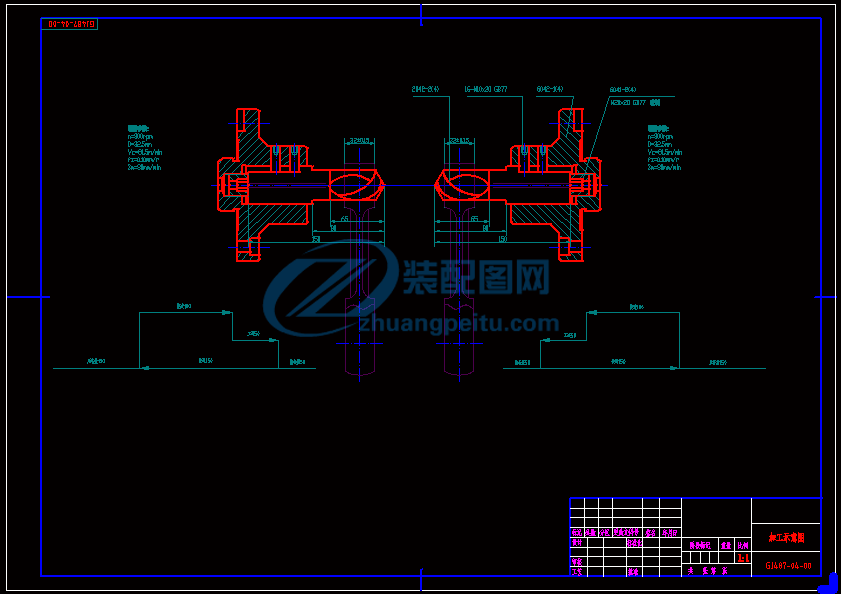
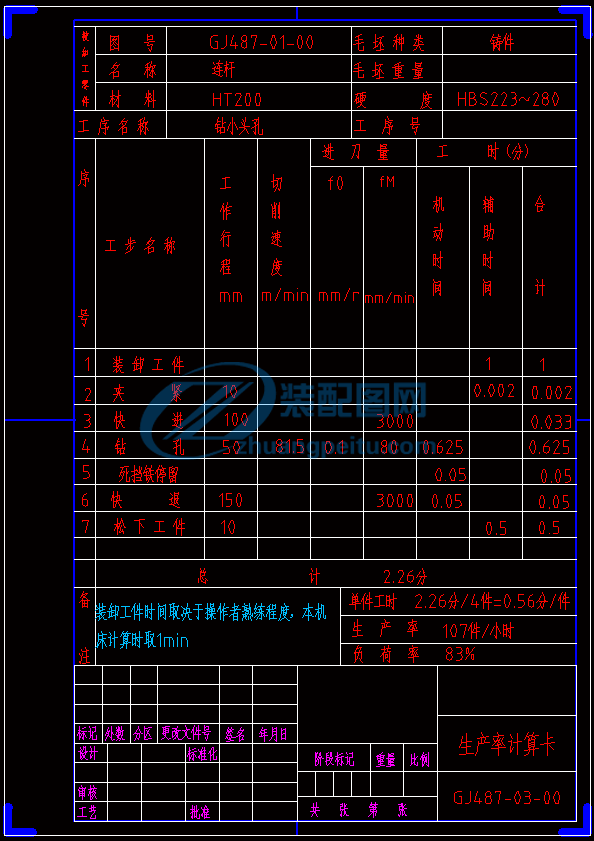
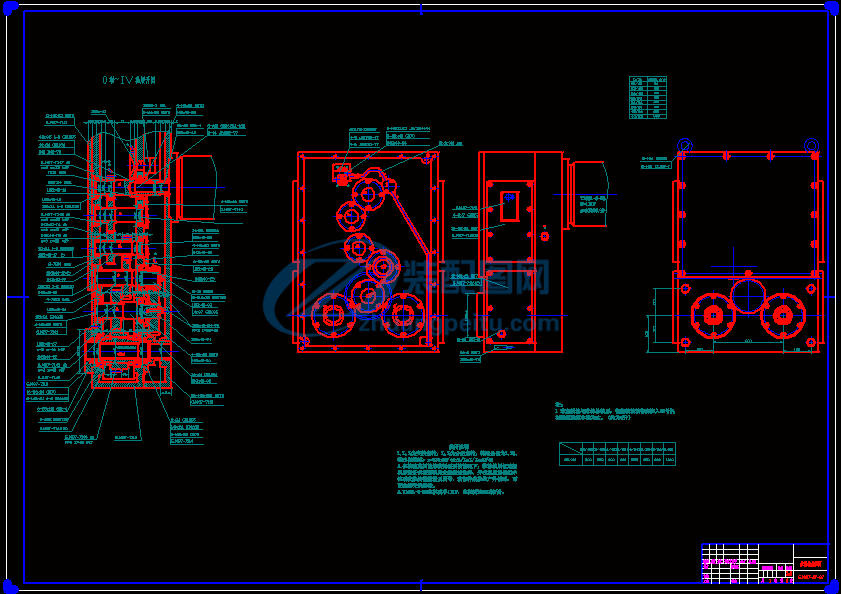
6110 連桿鉆小頭孔組合機床設計0一、 前 言1.1 組合機床的發(fā)展及概況 組合機床是根據工件加工需要,以大量通用部件為基礎,配以少量專用部件并按工序高度集中的原則設計的。它是可以同時完成鉆孔、擴孔、鉸孔、鏜孔、車端面、車削和銑削等工序的高效率的專用機床,它一般采用多軸、多刀、多工序、多面、多工位同時加工。與萬能機床和專用機床相比,組合機床有重新改裝的優(yōu)越性,其通用零、部件可以多次重復利用。加工過程中采用多軸對被加工零件一個面上的許多孔同時進行加工,這樣不僅較好地保證各孔之間的精度、提高產品質量、減少工件工序間的搬運、改善勞動條件,也減少了機床占地面積。由于組合機床大多數零、部件是同類的通用部件,這就縮短了設計和制造周期,簡化了機床的維護和修理。必要時甚至可以更換整個部件,以提高機床的維修速度?,F代化的大生產使組合機床得到了較為廣泛的應用, 但也對組合機床的使用周期提出了嚴峻的挑戰(zhàn),糾其原因主要是機械行業(yè)特別是汽車產業(yè)產品更新換代不斷加快, 生產作業(yè)線日趨柔性化。由于產品生產工藝及流程經常變化, 需靈活地改變控制程序, 以使機械設備或生產過程按預定的條件和順序來運行或執(zhí)行。在控制系統(tǒng)方案中, PLC 已成為當今增長速度最快的工業(yè)控制設備, 它具備了許多獨特的優(yōu)點, 能較好地解決工業(yè)控制領域普遍關心的可靠性、安全性、靈活性、經濟性、方便性等問題。操作員可以通過命令監(jiān)控相關部分的運行狀態(tài), 根據具體的工藝要求, 對進給控制、調整定時等進行詳細設定, 從而實現“集中管理, 分散控制” 。因此采用了 PLC 來實現對主軸孔加工用機床操作過程的自動控制。1.2 組合機床的工藝范圍及特點組合機床適宜于各種大中型箱體類零件,目前組合機床主要用于平面加工和孔加工兩類工序。其中孔加工包括鉆、擴、鉸、鏜孔及倒角、切槽、攻螺紋、锪沉孔、滾壓孔等。隨著自動化的發(fā)展,組合機床的工藝范圍已擴展到了車外圓等工序。組合機床具有如下特點:1) 主要用于加工箱體類零件和雜件的平面和孔。2)生產率高??啥嗝妗⒍喙の?、多軸、多刀同時自動加工。3)加工精度穩(wěn)定。可選用成熟的通用部件、精密夾具來保證加工精度。4)研制周期短,便于設計、制造和使用維護,成本低。5)自動化程度高,勞動強度低。6)配置靈活。因為結構模塊化、組合化,機床易于改裝;產品或工藝變化時,通用部件還可以重復利用。1.3 機床設計的課題來源、設計內容及要求1.3.1 課題來源1該畢業(yè)設計課題是 6110 連桿鉆小頭孔組合機床設計,來源于江蘇高精機電設備有限公司,主要為了解決以前工作效率低,加工精度不高,勞動強度大的問題。這次畢業(yè)設計是在實習的基礎上進行的。在工程技術人員的帶領下,深入車間,了解被加工零件的加工特點、精度和技術要求以及生產率的要求等,確定在組合機床上完成的工藝內容及其加工方法。我們小組通過討論,協(xié)調,既考慮工藝方案的實現,保證加工精度、技術要求及其生產效率,又考慮機床操作、維護、修理是否方便,排屑情況是否良好,還注意被加工零件的生產批量等。最后確定了機床各部件間的相互關系,選擇通用部件和刀具的導向,計算切削用量等以便使設計的組合機床符合多快好省的要求。1.3.2 設計內容1)運動設計 根據給定的被加工零件,確定機床的切削用量,通過分析比較擬定傳動方案和傳動系統(tǒng)圖,確定傳動副的傳動比及齒輪的齒數。2)動力設計 根據給定的工件,初算傳動軸的直徑、齒輪的模數;確定動力箱;計算多軸箱尺寸及設計傳動路線。完成裝配草圖后,要驗算傳動軸的直徑,齒輪模數否在允許范圍內。3)結構設計 進行主運動傳動軸系、變速機構、主軸部件、箱體、潤滑與密封等的布置和機構設計。4)編寫設計說明書1.3.3 設計要求本次課題所設計的組合機床總體應滿足零件的加工要求,保證加工精度;機床應運轉平穩(wěn)、工作可靠、結構簡單、裝卸方便、便于維修、調整;機床盡量能用通用件以便降低制造成本。6110 連桿鉆小頭孔組合機床設計2二、 組合機床總體設計2.1 組合機床工藝方案的擬訂2.1.1 制定工藝方案零件加工工藝將決定組合機床的加工質量、生產率、總體布局和夾具結構等。所以,在制定工藝方案時,必須計算分析被加工零件圖,并深入了解零件的形狀、大小、材料、硬度、剛度,加工部位的結構特點加工精度,表面粗糙度,以及定位,夾緊方法,工藝過程,所采用的刀具及切削用量,生產率要求等等。并查閱有關技術資料,制定出合理的工藝方案。根據被加工被零件(箱體)的零件圖(圖 2-1) ,加工四個螺紋底孔的工藝過程。1) 加工孔的主要技術要求:加工 1 個 Φ32.5 的孔;孔的位置度公差為 Φ0.1mm;工件材料為 HT200,HB170~241;要求生產綱領為(考慮廢品及備品率)年產量 25 萬件,單班制生產。2)工藝分析加工該孔時,孔的位置度公差為 0.1mm根據組合機床用的工藝方法及能達到的經濟精度,可采用如下的加工方案:一次性加工通孔,孔徑為 Φ32mm3) 定位基準及夾緊點的選擇選擇定位基準的原則及應注意的問題:a)盡量選擇零件設計基準作為組合機床加工的定位基準,保證加工精度b)選擇定位基準應確保工件穩(wěn)定定位c)基面統(tǒng)一原則通過分析,對該機體的加工可采用兩種定位方式。一種是“三面定位” (底面、后面、側面) ,底面限制三個自由度,右面限制兩個自由度,后面限制一個自由度。還有一種是“一面兩孔”定位。在此選三面定位方式為該加工中的主要工藝基準。2.1.2 確定組合機床的配置形式和結構方案。1)被加工零件的加工精度被加工零件需要在組合機床上完成的加工工序及應保證的加工精度,工件各孔間的位置精度為 0.1mm,它的位置精度要求不是很高,安排加工時可以在下一個安裝工位上對所有孔進行最終精加工。為了加工出表面粗糙度為 Ra3.2um 的孔。采取提高機床原始制造精度和工件定位基準精度并減少夾壓變形等措施就可以了。被加工零件圖如圖 2-1 所示:3圖 2-1 被加工零件圖2) 被加工零件的特點此箱體的材料是 HT200、硬度 HB170-241,孔的位置分配不規(guī)則,孔的直徑為Φ8.5mm。采用多孔同步加工,此零件的加工特點是中心線與定位基準平面是垂直的,并且定位基準面是水平的??椎姆植疾灰?guī)則,工件比較小,可一次鉆完,因而適合選擇立式單工位鉆床。3) 零件的生產批量零件的生產批量是決定采用單工位、多工位、自動線或按中小批量生產特點設計組合機床的重要因素。按設計要求生產綱領為年生產量為 25 萬件,從工件外形及輪廓尺寸,為了減少加工時間,采用多軸頭以提高利用率。綜上所述:通過對箱體零件的結構特點、加工部位、尺寸精度、表面粗糙度和技術要求、定位、夾緊方式、工藝方法,并定出影響機床的總體布局和技術性能等方面的考慮,最終決定設計四軸頭單工位同步鉆床。根據任務書的要求:設計的組合機床要滿足加工要求、保證加工精度;盡可能用通用件、以降低成本;各動力部件用電氣控制、液壓驅動。因此根據任務書要求和機體的特點初定兩種設計方案:A.臥式組合機床6110 連桿鉆小頭孔組合機床設計4圖 2-2 臥式組合機床結構特點:臥式組合機床重心低,振動小,運作平穩(wěn),加工精度高,占地面積大。B.立式組合機床 圖 2-3 立機床結構式組合特點:立式組合機床重心高,振動較大,加工精度高,占地面積小。通過以上比較,故選用臥式組合機床。2.2 確定切削用量及選擇刀具2.2.1 選擇切削用量合理地選擇切削用量,即確定合理的切削速度和工作進給量,能使組合機床以最少的停車損失,最高的生產效率,最長的刀具壽命和最好的加工質量也就是多、快、好、省地進行生產。在組合機床上所有的刀具共用一個進給系統(tǒng),因此,同一滑臺帶動的所有刀具每分鐘進給量相同,即等于滑臺的工進速度,即n1f1=n2f2=……=nifi=vf (2-1)其中: n 1,n 2,……n i為各主軸轉速,r/min ;f1,f 2, ……fi為各主軸進給量,mm/s;vf為動力滑臺每分鐘進給量, mm/min。本設計只需要加工一個空。按照經濟地選擇滿足加工要求的原則,采用查表的方法查得:5小孔為 Φ32.5mm 的光孔,鉆通,l=32mm。由 d>30~40,硬度 223~280HBS, 初選 v=81.5m/min,f=0.10mm/r,n 根據分組齒輪不同分別選擇,在滿足需要的情況下盡量使用低速組。2.2.2 切削力及功率的計算根據選定的切削用量(主要指切削速度 v 及進給量 f)確定切削力,作為選擇動力部件(滑臺)及夾具設計的依據;確定切削扭矩,用以確定主軸及其它傳動件(齒輪,傳動軸等)的尺寸;確定切削功率,用以選擇主傳動電動(一般指動力箱)功率,通過查文獻 表 2-6 計算如下:??1布氏硬度:HB =HBmin- (HBmax-HB min) (2-32)=170- (241-170)1=146.33切削力: =26 (2-FD8.0f6.HB3)=26×16× ×8.010.643=1313.09N切削扭矩:=10 (2-9.1D8.0f6.HB4)=10× × ×9.1T8.00.6143=6123.90N·mm切削功率: = (2-PD974v?5)=6123.90×12/(9740×3.14×16)=0.15 kw式中:HB——布氏硬度F——切削力,N;D——鉆頭直徑,mm;f——每轉進給量,mm/r;6110 連桿鉆小頭孔組合機床設計6T——切削扭矩,N·mm;V——切削速度,m/min;P——切削功率,kw。2.2.3 刀具的選擇 A.確定刀具的耐用度。刀具開始切削起,至磨損量達到磨鈍標準止的切削時間稱為刀具的耐用度。刀具耐用度反映了刀具磨損的速率,影響刀具耐用度的主要因素有切削用量,工件材料等。根據上面已經求得的機床進給速度和已經知道的工件材料,通過查文獻[4]中表 2-9,確定刀具的耐用度需要達到 90-180min。B.確定刀具的類型。確定刀具類型應考慮加工精度、表面粗糙度、排屑及生產率等要求,只要條件允許應盡量選用標準刀具。孔加工刀具(鉆、鏜、鉸等)的直徑應與加工部位尺寸、精度相適應,其長度應保證加工終了時刀具螺旋槽尾端離導向套外端 30~50mm,以利排屑和刀具磨損后有一定向前調整量。刀具錐柄插入接桿孔內長度,在繪制加工示意圖是應注意從刀具總長中減去。 根據已知條件初步決定選擇復合刀具。所謂復合刀具,就是指同時或先后順序完成兩個或兩個以上的加工工序或工步的刀具。復合刀具之所以在組合機床上大量使用,是由于它有很多優(yōu)點:a)集中工序,可減少加工工位數和機床數,有時也就減少了加工工件的機動時間和輔助時間,減少機床占地面積,節(jié)省設備投資。b)減少工件安裝和夾具轉位次數,在一個工位上孔進行粗精加工,減少精加工余量,提高加工精度,降低粗糙度。c)在一個工位上同時加工幾個加工表面,可以提高加工表面相互間的位置精度。如同一軸線的幾個孔的同軸度,端面與孔的垂直度等。箱體的布氏硬度在 HB170~241,孔徑 D 為 16mm,刀具的材料選擇高速鋼鉆頭(W18Cr4V) ,為了使工作可靠、結構簡單、刃磨簡單,選擇標準 Φ16 的麻花鉆。2.3 組合機床總體設計——“三圖一卡”繪制組合機床“三圖一卡” ,就是針對具體零件,在選定的工藝和結構方案的基礎上,進行組合機床總體方案圖樣文件設計。其內容包括:繪制被加工零件工序圖、加工示意圖、機床聯系尺寸總圖和編制生產率計算卡。2.3.1 被加工零件工序圖被加工零件工序圖是根據選定的工藝方案,表示在一臺機床上或一條自動線上完成的工藝內容、加工部位的尺寸及精度、技術要求、加工用定位基準、夾壓部位7以及被加工零件的材料、硬度和在本機床加工前毛坯情況的圖紙。它是在原有零件圖基礎上,以突出本機床或自動線加工內容,加上必要的說明繪制的。它是組合機床設計的主要依據,也是制造使用時調整機床、檢查精度的重要技術文件。繪制的被加工零工序圖如圖 2-4 所示。圖 2-4 被加工零件工序圖其原始數據其主要內容包括:A.被加工零件的形狀和主要輪廓尺寸以及與本工序機床設計有關部位結構形狀和尺寸。B.本工序所選用的定位基準、夾緊部位及夾緊方向。以便根據此進行夾具的支承、定位、夾緊和導向等機構設計。C.本工序加工表面的尺寸、精度、表面粗糙度、形位公差等技術要求以及對上道工序的技術要求。D.注明被加工零件的名稱、編號、材料、硬度以及加工部位的余量。a)在圖中注明被加工零件的名稱及編號:7170316KZ 后橋殼;材料:QT590-10;硬度:HB180~260。b)圖中符號, ---為夾緊位置 為定位基準。為使被加工零件工序圖表達清晰明了,突出本工序內容,繪制時規(guī)定:應按一定的比例,繪制足夠的視圖;本工序加工部位用粗實線表示,保證的加工部位尺寸及位置尺寸數值下方畫“__”粗實線,其余部位用細實線表示。2.3.2 加工示意圖1)加工示意圖的作用和內容6110 連桿鉆小頭孔組合機床設計8加工示意圖是被加工零件工藝方案在圖樣上的反映,表示被加工零件在機床上的加工過程,刀具的布置以及工件、夾具、刀具的相對位置關系,機床的工作行程及工作循環(huán)等,是刀具、夾具、多軸箱、電氣和液壓系統(tǒng)設計選擇動力部件的主要依據,是整臺組合機床布局形式的原始要求,也是調整機床和刀具所必需的重要文件。圖2-3 為箱體上 4 孔立式鉆床加工示意圖。在圖上應標注的內容:①機床的加工方法,切削用量,工作循環(huán)和工作行程。②工件、夾具、刀具及多軸箱端面之間的距離等。③主軸的結構類型,尺寸及外伸長度;刀具類型,數量和結構尺寸、接桿、導向裝置的結構尺寸。2)繪制加工示意圖之前的有關計算①刀具的選擇 刀具選擇考慮加工尺寸精度、表面粗糙度、切削的排除及生產率要求等因素。 (刀具的選擇前面已有說明。 )2-3 加工示意圖②導向套的選擇 在組合機床上加工孔,除用剛性主軸的方案外,工件的尺寸、位置精度主要取決于夾具導向。因此正確選擇導向裝置的類型,合理確定其尺寸、精度,是設計組合機床的重要內容。Ⅰ選擇導向類型 根據刀具導向部分直徑 d=16mm 和刀具導向的線速度v=12m/min,選擇固定式導向。Ⅱ導向套的參數 根據刀具的直徑選擇固定導向裝置,如圖 2-4 所示:固定導向裝置的標準尺寸如表 2-1 所示:9表 2-1 固定導向裝置的標準尺d D D1 D2 L L1 m R d1 d2 L016 26 35 39 36 45 18 22 M16 32 32圖 2-4 固定導向裝置固定裝置的配合如表 2-2:表 2-2 固定裝置的配合導向類別 工藝方法 1DD 刀具導向部分外徑固定導向 鉆孔 67nH67gg6③初定主軸類型、尺寸、外伸長度因為軸的材料為 40Cr,剪切彈性模量 G=81.0GPa,剛性主軸取 ψ=1/4,所以 B取 2.216,根據剛性條件計算主軸的直徑為:d B =2.216× =19.61mm (2-6)?4T490.6123式中:d——軸直徑,mm;T——軸所承受的轉矩,N·mm;6110 連桿鉆小頭孔組合機床設計10B——系數。本設計中所有主軸直徑皆取 d=20mm,主軸外伸長度為:L=115mm,D/ 為1d32/20,內孔長度為:l 1 =77mm.④選擇刀具接桿 由以上可知,多軸箱各主軸的外伸長度為一定值,而刀具的長度也是一定值,因此,為保證多軸箱上各刀具能同時到達加工終了位置,就需要在主軸與刀具之間設置可調環(huán)節(jié),這個可調節(jié)在組合機床上是通過可調整的刀具接桿來解決的,連接桿如圖 2-5 所示,圖 2-5 可調連接桿連接桿上的尺寸 d 與主軸外伸長度的內孔 D 配合,因此,根據接桿直徑 d 選擇刀具接桿參數如表 2-3 所示:表 2-3 可調接桿的尺寸d(h6) D1(h6) d2 d3 L l1 l2 l3螺母厚度20 Tr20×6 莫氏 1 號 12.061 17 188 46 42 100 12⑤確定加工示意圖的聯系尺寸從保證加工終了時主軸箱端面到工件端面間距離最小來確定全部聯系尺寸,加工示意圖聯系尺寸的標注如圖 2-3 所示。其中最重要的聯系尺寸即工件端面到多軸箱端面之間的距離(圖中的尺寸 314mm),它等于刀具懸伸長度、螺母厚度、主軸外伸長度與接桿伸出長度(可調)之和,再減去加工孔深度和切出值。⑥工作進給長度的確定 如圖 2-6 工作進給長度 應等于工件加工部位長度工LL 與刀具切入長度 和切出長度 之和。切入長 應根據工件端面誤差情況在1L2L15~10mm 之間選擇,誤差大時取大值,因此取 =7mm,切出長度 =1/3d+(3~8)=211+8 9mm,所以 =10+7+8=25mm.5.831??工L⑦快進長度的確定 考慮實際加工情況,在未加工之前,保證工件表面與刀尖之間有足夠的工作空間,也就是快速退回行程須保證所有刀具均退至夾具導套內而不影響工件裝卸。這里取快速退回行程為 155mm,快退長度等于快速引進與工作工進之和,因此快進長度 155-25=130mm.圖 2-6 工作進給長度2.3.3 機床聯系尺寸圖圖 2-7 機床聯系尺寸圖1)聯系尺寸圖的作用和內容6110 連桿鉆小頭孔組合機床設計12聯系尺寸圖用來表示機床各組成部件的相互裝配和運動關系,以檢驗機床各部件的相對位置及尺寸聯系是否滿足要求,通用部件的選擇是否合適,并為進一步開展主軸箱、夾具等專用部件、零件的設計提供依據。聯系尺寸圖也可以看成是簡化的機床總圖,它表示機床的配置型式及總體布局。如圖 2-7 所示,機床聯系尺寸圖的內容包括機床的布局形式,通用部件的型號、規(guī)格、動力部件的運動尺寸和所用電動機的主要參數、工件與各部件間的主要聯系尺寸,專用部件的輪廓尺寸等。2)選用動力部件選用動力部件主要選擇型號、規(guī)格合適的動力滑臺、動力箱。①滑臺的選用 通常,根據滑臺的驅動方式、所需進給力、進給速度、最大行程長度和加工精度等因素來選用合適的滑臺。Ⅰ驅動形式的確定 根據對液壓滑臺和機械滑臺的性能特點比較,并結合具體的加工要求,使用條件選擇 HY 系列液壓滑臺。Ⅱ確定軸向進給力 滑臺所需的進給力 = ∑ =4×1313.09=5252.36N進Fi式中: ——各主軸加工時所產生的軸向力i由于滑臺工作時,除了克服各主軸的軸的向力外,還要克服滑臺移動時所產生的摩擦力。因而選擇滑臺的最大進給力應大于 =5.30KN。進FⅢ確定進給速度 液壓滑臺的工作進給速度規(guī)定一定范圍內無級調速,對液壓滑臺確定切削用量時所規(guī)定的工作進給速度應大于滑臺最小工作進給速度的 0.5~1 倍;液壓進給系統(tǒng)中采用應力繼電器時,實際進給速度應更大一些。本系統(tǒng)中進給速度=n·f=800×0.1=80mm/min。所以選擇 HY80Ⅲ液壓滑臺,工作進給速度范圍vf4~250mm/min,快進速度 4m/min。Ⅳ確定滑臺行程 滑臺的行程除保證足夠的工作行程外,還應留有前備量和后備量。前后備量的作用是動力部件有一定的向前后移動的余地,以彌補機床的制造誤差以及刀具磨損13后能向前調整。本系統(tǒng)前備量為 20mm, HY80Ⅲ液壓滑臺的工作行程由查表可取250mm,工作行程=快進行程+工進行程+前備量+后備量,即 250=130+25+20+后備量,所以后備量取 75mm。②由下式估動力箱的選用 動力箱主要依據多軸所需的電動機功率來選用,在多軸箱沒有設計之前, 可算主P= /η (2-主 切7)=4×0.15/0.8=0.75KW式中:η——多軸箱傳動效率,加工黑色金屬時 η=0.8~0.9;有色金屬時η=0.7~0.8,本系統(tǒng)加工 HT200,取 η=0.8.動力箱的電動機功率應大于計算功率,并結合主軸要求的轉速大小選擇。因此,選用電動機型號為 Y100L—6B5 的 1TD16 IA 型動力箱,動力箱輸出軸至箱底面高度為 125mm。主要技術參數如表 2-4:表 2-4 Y90S 電機的技術參數轉速范圍(r/min)主電機傳動型號電機轉速 輸出轉速主電機功率()kw配套主軸部件型號Y90S-6 910 600 0.751TA32、1TA32M、1TZ32~1TG32③Y 軸液壓滑臺的選用摩擦系數:f=0.07~0.12 取 f=0.1F=f·N=0.1mg=0.1×9.156×10=9.156N (2-8)3)確定多軸箱輪廓尺寸本機床配置的多軸箱總厚度為 220mm,寬度和高度按標準尺寸中選取。計算時,多軸箱的寬度 B 和高度 H 可確定為:B=600mm H=860mm根據上述計算值,按主軸箱輪廓尺寸系列標準,最后確定主軸箱輪廓尺寸B×H=600 mm×860 mm。2.3.4 生產率計算卡6110 連桿鉆小頭孔組合機床設計14生產率計算卡是反映所設計機床的工作循環(huán)過程、動作時間、切削用量、生產率、負荷率等技術文件,通過生產率計算卡,可以分析擬定的方案是否滿足用戶對生產率及負荷率的要求。1)理想生產率理想生產率 Q(件/小時)是指完成年生產綱領 A(包括備品及廢品率)所要求的機床生產率。根據文獻 第 51 頁??1Q=A/tk (2-9)式中,t k——全年工時總數,h;A——年生產綱領,件。一年按 250 個工作日、兩班制,則全年工時為 4600 小時,年制造 105000 臺機床(每臺車床需一個主軸箱) ,加上 5%的備品及廢品率,則年生產綱領 A 為 110000件,所以:Q= 110000/4600=24(件/小時)2)實際生產率實際生產率 Q(件/小時)是指所設計的機床每小時實際可生產的零件數量。根據文獻[1]第 51 頁Q=60/ (2-10)T單式中: ——生產一個零件所需時間( min) ,可按下式計算:T單(2-11)T??輔單 機式中: ——機加工時間( min) , ——輔助時間( min) ,可按下式計算:機 輔(2-12)IVL工 進工 進機(2-13)裝 卸快 快 退快 進輔 TT??式中: —刀具工作進給長度,mm;L工 進—動力頭快進行程長度,mm;快 進—動力頭快退行程長度,mm;快 退—刀具工作進給速度,mm/min;V工 進—動力頭快進、快退速度,mm/min;快—工件裝卸、定位、夾緊的時間,min;T裝 卸—死擋鐵停留時間, min。I(1)機加工時間 機根據公式(2-17) ,計算鉆孔的 :T機15T 機 =50/80+0.05=0.63min(2)輔助加工時間 輔根據公式(2-18) ,計算鉆孔的 :輔T 輔 =(100+150)/3000+1.5=1.57min由此可算得單件工時 T 單=(T 總+T 輔)=(0 .63+1.57)/4=0.56 分/件Q=60/ =60/0.56=107(件/小時)單3)機床負荷率計算根據文獻 第 51 頁得:負荷率為??1=83% (2-14) 1Q?負?4)機床的生產率計算卡由上面的計算可以繪制出鉆孔的生產率計算卡,如圖 2-5 所示。表 2-5 生產率計算卡圖號 毛坯種類 鑄件名稱 箱體 毛坯重量被加工零件材料 HT200 JB297-62 硬度 HB170-241工序名稱 鉆壓盤連接孔 工序號 工時/min序號工步名稱工作行程/mm切速/(m·min -1)進給量/(mm·r -1)進給量/(mm·min -1)工進時間輔助時間1 按卸工件 12 夾 緊 10 0.0023 快 進 100 3000 0.0334 鉆 孔 50 81.5 0.1 80 0.6255 死檔鐵停留 0.056 快 退 150 3000 0.057 卸下工件 10 0.5累計 0.758 1.502單件總工時 2.26/4=0.56分/件機床生產率 107 件/h備注1、主軸轉速 706r/min2、一次安裝加工完一個工件理論生產率 128.2 件/h6110 連桿鉆小頭孔組合機床設計16負荷率 83%三、主軸箱設計主軸箱是組合機床的重要專用部件,它是根據機床總體設計所確定的工件加工孔的數量、切削用量等加工要求,安排各主軸位置,將動力和運動遞給各工作主軸,使之得到要求的轉速和轉向的動力部件。其動力來自通用的動力箱,與動力箱一起安裝于進給滑臺,完成鉆、擴、鏜、攻絲等加工工序。其特點是按專用要求設計,由通用部件組成,靠夾具的導向裝置來保證孔加工的位置精度。本人的主軸箱部分設計是連桿鉆小頭孔組合機床主軸箱的設計。由總體設計部分可知,需設計的主軸箱輪廓尺寸為 600mm 220mm;該類型的主軸箱結構典型,能?利用通用的箱體和傳動件;采用標準主軸,借助導向套引導刀具來保證被加工孔的位置精度。本課題中主軸箱由箱體、前蓋和側蓋三個部分組成。箱體材料為 HT200,前蓋等材料為 HT200;箱體的標準厚度為 35mm,前蓋厚度為 10mm,側蓋厚度為 15mm。主軸的類型為圓錐滾子軸承長主軸,主軸材料采用 40Cr 鋼,熱處理 C42。通用傳動軸一般用 45 鋼,調質 T235。 通用齒輪有傳動齒輪、動力箱齒輪和電動機齒輪三種。在主軸箱箱體內腔,可安排三排齒輪;箱體后壁與后蓋之間安排一排齒輪。通用主軸箱設計的順序是:繪制主軸箱設計原始依據圖;確定主軸結構、軸徑及模數;擬訂傳動系統(tǒng);計算主軸、傳動軸坐標,繪制坐標檢查圖;繪制主軸箱總圖,零件圖及編制組件明細表。具體內容如下所示。3.1 繪制主軸箱設計原始依據圖主軸箱設計原始依據圖,是根據“三圖一卡”整理編繪出來的,其內容包括主軸箱設計的原始要求和已知條件。(1)主軸箱輪廓尺寸 600×220mm。(2)機體對輪廓尺寸以及每個孔的位置尺寸。(3)機體對與主軸箱相對位置尺寸。17根據這些數據可編制出主軸箱設計原始依據如圖 3-1 所示。圖 3-1 主軸箱設計原始依據3.2 確定主軸、齒輪及動力計算3.2.1 主軸結構型式和直徑、齒輪模數的確定主軸的型式和直徑,主要取決于工藝方法,刀具主軸連接結構、刀具進給抗力和切削轉矩。如鉆孔時常采用滾珠軸承主軸,擴、鏜孔等工序常采用滾錐軸承主軸;主軸間距較小是常采用滾針軸承主軸。齒輪模數 (單位 mm)一般用類比法確定,也可按文獻[1]公式估算,即m(3-1)3(0~2)Pzn?式中, —齒輪所傳遞的功率, kw;P—一對嚙合齒輪中的小齒輪齒數;Z—小齒輪的轉速,r/min。N主軸箱中的齒輪模數常用 2、2.5、3、3.5、4 幾種。為了便于生產,同一主軸箱中的模數規(guī)格不要多于兩種。由于本主軸箱為鉆孔主軸箱,主軸轉速誤差較小,且加工孔的位置比較集中,可以根據實際需要選出齒輪模數為 2、3、4 三種。3.2.2 主軸箱所需動力的計算6110 連桿鉆小頭孔組合機床設計18主軸箱的動力計算包括主軸箱所需要的功率和進給力兩項。 (3-2)PP??切 削 損 失主 軸 箱 空 轉式中, ——切削功率,kw;P切 削——空轉功率,kw;空 轉——與負荷成正比的功率損失,kw。損 失根據文獻 表 4-6 得??6=0.018kw空 轉=1188w P切 削=1188x1%=11.88 w 損 失所以可得到 = 0.018 +1.188+0.01188=1.218kw主 軸 箱主軸箱所需進給力 (單位 N)可按式 3-3 計算F主 軸 箱(3-3)1niF??主 軸 箱式中: ——各主軸所需的軸向切削力,單位為 N;iF=3765N。主 軸 箱3.3 主軸箱傳動系統(tǒng)的設計主軸箱傳動系統(tǒng)設計是根據動力箱驅動軸位置和轉速、各主軸位置及其轉速要求,設計傳動鏈,把驅動軸和各主軸連接起來,使各主軸獲得預定的轉速和轉向。3.3.1 對主軸箱傳動系統(tǒng)的一般要求對主軸箱傳動系統(tǒng)設計的一般要求有:A.在保證主軸的強度﹑剛度﹑轉速和轉向要求的前提下,力求使傳動軸和齒輪為最少;B.主軸﹑傳動軸和齒輪的規(guī)格要盡可能少;C.最佳傳動比為 1~1.5;D.盡可能避免升速傳動。3.3.2 擬定主軸箱系統(tǒng)的基本方法主軸的分布通??梢苑譃椋和膱A分布、直線分布和任意分布三種。擬定多軸箱傳動系統(tǒng)的基本方法是:先把全部主軸中心盡可能分布在幾個同心圓上,在各個同心圓的圓心上分別設置中心傳動軸,非同心圓分布的一些主軸也宜設置中間傳動軸(如一根傳動軸帶兩根或三根主軸) ,然后根據已選定的各中心傳動軸再作同心圓,并用最少的傳動軸帶動這些中心傳動軸,最后通過合攏傳動軸與動力箱驅動軸使之連接起來。19(1)根據工序圖,采用任意分布;(2)驅動軸的設置驅動軸直接帶動的軸數不能超過兩根,以免給裝配帶來困難。驅動軸的旋轉方向可任意選擇;動力箱與多軸箱連接時,應注意驅動軸中心一般設置于多軸箱箱體寬度的中心線上,其中心高度則決定于所選動力箱的型號規(guī)格。3.3.3 確定傳動軸的位置及齒輪齒數傳動方案擬訂之后,通過“計算、作圖和多次試湊”相結合的方法,確定齒輪齒數和中間傳動軸的位置及轉速。由各主軸幾驅動軸轉速求驅動軸到各主軸之間的傳動比主軸 n 8=n9=……=n19=800r/min驅動軸 970r/min470/minor?各主軸總傳動比 i =800/970=0.825為使結構緊湊,主軸箱體內的齒輪傳動副的最佳傳動比為 1~1.5;另外,主軸與驅動軸轉向相同時,經過偶數個傳動副。3.3.4 擬訂主軸箱傳動路線該主軸箱有 7 根主軸,由傳動軸 0 傳動。具體傳動路線見圖 3-2。圖 3-2 傳動樹形圖6110 連桿鉆小頭孔組合機床設計203.4 各零件的設計選用與校核主軸箱零件校核:a)軸承校核:設計中所用的所有重要軸承都要經過壽命校核。在滿足尺寸和強度要求的情況下,盡可能地選用國產軸承。b)軸的校核:設計中所用的所有較重要的軸都要經過強度校核和剛度校核。c)齒輪校核:設計中所用的所有齒輪都要經過強度校核。d)鍵及花鍵:設計中所用的所有較重要的鍵及花鍵都要經過強度校核。e)銷與螺釘:設計中所用的所有較重要的銷與螺釘都要經過強度校核。3.4.1 主軸箱中軸的強度校核A.軸系零件的軸向固定為使軸和軸上零件在機器中有正確的位置,防止軸系軸向竄動和正確傳遞軸向力,軸系零件應予軸向固定。常見的軸向固定方式有三種:a)兩端單向固定的支承結構;b)一端雙向固定,一端游動的支承結構;c)兩端游動的支承結構。軸系零件不論采取哪種固定方式,都是根據具體情況通過選擇軸承的內圈與軸,外圈與軸承座孔的固定方式來實現的。軸承內外圈的周向固定主要由配合來保證,軸承內圈和軸的軸向固定,其原則及方法與一般軸系的軸向固定方式基本相同,外圈與軸承座孔的軸向固定形式主要是利用軸承蓋、孔用彈性墊圈、套孔的凸肩以及軸承座孔的凸肩。具體選擇時要考慮軸向載荷的大小,方向,轉速高低,軸承的類型,支承的固定型式等情況。根據上面的要求,結合本設計情況,主軸箱內的軸系零件的軸向固定方式采用兩端單向固定的支承結構。B.軸的結構軸的結構主要取決于:軸在機器中的安裝位置及形式;軸上零件的類型,尺寸及配置,定位和固定方式;載荷的性質,大小,方向及分布情況;軸的加工和裝配工藝性等。由于影響軸結構的因素較多,其結構隨具體條件不同而靈活變化,所以軸一般并無標準的結構形式。但不論何種具體條件,軸的結構均須滿足:足夠的強度和剛度;軸和裝在軸上的零件應有準確的工作位置;軸上的零件應便于裝拆和調整;軸應該具有良好的制作工藝性。 C. 計算各軸扭矩,確定各軸直徑 為設計計算方便,將各根軸分別編號為 0、1、2、3……6。根據主軸位置和轉速要求,設計齒輪傳動系統(tǒng)。已知驅動軸轉速為 970r/min,則可通過各齒輪的嚙合關系求出各軸的轉速:n0=970r/minn1=970*32/45=689.8r/minn2=689.8*45/45=689.8r/minn3=689.8*38/46=569.8r/min21n4=569.8*45/23=1114.9r/minn5=1114.9*40/43=1037.1r/min根據文獻 第 66 頁??1(3-4)nUTT???21總 Nm41.910.986323 ????總根據文獻[2]表 5-10 選 d1=d2=……d7=25mm同樣通過計算查表 5-10 選得d0=55mm,d1=50mm,d2=50mm,d3=60mm.d4=60mm,d5=d6=110mmd.軸的校核根據裝配圖上各軸的受載情況知,軸 0 在所有軸種受到的載荷最大,所以校核軸 0。根據文獻 公式 7-6 輪齒的受力大小可算得:??82x 9141.41/40=457.07N307.8.5tTFNd???總tg =457.07×tg20°=166.36Nrt?/cos =457.07/cos20°=486.40Nnt?457.07x40/2=9141.4Nmm708.5203782tHFDMN??486.40x40/2=9728N mm14.9.165.nV?166.36x40/2=3327.2Nmm257.8.4.92rFm??6400.8 Nmm126.VVMN?=9362.81 NmmH??Wcac???P1??根據文獻[8]表 10-5 抗彎截面系數(3-5)31.0dW?MPaca 47.)3(1.089623?????6110 連桿鉆小頭孔組合機床設計22根據文獻 表 10-1 軸的許用彎曲應力表可得 45 號正火鋼的 。??8 1[]5MPa???1[]ca???因此,該軸的強度滿足設計要求。3.4.2 主軸箱中齒輪的校核計算一般只對主軸箱中承受載荷最大,最薄弱的齒輪進行接觸強度和彎曲強度的驗算。由于軸 2 上的小齒輪和軸 3 上的大齒輪嚙合,軸 3 上的小齒輪又和軸 4 上的模數更大的齒輪嚙合,所以軸 2 上的小齒輪承受的扭矩最大,故校核軸 2 與軸 3 上嚙合的模數 m 為 3 的一對齒輪。(1)齒輪的材料、精度和齒數 因傳遞功率不大,轉速不高,材料按文獻[8]表 7-1 選取,都采用 45 鋼,鍛造毛坯,大齒輪正火處理,小齒輪調質,均用軟齒面。齒輪精度用 8 級,輪齒表面粗糙度為 =1.6。軟齒面閉式傳動,失效形式為點蝕,考慮傳動平穩(wěn)性,齒數宜取多aR些,取 =38, Z2=46。1Z(2)校核計算(a)設計準則 按齒面接觸疲勞強度設計,再按齒根彎曲疲勞強度校核。(b)按齒面接觸疲勞強度校核 已知 32479.8MNm?4 201453.6i Nm???根據文獻 圖 7-6 齒面接觸疲勞極限選取材料的接觸疲勞極限應力為??8MPaPaHH60li2lim1??,根據文獻 圖 7-7 選取的彎曲疲勞極限應力為:??MFF1230limli ??,應力循環(huán)次數 N 根據文獻 公式(7-3)計算??888121 1024.6./09./ 96)3(26???uatn則根據文獻 圖 7-8 查得接觸疲勞壽命系數 。??8 2.5NZ,根據文獻 圖 7-9 查得彎曲疲勞壽命系數 。1Y,根據文獻 表 7-2 查得接觸疲勞安全系數 ,彎曲疲勞安全系數?? minHS?又 試選 。min1.4FS?2.0STY1.3tK?根據文獻[8]式(7-1) 、 (7-2)求許用接觸應力和許用彎曲應力:23???? MPaYSPaZSNFTFNH304.1208.3695802minl21il12minl21il1 ???????smdv /.6.31061??sz /23.0/4.2/1 ??根據文獻 圖 7-10 得 ;??81vK根據文獻 表 7-3 查得 ;A根據文獻 表 7-4 查得 ;??.8?取 則 。,1??K1.0.3????V根據文獻 表 7-6 取標準模數 =3mm ;??8m根據文獻 表 7-5,得彈性影響系數 。8.9EZMPa又 b=24mm,K=1.1, mm16dz(3-6)???21)(bdKTEH??=2.5×188.9×0.9× 64.1)(253.??=276.1MPa][limH??因此,滿足強度要求。(3)校核齒根彎曲疲勞強度根據文獻 圖 7-18 查得 , ,取??814.2FSY?.0FS.7Y??根據文獻 式( 7-12)校核大小齒輪的彎曲強度(3-7)MPamZKTFSdF .35.0.22131 ??????][.1MPa??][74.12.432122 FFSF PaY?????6110 連桿鉆小頭孔組合機床設計24因此,此齒輪適合要求3.4.3 主軸箱中軸承的校核計算因主軸上的軸承承受的軸向力最大,且承受的扭矩也較大,故校核主軸 1 上的一對軸承。已知 。2384.aFN?(1)計算軸承所受徑向力主軸 1 上的受力情況如圖 3-3 所示。圖 3-3 主軸 1 的受力圖根據文獻 公式 7-6 主軸 1 上輪齒的受力大小可算得??8(3-8)12063.54.tTFNd???tg =354.4×tg20=129N (3-9) rt?根據力矩平衡關系可知 NFrr12921??03.7(03.746)rr??經計算得 =39.64N, =89.36N。12r根據力矩平衡關系可知 NFtH.521??03.7(03746)t??經計算得 =108.9N, =245.5N12H可得2221108.93.6415.9RrFN????25H?(2)計算派生軸向力對 30204 型軸承,根據文獻[9]表 7-2-79,有 e=0.35,Y=1.7。則(3-10) NYFRS 1.347.2951????25NYFRS 84.76.122????(3)計算軸承所收的軸向載荷 =76.84Nsa 5.21.3.1??2SF故軸承 1 有被“放松”的趨勢,軸承 2 有被“壓緊”的趨勢,于是=2418.5N?2AF1SaFS1=34.1N(4)計算當量動載荷已查得 e=0.35,故eRA??29.015/.34/1F?6282再根據文獻 表 7-2-79,有 = 1、 =0、 =0.4、 =1.7;又根據文獻??9XY2X2Y表 11-8 得 =1.2~1.8,取中央值 =1.5。軸承的當量動負荷為??8pf pfNYXPAR 85.739.5.)(111 ?????NFfp 9.632).4126140(222 ???(5)計算軸承壽命根據文獻 表 11-6 得 =0.95,根據文獻[9]表 7-2-79 得 =28200N。又??8tf rCε=10/3。得hPCfnLrth 63/1011 8.9)85.7290(86)(67 ??????frth ).()( 3/1022?故軸承 1 的壽命為 ,軸承 2 的壽命為 。這對軸承的工作壽命69.810h?9h為 。根據組合機床的壽命要求,此對軸承滿足要求。3903.5 多軸箱坐標計算(1) 選擇加工基準坐標系 X0Y主軸箱是安裝在動力頭上的,坐標原點放在靠近主軸箱左側的定位銷上,如圖3-4 所示:6110 連桿鉆小頭孔組合機床設計26圖 3-4 基準坐標系定位銷的尺寸是距離主軸箱側面 E=50mm,距主軸箱底邊 H=30.5mm。下面分別計算各主軸及傳動軸的坐標。(2)計算每根軸的坐標主軸 0 的坐標已知為 =0mm, =0mm;1X1Y計算傳動軸坐標時,先算出與主軸有直接傳動關系的傳動軸坐標,然后計算其它傳動軸坐標。根據文獻 第 71 頁圖 4-25,其計算方法如下,結合圖 3-5:??6jiA123B 1JC0ILabc(,)R圖 3-5 主軸和傳動軸坐標關系設 ABX??27ABY??則 2L???21IRJI??因為 00siniaBcL?Ao所以 LBJAIcJI????00231 sincoB????asin還原到 X0Y 坐標系中去,則 c 點坐標:LAJBIYXA????1各主軸、傳動軸及驅動軸的坐標如下表所示。表 3-1 各主軸、傳動軸及驅動軸的坐標坐 標 X(mm) Y(mm)軸 0 0.000 0.000軸 1 -72.826 -94.838軸 2 -39.046 -230.457軸 3 63.403 -311.204軸 4 0.000 -436.918軸 5 -150.000 -520.790軸 6 150.000 -520.790軸 7 88.000 35.791軸 8 250.000 154.210軸 9 -275.000 -630.7903.6 繪制軸坐標檢查圖3.6.1 坐標檢查圖的主要內容6110 連桿鉆小頭孔組合機床設計28(1)通過齒輪嚙合,檢查坐標位置是否正確,檢查主軸轉速及轉向;(2)進一步檢查各零件間有無干涉現象;(3)查潤滑油泵、分油器等附加機構的位置是否合適。3.6.2 坐標檢查圖繪制的順序及要求繪出多軸箱輪廓尺寸和坐標系 XOY。按計算出的坐標值繪制各主軸、傳動軸軸心位置及及主軸外伸部分直徑,并注明軸號及主軸、驅動軸、液壓泵軸的轉速和轉向等。用點劃線繪制各齒輪的分度圓、注明各齒輪齒數、模數、所處排數及變位齒輪的變位量。為了醒目和易于檢查,可用不同顏色細線條畫出 。29四、PLC 控制系統(tǒng)設計4.1 裝置簡介參照設計圖紙,本組合機床需要完成鉆削、快進、工進、快退、液壓啟停、冷卻啟停等操作,其中最主要的是滑臺需要完成如圖 4-1 所示的運動。圖 4-1 滑臺需要完成的工作示意圖機床的控制及工作過程如下:(1)原始狀態(tài)下,按下液壓啟動按鈕,液壓泵開始工作;(2)按下冷卻排屑系統(tǒng)開按鈕,冷卻排屑系統(tǒng)啟動;(3)按下主軸旋轉按鈕,主軸電機啟動;(4)按下快進開始按鈕,控制滑臺運動的電機啟動并加速;(5)滑臺運行壓倒行程開關 SQ1,滑臺開始工進;(6)滑臺運行壓倒行程開關 SQ2,滑臺開始快退;(7)滑臺運行壓倒行程開關 SQ3,滑臺停止運動;(8)按下主軸停止按鈕,主軸停止運動;該機床還設有緊急停止按鈕、主軸與進給停止按鈕、點動快進按鈕、點動快退按鈕、進給停止按鈕、液壓停止按鈕、冷卻排屑系統(tǒng)停止按鈕,該機床還配有照明燈及其開關、控制顯示燈等。4.2 輸入/輸出分析(1)輸入信號為 14 個開關量信號,分別是:主軸旋轉、緊急停止、主軸停止、快進開始、SQ1、SQ2、SQ3、點動快進、點動快退、液壓啟動、進給停止、主軸與進給停止、冷卻排屑開和冷卻排屑關。(2)輸出信號為 6 個開關量信號,分別是 KM0、KM1、KM2、KM3、KM4、KM5。4.3 用戶程序容量估計分析系統(tǒng)控制要求,控制用的程序估計較短。